Process for preparing fluorine-containing high polymer high frequency circuit board material by hydrothermal method
A technology of high-frequency circuit boards and process methods, which is applied in the direction of circuit substrate materials, chemical instruments and methods, printed circuit components, etc., can solve the problems of high price and inability to meet the needs of high-frequency circuits, and achieve the goal of improving bonding performance Effect
- Summary
- Abstract
- Description
- Claims
- Application Information
AI Technical Summary
Problems solved by technology
Method used
Examples
Embodiment 1
[0026] A. Mix 2.048L polytetrafluoroethylene emulsion (PTFE), 1.024L polyfluoroethylene propylene emulsion (FEP), and 3.926L tetrafluoroethylene-perfluoron-propyl vinyl ether copolymer emulsion (PFA) After mixing thoroughly, first add 897.4g zirconium nitrate Zr (NO 3 ) 4 and 434.4g calcium nitrate Ca (NO 3 ) 2 , then add 80g of diisopropylamine and 70g of isopropanol, and mix to obtain a mixed emulsion.
[0027] The concentration of the polytetrafluoroethylene emulsion (PTFE) is 50% (w), the concentration of the polyperfluoroethylene propylene emulsion (FEP) is 50% (w), tetrafluoroethylene-perfluoro-n-propyl vinyl ether copolymerization The concentration of the polymer emulsion (PFA) is 30% (w).
[0028] B. Put the mixed emulsion prepared in step A into a 10L high-pressure reactor, and the filling ratio is 70.5%. After heating up to 200°C at a heating rate of 1°C / min, react for 48 hours under a pressure of 4Mpa to obtain a polymer package Substances coated with nanoparti...
Embodiment 2
[0036] A. Mix 1.982L polytetrafluoroethylene emulsion (PTFE), 1.038L polyfluoroethylene propylene emulsion (FEP), and 3.980L tetrafluoroethylene-perfluoron-propyl vinyl ether copolymer emulsion (PFA) After mixing thoroughly, first add 1.1164kg of barium nitrate Ba (NO 3 ) 2 and 1.4538kg orthobutyl titanate C 16 h 36 o 4 Ti, add 90g diisopropylamine and 80g 3-isooctyl mercaptopropionate (IOMP) again, mix to obtain mixed emulsion.
[0037] The concentration of the polytetrafluoroethylene emulsion (PTFE) is 50% (w), the concentration of the polyperfluoroethylene propylene emulsion (FEP) is 50% (w), tetrafluoroethylene-perfluoro-n-propyl vinyl ether copolymerization The concentration of the polymer emulsion (PFA) is 30% (w).
[0038] B. Put the mixed emulsion prepared in step A into a 10L high-pressure reactor, and the filling ratio is 72.6%. After heating up to 180°C at a heating rate of 0.5°C / min, react for 36 hours under a pressure of 5Mpa to obtain a polymer package Subs...
Embodiment 3
[0046] A. Mix 1.920L polytetrafluoroethylene emulsion (PTFE), 1.047L polyfluoroethylene propylene emulsion (FEP), and 4.030L tetrafluoroethylene-perfluoron-propyl vinyl ether copolymer emulsion (PFA) After mixing thoroughly, first add 1.3802kg of calcium nitrate Ca (NO 3 ) 2 , 1.4305kg butyl orthotitanate C 16 h 36 o 4 Ti and 1.418kg zirconium nitrate Zr(NO 3 ) 4 , then add 100g of diisopropylamine and 90g of alkyl mercaptan, and mix to obtain a mixed emulsion.
[0047] The concentration of the polytetrafluoroethylene emulsion (PTFE) is 50% (w), the concentration of the polyperfluoroethylene propylene emulsion (FEP) is 50% (w), tetrafluoroethylene-perfluoro-n-propyl vinyl ether copolymerization The concentration of the polymer emulsion (PFA) is 30% (w).
[0048] B. Put the mixed emulsion prepared in step A into a 10L high-pressure reactor, and the filling ratio is 73.4%. After heating up to 220°C at a heating rate of 1.5°C / min, react for 24 hours under a pressure of 6.5...
PUM
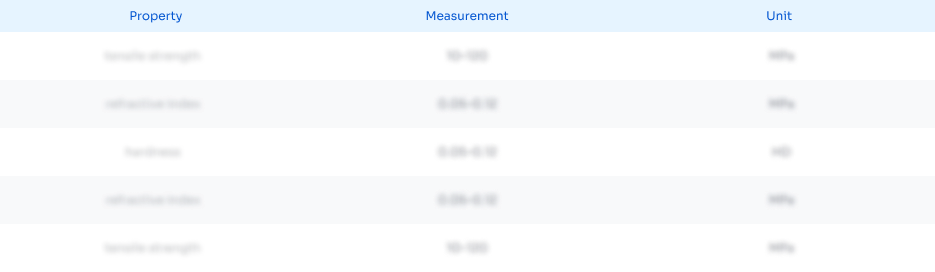
Abstract
Description
Claims
Application Information

- Generate Ideas
- Intellectual Property
- Life Sciences
- Materials
- Tech Scout
- Unparalleled Data Quality
- Higher Quality Content
- 60% Fewer Hallucinations
Browse by: Latest US Patents, China's latest patents, Technical Efficacy Thesaurus, Application Domain, Technology Topic, Popular Technical Reports.
© 2025 PatSnap. All rights reserved.Legal|Privacy policy|Modern Slavery Act Transparency Statement|Sitemap|About US| Contact US: help@patsnap.com