Polyborazine ceramic precursor and preparation method thereof
A technology of ceramic precursors and polyborazane, which is applied in the field of polyborazane ceramic precursors and its preparation, can solve the problems of low boron content, difficulty in exerting the excellent performance of boron atoms, low activity, etc., and achieve simple preparation equipment , High utilization rate, rich source of monomer
- Summary
- Abstract
- Description
- Claims
- Application Information
AI Technical Summary
Problems solved by technology
Method used
Image
Examples
example 1
[0018] Example 1: 0.1 mole of 1,3 propylenediamine in 100 mL of DMF was added to a 250 mL three-neck flask under nitrogen protection, and 0.06 mole of boron trifluoride in ether was slowly added thereto under stirring at -10°C. After the dropwise addition, the system was reacted at 0° C. for 10 h, then heated to 60° C. and reacted at this temperature for 4 h. Then react at 150°C for 24h. After the reaction, the solvent was distilled off under reduced pressure. The obtained substance was dissolved-precipitated three times with ethanol-anhydrous ether, and vacuum-dried at 60° C. for 24 hours to obtain the target polymer as a pale yellow solid with a yield of 65%.
example 2
[0019] Example 2: Add 0.15 moles of p-phenylenediamine in 100 mL of sulfolane solution into a 250 mL three-neck flask under nitrogen protection, and slowly add 0.05 moles of boron trifluoride in ether to it under stirring at 0°C. After the dropwise addition, the system was reacted at 5°C for 6h, then heated to 80°C and reacted at this temperature for 4h. Then react at 120°C for 12h and at 200°C for 8h. After the reaction, the solvent was distilled off under reduced pressure. The obtained substance was dissolved-precipitated three times with ethanol-anhydrous ether, and vacuum-dried at 60° C. for 24 hours to obtain the target polymer as a pale yellow solid with a yield of 78%.
example 3
[0020] Example 3: Under nitrogen protection, 0.20 moles of p-phenylenediamine in 100 mL of dimethyl sulfoxide solution was added to a 250 mL three-necked flask, and 0.05 moles of boron trichloride in toluene was slowly added thereto under stirring at -10°C solution. After the dropwise addition, the system was reacted at 5°C for 2h, then heated to 80°C and reacted at this temperature for 4h. Then react at 120°C for 12h and at 160°C for 24h. After the reaction, the solvent was distilled off under reduced pressure. The resulting substance was precipitated three times with ethanol-anhydrous ether, and dried under vacuum at 60° C. for 24 hours to obtain the target polymer as a pale yellow solid with a yield of 81%.
PUM
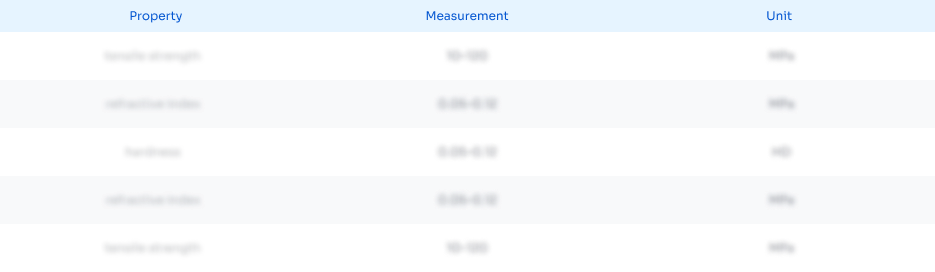
Abstract
Description
Claims
Application Information

- R&D
- Intellectual Property
- Life Sciences
- Materials
- Tech Scout
- Unparalleled Data Quality
- Higher Quality Content
- 60% Fewer Hallucinations
Browse by: Latest US Patents, China's latest patents, Technical Efficacy Thesaurus, Application Domain, Technology Topic, Popular Technical Reports.
© 2025 PatSnap. All rights reserved.Legal|Privacy policy|Modern Slavery Act Transparency Statement|Sitemap|About US| Contact US: help@patsnap.com