A short-process and high-efficiency production method for brass pipes
A production method and short process technology, applied in the direction of rolling force/roll gap control, etc., can solve the problems of high energy consumption, low product quality, small production capacity, etc., to achieve high energy utilization, reduce production costs, and reduce energy The effect of consumption
- Summary
- Abstract
- Description
- Claims
- Application Information
AI Technical Summary
Problems solved by technology
Method used
Examples
Embodiment 1
[0020] Example 1: The production method of brass straight pipe with the size of Ф45×5mmH96
[0021] ①A pipe billet with a diameter of Ф120×30mm is prepared by horizontal continuous casting of hot and cold combined molds. The melting temperature of the copper alloy liquid is 1180°C, the holding temperature is 1200°C, the temperature of the hot mold (mold heating) is 1180°C, and resistance heating is adopted, with a heating power of 5kW. The cooling water (water-cooled copper sleeve) flow rate is 1000L / h, and the traction speed is 150mm / min.
[0022] ② The tube blank prepared in step 1 is subjected to 4-8 passes of three-roller periodic cold rolling, with an average deformation of 20%, and the deformation of each pass gradually decreases with the increase of cumulative deformation. Intermediate annealing may not be performed during the manufacturing process.
[0023] ③Bright annealing is carried out on the rolled pipe, the annealing temperature is 500°C, the annealing time is...
Embodiment 2
[0024] Example 2: The production method of brass straight pipe with the size of Ф10×0.5mmH80
[0025] ①Using hot-cold combination casting mold horizontal continuous casting to prepare tube billets with a diameter of Ф50×5mm, the melting temperature of the copper alloy liquid is 1100°C, the holding temperature is 1120°C, the hot mold (mold heating) temperature is 1100°C, resistance heating is used, and the heating power is 3kW. The cooling water (water-cooled copper sleeve) flow rate is 450L / h, and the traction speed is 200mm / min.
[0026] ② Carry out one planetary rolling on the tube blank prepared in step 1, and the total deformation amount is 90-95%.
[0027] ③Bright annealing is carried out on the rolled pipe, the annealing temperature is 400°C, the annealing time is 30min, the gas protection atmosphere in the furnace is 2% hydrogen + the balance nitrogen, and the pipe is purged with pure nitrogen gas, and the purge gas is continuously fed in, and the initial purge The s...
Embodiment 3
[0028] Example 3: The production method of the H80 brass coil with a size of Ф30×2mm
[0029] ①A pipe billet with a diameter of Ф100×15mm is prepared by horizontal continuous casting of a hot-cold combined mold. The melting temperature of the copper alloy liquid is 1100°C, the holding temperature is 1120°C, and the temperature of the hot mold (mold heating) is 1100°C. Resistance heating is used, and the heating power is 3kW. Cooling water (water-cooled copper sleeve) flow rate is 700L / h, traction speed is 150mm / min.
[0030] ② Carry out one planetary rolling on the tube blank prepared in step 1, with a total deformation of 40% to 90%.
[0031] ③ The rolled tube blank is subjected to 1-3 passes of series drawing or triple drawing, with a deformation of 15% to 25%, the purpose of which is to finish the pipe before coil drawing.
[0032] ④ Use an inverted coil machine for coil pulling, with an average pass elongation coefficient of 1.4, stretching passes of 3 to 4 passes, and ...
PUM
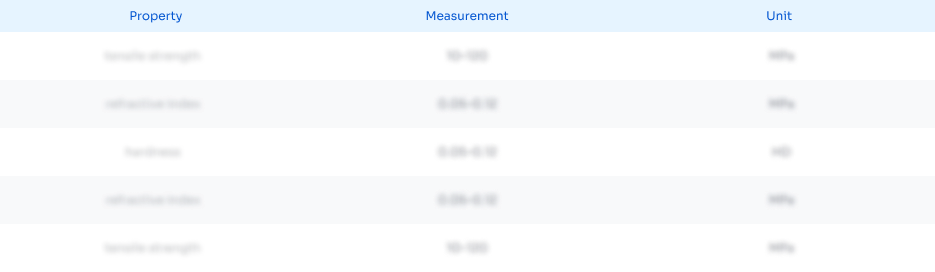
Abstract
Description
Claims
Application Information

- Generate Ideas
- Intellectual Property
- Life Sciences
- Materials
- Tech Scout
- Unparalleled Data Quality
- Higher Quality Content
- 60% Fewer Hallucinations
Browse by: Latest US Patents, China's latest patents, Technical Efficacy Thesaurus, Application Domain, Technology Topic, Popular Technical Reports.
© 2025 PatSnap. All rights reserved.Legal|Privacy policy|Modern Slavery Act Transparency Statement|Sitemap|About US| Contact US: help@patsnap.com