Continuous Casting Process of Steel for High Titanium Alloy Welding Rod
A technology of steel and titanium alloy for welding electrodes, applied in the field of metallurgy, can solve the problems of increased basicity, melting point, viscosity, crystallization performance of mold slag, poor surface quality of casting billet, and variability of mold slag, etc., so as to ensure stability, Good quality, prevent denaturation effect
- Summary
- Abstract
- Description
- Claims
- Application Information
AI Technical Summary
Problems solved by technology
Method used
Examples
Embodiment 1
[0018] A continuous casting protective pouring process of steel for high titanium alloy welding rods, comprising the following steps:
[0019] ⑴Before the casting machine starts pouring, put the mold slag into the mold slag baking furnace for baking, the baking temperature is controlled at 130°C, and the baking time is 30 minutes to ensure that the mold slag is dry and preheated; the mold slag is determined by weight percentage Composition of: SiO 2 : 35.65%, CaO: 30.85%, Al 2 o 3 : 4.0%, Fe 2 o 3 : 3.5%, MgO: 4.5%, F - : 4.5%, K 2 O+Na 2 O: 5.0%, solid C: 12.0%; R (is alkalinity, CaO / SiO 2 Ratio): 0.87; the physical indicators of mold flux are: melting point (°C): 1045, viscosity (Pa.s / 1300°C): 0.28, moisture 0.3%, particle size (0.15-1mm) 80%, bulk density (g / cm 3 ): 0.5.
[0020] ⑵Continuous casting adopts full protection pouring, ladle to tundish adopts long nozzle argon seal protection pouring, tundish to crystallizer adopts integral built-in submerged nozzle pro...
Embodiment 2
[0025] A continuous casting protective pouring process of steel for high titanium alloy welding rods, comprising the following steps:
[0026] ⑴Before the casting machine starts pouring, put the mold slag into the mold slag baking furnace for baking, the baking temperature is controlled at 140°C, and the baking time is 40min to ensure that the mold slag is dry and preheated; the mold slag is determined by weight percentage Composition of: SiO 2 : 38.5%, CaO: 28.5%, Al 2 o 3 : 3.5%, Fe 2 o 3 : 3.0%, MgO: 4.0%, F - (F- Indicates fluoride ion): 6%, K 2 O+Na 2 O: 7%, solid C: 9.5%; R (is alkalinity, CaO / SiO 2 Ratio): 0.74; the physical indicators of mold flux are: melting point (°C): 1080, viscosity (Pa.s / 1300°C): 0.43, moisture 0.4%, particle size (0.15-1mm) 90%, bulk density (g / cm 3 ): 0.70.
[0027] ⑵Continuous casting adopts full protection pouring, ladle to tundish adopts long nozzle argon seal protection pouring, tundish to crystallizer adopts integral built-in subm...
Embodiment 3
[0032] A continuous casting protective pouring process of steel for high titanium alloy welding rods, comprising the following steps:
[0033] ⑴Before the casting machine starts pouring, put the mold slag into the mold slag baking furnace for baking, the baking temperature is controlled at 150°C, and the baking time is 50 minutes to ensure that the mold slag is dry and preheated; the mold slag is determined by weight percentage Composition of: SiO 2 : 33.5%, CaO: 32%, Al 2 o 3 : 5.0%, Fe 2 o 3 : 4.0%, MgO: 5.0%, F - : 3%, K 2 O+Na 2 O: 3.0%, solid C: 14.5%; R (is alkalinity, CaO / SiO 2 Ratio): 0.96%; the physical indicators of mold flux are: melting point (°C): 1115, viscosity (Pa.s / 1300°C): 0.58, moisture 0.5%, particle size (0.15-1mm) 80%, bulk density (g / cm 3 ): 0.9.
[0034] ⑵Continuous casting adopts full protection pouring, ladle to tundish adopts long nozzle argon seal protection pouring, tundish to crystallizer adopts integral built-in submerged nozzle protec...
PUM
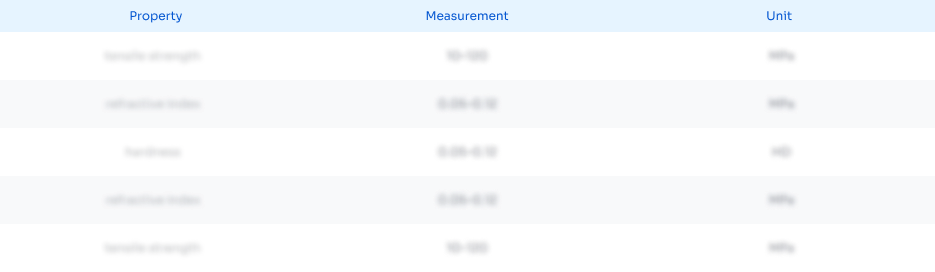
Abstract
Description
Claims
Application Information

- R&D
- Intellectual Property
- Life Sciences
- Materials
- Tech Scout
- Unparalleled Data Quality
- Higher Quality Content
- 60% Fewer Hallucinations
Browse by: Latest US Patents, China's latest patents, Technical Efficacy Thesaurus, Application Domain, Technology Topic, Popular Technical Reports.
© 2025 PatSnap. All rights reserved.Legal|Privacy policy|Modern Slavery Act Transparency Statement|Sitemap|About US| Contact US: help@patsnap.com