The method that adopts composite ionic liquid catalyst to synthesize tri-n-butyl citrate
A technology of liquid catalysts and compound ions, applied in chemical instruments and methods, organic compound/hydride/coordination complex catalysts, physical/chemical process catalysts, etc., can solve the problem of reaction conversion, catalytic activity, product color lightening wastewater Environmental protection, low acylation reaction temperature, complex production process and other issues, to achieve the effect of reducing the production process time, low reaction temperature, and simple synthesis process
- Summary
- Abstract
- Description
- Claims
- Application Information
AI Technical Summary
Problems solved by technology
Method used
Image
Examples
Embodiment 1
[0049] Such as figure 2 Shown in the flow process: by the production technology of the present invention's synthetic tri-n-butyl citrate (TBC), add 300kg citric acid, 634kg n-butanol, 0.9kg composite catalyst in succession in 1000L esterification reactor and stir, in the reactor jacket Heat the reaction material to 50°C by introducing heat conduction oil, and react for 3 hours until the esterification is qualified (detected by liquid chromatography). In this reaction kettle, direct vacuum distillation at this temperature, and the n-butanol vapor cools down through the condenser. After that, it enters the butanol recovery tank for recycling. The material after the distillation is put into static kettle and emits catalyzer, the material after layering can obtain 491kg of tri-n-butyl citrate (TBC) of colorless transparent liquid product through neutralization, washing under reduced pressure again after layering, through liquid chromatography Detection, the productive rate reach...
Embodiment 2
[0051] Add 300kg of citric acid, 423kg of n-butanol, and 1.5kg of composite catalyst into a 1000L esterification reaction kettle in turn, and stir. Heat conduction oil into the jacket of the reaction kettle to heat the reaction materials to 65°C, and react for 2 hours until the esterification is qualified (by Liquid chromatography detection), other processing conditions are with embodiment 1, obtain colorless transparent liquid product tri-n-butyl citrate (TBC) 488kg, through liquid chromatography detection, productive rate reaches 99.3%. Product performance indicators are shown in Table 1.
Embodiment 3
[0053] Add 250kg of citric acid, 395kg of n-butanol, and 2.0kg of composite catalyst in a 1000L esterification reaction kettle to stir, and heat the reaction material to 110°C by introducing heat transfer oil into the jacket of the reaction kettle, and react for 2.5 hours until the esterification is qualified (by liquid chromatography detection), other processing conditions are with embodiment 1, obtain colorless transparent liquid product tri-n-butyl citrate (TBC) 412kg, through liquid chromatography detection, productive rate reaches 99.6%. Product performance indicators are shown in Table 1.
PUM
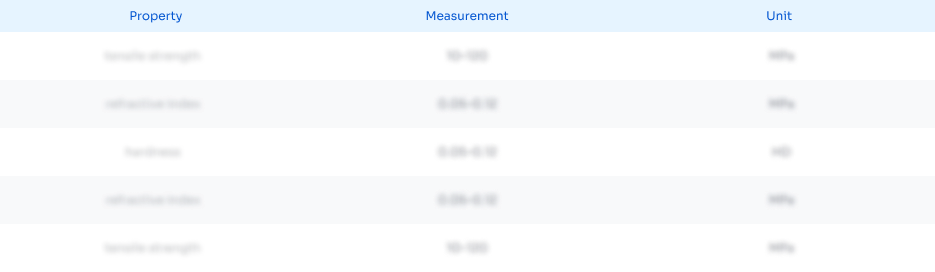
Abstract
Description
Claims
Application Information

- Generate Ideas
- Intellectual Property
- Life Sciences
- Materials
- Tech Scout
- Unparalleled Data Quality
- Higher Quality Content
- 60% Fewer Hallucinations
Browse by: Latest US Patents, China's latest patents, Technical Efficacy Thesaurus, Application Domain, Technology Topic, Popular Technical Reports.
© 2025 PatSnap. All rights reserved.Legal|Privacy policy|Modern Slavery Act Transparency Statement|Sitemap|About US| Contact US: help@patsnap.com