Poly(propylene carbonate)-based polyurethane fireproof coating and preparation method thereof
A polypropylene carbonate-based water-based, polypropylene carbonate technology is applied in the field of polypropylene carbonate-based water-based polyurethane fire-retardant coatings and their preparation, and can solve the problem of low proportion of polyurethane fire-retardant coatings, high difficulty and large amount of consumption. And other issues
- Summary
- Abstract
- Description
- Claims
- Application Information
AI Technical Summary
Problems solved by technology
Method used
Examples
Embodiment 1
[0048] (1) Preparation of waterborne polyurethane
[0049] (1) Add 100g of polypropylene carbonate diol with a molecular weight of 3500 into the reaction kettle, vacuum and dehydrate at 100°C for 40 minutes, and cool to 40°C;
[0050] (2) Add 6g of dimethylolpropionic acid and 0.2g of catalyst dibutyltin dilaurate into the reaction kettle under the protection of nitrogen, stir it evenly, and raise the temperature to 60°C;
[0051] (3) Add 20g of toluene diisocyanate TDI into the reaction kettle, the reaction kettle is heated to 70°C, and the reaction is kept warm for 3 hours. According to the viscosity of the reaction system, 15g of acetone can be added to adjust the viscosity of the reaction system during the reaction process;
[0052] (4) Add 2g of 1,4-butanediol to the reactor for chain extension, and the reactor is heated to 80 o C, heat preservation reaction for 2 hours;
[0053] (5) Cool down to room temperature, add 5.2g of γ-aminopropyltriethoxysilane KH-550 to the reaction kett...
Embodiment 2
[0063] (1) Preparation of waterborne polyurethane
[0064] (1) Add 100g of polypropylene carbonate diol with a molecular weight of 3500 into the reaction kettle, vacuum and dehydrate at 100°C for 60 minutes, and cool to 40°C;
[0065] (2) Add 8g of dimethylolpropionic acid and 0.2g of catalyst dibutyltin dilaurate into the reaction kettle under the protection of nitrogen, stir well, and raise the temperature to 60°C;
[0066] (3) Add 30g of 4,4'-diphenylmethane diisocyanate MDI to the reaction kettle, heat the reaction kettle to 80°C, keep the temperature for 4 hours, and add 20g of N methyl during the reaction process according to the viscosity of the reaction system Pyrrolidone adjusts the viscosity of the reaction system;
[0067] (4) Add 3g of 1,6-hexanediol to the reactor for chain extension, and the reactor is heated to 85 o C, heat preservation reaction for 3 hours;
[0068] (5) Cool down to room temperature, add 10g of N-β-aminohexyl-γ-aminopropylmethyldimethoxysilane 602 to th...
Embodiment 3
[0078] (1) Preparation of waterborne polyurethane
[0079] (1) Add 100g of polypropylene carbonate diol with a molecular weight of 3500 into the reactor, vacuum and dehydrate at 100°C for 30 minutes, and cool to 40°C;
[0080] (2) Add 2g of 1,2-dihydroxy-3-propanesulfonic acid and 0.1g of catalyst dibutyltin dilaurate into the reaction kettle under the protection of nitrogen, and after stirring uniformly, the temperature is raised to 60°C;
[0081] (3) Add 15g of isophorone diisocyanate IPDI to the reaction kettle, the reaction kettle is heated to 60°C, and the reaction is kept for 1 hour. According to the viscosity of the reaction system, 10g of acetone can be added to adjust the viscosity of the reaction system during the reaction process;
[0082] (4) Add 1g of ethylenediamine to the reaction kettle for chain extension, and the reaction kettle is heated to 65 o C, heat preservation reaction for 1 hour;
[0083] (5) Cool down to room temperature, add 1 g of 3-glycidoxypropyltrimethoxy...
PUM
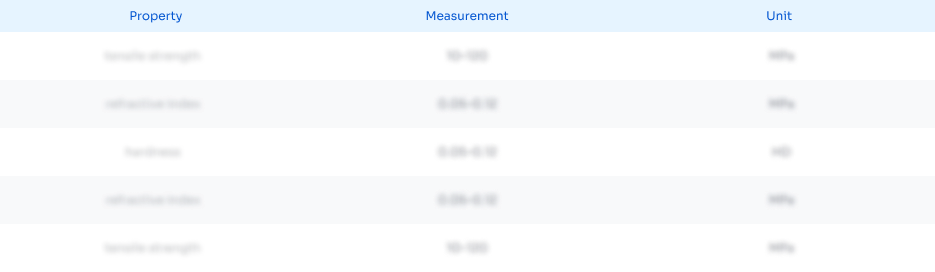
Abstract
Description
Claims
Application Information

- R&D
- Intellectual Property
- Life Sciences
- Materials
- Tech Scout
- Unparalleled Data Quality
- Higher Quality Content
- 60% Fewer Hallucinations
Browse by: Latest US Patents, China's latest patents, Technical Efficacy Thesaurus, Application Domain, Technology Topic, Popular Technical Reports.
© 2025 PatSnap. All rights reserved.Legal|Privacy policy|Modern Slavery Act Transparency Statement|Sitemap|About US| Contact US: help@patsnap.com