Lithium ion battery anode material with LiCoO2 coated on surface and preparation method for lithium ion battery anode material
A surface-coated lithium cobalt oxide and lithium-ion battery technology, which is applied to battery electrodes, circuits, electrical components, etc., can solve problems such as poor low-temperature performance, poor high-temperature storage performance, and deterioration of cycle performance, and achieve easy industrial production, The process is easy to control and the effect of shortening the roasting time
- Summary
- Abstract
- Description
- Claims
- Application Information
AI Technical Summary
Problems solved by technology
Method used
Image
Examples
Embodiment 1
[0033] Embodiment 1: Take by weighing 50g lithium ion battery cathode material LiNi 0.8 co 0.15 al 0.05 o 2 Substrate, by LiCoO 2 Add cobalt nitrate and lithium nitrate to 3% of the weight of the substrate, and then add KCl according to substrate: KCl=1:1 (mass ratio), mix evenly, bake at 750°C for 2 hours, cool to room temperature with the furnace, and use Wash with deionized water three times, and then dry at 200 °C for 3 h to obtain LiCoO 2 The coating amount is 3wt.% positive electrode material.
[0034] LiNi 0.8 co 0.15 al 0.05 o 2 Surface coated with 3wt.% LiCoO 2 SEM pictures before and after figure 1 Shown, visible, coated with 3wt.% LiCoO 2 After LiNi 0.8 co 0.15 al 0.05 o 2 Many nano-scale small particles are obviously attached to the surface of the primary particle of the substrate. LiNi 0.8 co 0.15 al 0.05 o 2 Surface coated with 3wt.% LiCoO 2 XRD pictures before and after figure 2 As shown, it can be seen that the crystal structure has not c...
Embodiment 2
[0035] Embodiment 2: take by weighing 50g lithium ion battery cathode material LiNi 0.8 co 0.15 al 0.05 o 2 Substrate, by LiCoO 2 The weight accounts for 7% of the base material, and cobalt sulfate and lithium hydroxide are added, and then KCl is added according to the base material: KCl=1:2 (mass ratio), mixed evenly, roasted at 800 ° C for 3 hours, and cooled to room temperature with the furnace. Wash 4 times with deionized water, and then dry at 250 °C for 2 h to obtain LiCoO 2 The coating amount is 7wt.% positive electrode material.
Embodiment 3
[0036] Embodiment 3: take by weighing 50g lithium ion battery cathode material LiNi 0.8 co 0.15 al 0.05 o 2 Substrate, by LiCoO 2 The weight accounts for 10% of the base material, and cobalt carbonate and lithium carbonate are added, and then NaCl is added according to the base material: NaCl=1:3 (mass ratio), mixed evenly, roasted at 850 ° C for 4 hours, and cooled to room temperature with the furnace, and then used Wash with deionized water 4 times, and then dry at 300 °C for 3 h to obtain LiCoO 2 The coating amount is 10wt.% positive electrode material.
PUM
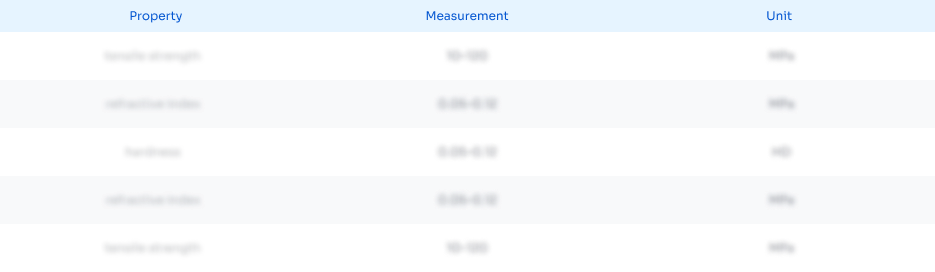
Abstract
Description
Claims
Application Information

- R&D
- Intellectual Property
- Life Sciences
- Materials
- Tech Scout
- Unparalleled Data Quality
- Higher Quality Content
- 60% Fewer Hallucinations
Browse by: Latest US Patents, China's latest patents, Technical Efficacy Thesaurus, Application Domain, Technology Topic, Popular Technical Reports.
© 2025 PatSnap. All rights reserved.Legal|Privacy policy|Modern Slavery Act Transparency Statement|Sitemap|About US| Contact US: help@patsnap.com