Processing technique of ethyl difluoroacetate
A technology of ethyl difluoroacetate and production process, applied in the field of production technology of ethyl difluoroacetate, can solve the problems of low total yield, equipment corrosion, long process flow, etc., and achieves improved production yield and industrialized production. , the effect of increasing the reaction rate
- Summary
- Abstract
- Description
- Claims
- Application Information
AI Technical Summary
Problems solved by technology
Method used
Image
Examples
example 1
[0028] In a 1000ml reaction bottle, put 80g of diethylamine and 400ml of toluene respectively, lower the temperature, add 138g of dichloroacetyl chloride dropwise under 10°C for 1 hour, the dropwise addition is completed, keep the reaction for 2 hours, filter, and the filtrate is decompressed to recover toluene, reduce 160g of dichloroacetyldiethylamine was collected by pressure distillation at 95-110°C / 20mmHg. Yield: 93.1%.
[0029] Put 125g of dichloroacetyldiethylamine, 110g of anhydrous potassium fluoride, 5g of catalyst tetrabutylammonium bromide, and 230g of solvent sulfolane into a 500ml reaction bottle, start stirring, heat up, and keep warm at 145-150°C for 6 hours , after the reaction was completed, it was lowered to room temperature, filtered, and the filtrate was collected under reduced pressure at 120-130° C. / 20 mmHg fraction to obtain 86.7 g of difluoroacetyldiethylamine, yield: 84.5%.
[0030] Put 260g of difluoroacetyldiethylamine into a 500ml reaction bottle,...
example 2
[0032] In a 1000ml reaction bottle, put 80g of diethylamine and 400ml of toluene respectively, lower the temperature, add 138g of dichloroacetyl chloride dropwise under 10°C for 1 hour, the dropwise addition is completed, keep the reaction for 2 hours, filter, and the filtrate is decompressed to recover toluene, reduce 160g of dichloroacetyldiethylamine was collected by pressure distillation at 95-110°C / 20mmHg. Yield: 93.1%.
[0033] Put 125g of dichloroacetyldiethylamine, 100g of anhydrous potassium fluoride, 5g of catalyst tetrabutylammonium bromide, and 250g of recovered sulfolane into a 500ml reaction bottle, start stirring, raise the temperature, and keep warm at 145-150°C for 6 hours , after the reaction was completed, lowered to room temperature, filtered, and the filtrate was collected under reduced pressure at 120-130° C. / 20 mmHg fraction to obtain 85.3 g of difluoroacetyldiethylamine, yield: 83.1%.
[0034] Put 260g of difluoroacetyldiethylamine into a 500ml reactio...
example 3
[0036] In a 1000ml reaction bottle, put 80g of diethylamine and 400ml of toluene respectively, lower the temperature, add 138g of dichloroacetyl chloride dropwise under 10°C for 1 hour, the dropwise addition is completed, keep the reaction for 2 hours, filter, and the filtrate is decompressed to recover toluene, reduce 160g of dichloroacetyldiethylamine was collected by pressure distillation at 95-110°C / 20mmHg. Yield: 93.1%.
[0037]Put 125g of dichloroacetyldiethylamine, 120g of anhydrous potassium fluoride, 5g of catalyst tetrabutylammonium bromide, and 250g of recovered sulfolane into a 500ml reaction bottle, start stirring, heat up, and keep warm at 145-150°C for 6 hours , after the reaction was completed, lowered to room temperature, filtered, and the filtrate was collected under reduced pressure at 120-130° C. / 20 mmHg fraction to obtain 88.5 g of difluoroacetyldiethylamine, yield: 86.2%.
[0038] Put 260g of difluoroacetyldiethylamine into a 500ml reaction bottle, add 2...
PUM
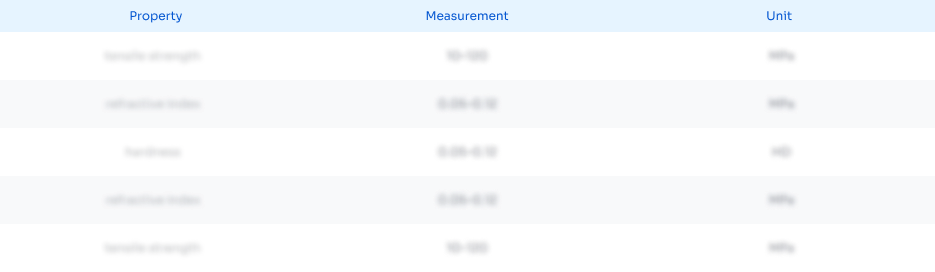
Abstract
Description
Claims
Application Information

- R&D
- Intellectual Property
- Life Sciences
- Materials
- Tech Scout
- Unparalleled Data Quality
- Higher Quality Content
- 60% Fewer Hallucinations
Browse by: Latest US Patents, China's latest patents, Technical Efficacy Thesaurus, Application Domain, Technology Topic, Popular Technical Reports.
© 2025 PatSnap. All rights reserved.Legal|Privacy policy|Modern Slavery Act Transparency Statement|Sitemap|About US| Contact US: help@patsnap.com