Method for preparing cyclopentadiene through continuous depolymerization and rectification
A technology for cyclopentadiene and dicyclopentadiene, which is applied in the field of preparing high-purity cyclopentadiene by a liquid-phase indirect continuous depolymerization method, can solve the problems of difficult recovery of inert diluent heat-conducting oil, hindered equipment operation, etc. Low, easy-to-control, simple-to-equip effect
- Summary
- Abstract
- Description
- Claims
- Application Information
AI Technical Summary
Problems solved by technology
Method used
Image
Examples
Embodiment 1
[0019] First, add pure heat transfer oil and composite polymerization inhibitor with a weight ratio of 1:0.005 to the thermal decomposer 2 and rectification reboiler 6, and then pass in nitrogen to replace the air in the system, heat the heat transfer oil to 270°C, and then pass the metering The pump adds crude dicyclopentadiene (83.5% by mass) from the bottom of the thermal decomposer to the thermal decomposer, contacts with high-temperature heat transfer oil, and controls the feed rate so that it stays in the thermal decomposer for 2.0S, dicyclopentadiene Diene gasification, depolymerized cyclopentadiene enters rectification column 3 for rectification, and the high-purity cyclopentadiene separated from the top of the tower enters collector 5 through condenser 4 (preserved at low temperature), and a small amount of uncracked cyclopentadiene Dicyclopentadiene and by-products are heated in the bottom reboiler 6 and rectified again. The composite inhibitor is a compound of hydro...
Embodiment 2
[0022] First, add pure heat transfer oil and composite polymerization inhibitor with a weight ratio of 1:0.008 to the thermal decomposer 2 and rectification reboiler 6, and then pass in nitrogen to replace the air in the system, heat the heat transfer oil to 280°C, and then pass the metering The pump adds crude dicyclopentadiene (83.5% by mass) from the bottom of the thermal decomposer to the thermal decomposer, contacts with high-temperature heat transfer oil, and controls the feed rate so that it stays in the thermal decomposer for 2.0S, dicyclopentadiene Diene gasification, depolymerized cyclopentadiene enters rectification column 3 for rectification, and the high-purity cyclopentadiene separated from the top of the tower enters collector 5 through condenser 4 (preserved at low temperature), and a small amount of uncracked cyclopentadiene Dicyclopentadiene and by-products are heated in the bottom reboiler 6 and rectified again. The complex polymerization inhibitor is a comp...
Embodiment 3
[0025] First, add pure heat transfer oil and composite polymerization inhibitor with a weight ratio of 1:0.01 to the thermal decomposer 2 and rectification reboiler 6, and then pass in nitrogen to replace the air in the system, heat the heat transfer oil to 280°C, and then pass the metering The pump adds crude dicyclopentadiene (92.7% by mass) from the bottom of the thermal decomposer to the thermal decomposer, contacts with high-temperature heat transfer oil, and controls the feed rate so that it stays in the thermal decomposer for 1.5S. Diene gasification, depolymerized cyclopentadiene enters rectification column 3 for rectification, and the high-purity cyclopentadiene separated from the top of the tower enters collector 5 through condenser 4 (preserved at low temperature), and a small amount of uncracked cyclopentadiene Dicyclopentadiene and by-products are heated in the bottom reboiler 6 and rectified again. The complex polymerization inhibitor is a compound of 4-tert-buty...
PUM
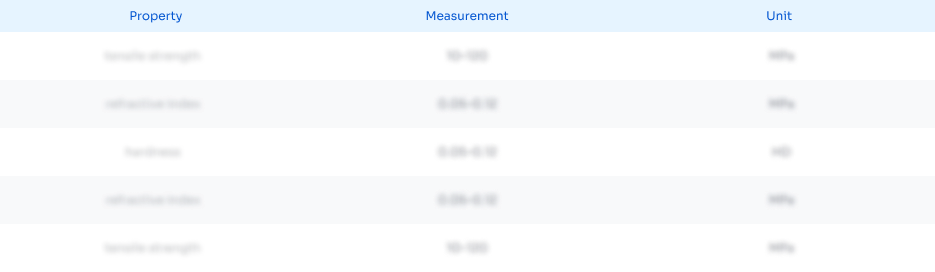
Abstract
Description
Claims
Application Information

- R&D
- Intellectual Property
- Life Sciences
- Materials
- Tech Scout
- Unparalleled Data Quality
- Higher Quality Content
- 60% Fewer Hallucinations
Browse by: Latest US Patents, China's latest patents, Technical Efficacy Thesaurus, Application Domain, Technology Topic, Popular Technical Reports.
© 2025 PatSnap. All rights reserved.Legal|Privacy policy|Modern Slavery Act Transparency Statement|Sitemap|About US| Contact US: help@patsnap.com