Composite brazing aluminum foil material for automobile radiator and manufacturing method thereof
A technology of automobile radiator and manufacturing method, which is applied in chemical instruments and methods, metal rolling, layered products, etc., can solve problems such as failure to meet collapse resistance, and achieve improved heat resistance, less cracking, and improved corrosion resistance. sexual effect
- Summary
- Abstract
- Description
- Claims
- Application Information
AI Technical Summary
Problems solved by technology
Method used
Examples
Embodiment 1
[0011] The chemical composition mass ratio of the core material is: 0.68% silicon, 0.20% iron, 0.30% copper, 1.15% manganese, 0.010% chromium, 0.15% titanium and the rest is aluminum. Put the industrial pure aluminum ingot (AL99.70A) for remelting into the melting furnace and raise the temperature to 740℃~760℃ to melt and stir. After removing the slag, add iron, copper, manganese, chromium and titanium according to the above ratio After stirring, refining, and adjusting the composition, the agent enters the static furnace. After degassing and slag removal, it is cast at 720°C to 740°C, and then cast into a hot-rolled ingot. The ingot is sawed and milled to form a core. After surface treatment, the core body is covered with a layer of AA4343 composite boards on the upper and lower sides. The thickness of the composite boards accounts for 10% of the total thickness. It is heated to 520°C to 540°C and kept for 10 hours before hot rolling to obtain hot-rolled slabs. The hot-rolled...
Embodiment 2
[0013] The chemical composition mass ratio of the core material is: 0.68% silicon, 0.25% iron, 0.35% copper, 1.25% manganese, 0.020% chromium, 0.18% titanium, and the rest is aluminum. Put the industrial pure aluminum ingot (AL99.70A) for remelting into the melting furnace and raise the temperature to 740℃~760℃ to melt and stir. After removing the slag, add iron, copper, manganese, chromium and titanium according to the above ratio After stirring, refining, and adjusting the composition, the agent enters the static furnace. After degassing and slag removal, it is cast at 720°C to 740°C, and then cast into a hot-rolled ingot. The ingot is sawed and milled to form a core. After surface treatment, the core body is covered with a layer of AA4343 composite boards on the upper and lower sides. The thickness of the composite boards accounts for 10% of the total thickness. It is heated to 520°C to 540°C and kept for 10 hours before hot rolling to obtain hot-rolled slabs. The hot-rolle...
Embodiment 3
[0015] The chemical composition mass ratio of the core material is: 0.75% silicon, 0.25% iron, 0.35% copper, 1.35% manganese, 0.028% chromium, 0.20% titanium, and the rest is aluminum. Put the industrial pure aluminum ingot (AL99.70A) for remelting into the melting furnace and raise the temperature to 740℃~760℃ to melt and stir. After removing the slag, add iron, copper, manganese, chromium and titanium according to the above ratio After stirring, refining, and adjusting the composition, the agent enters the static furnace. After degassing and slag removal, it is cast at 720°C to 740°C, and then cast into a hot-rolled ingot. The ingot is sawed and milled to form a core. After surface treatment, the core body is covered with a layer of AA4343 composite boards on the upper and lower sides. The thickness of the composite boards accounts for 10% of the total thickness. It is heated to 520°C to 540°C and kept for 10 hours before hot rolling to obtain hot-rolled slabs. The hot-rolle...
PUM
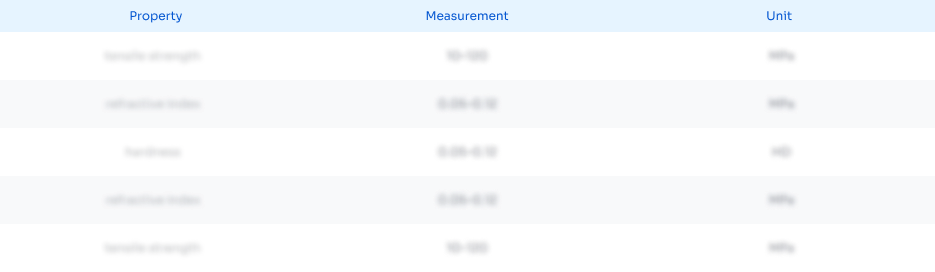
Abstract
Description
Claims
Application Information

- Generate Ideas
- Intellectual Property
- Life Sciences
- Materials
- Tech Scout
- Unparalleled Data Quality
- Higher Quality Content
- 60% Fewer Hallucinations
Browse by: Latest US Patents, China's latest patents, Technical Efficacy Thesaurus, Application Domain, Technology Topic, Popular Technical Reports.
© 2025 PatSnap. All rights reserved.Legal|Privacy policy|Modern Slavery Act Transparency Statement|Sitemap|About US| Contact US: help@patsnap.com