Glass sealing material as well as preparation and use methods thereof
A glass sealing and raw material technology, applied in the field of solid oxide fuel cells, can solve the problems of restricting the service life of sealing materials and SOFC, unsolved high temperature stability of materials, mismatch of thermal expansion coefficients, etc. Low cost and the effect of reducing the sealing temperature
- Summary
- Abstract
- Description
- Claims
- Application Information
AI Technical Summary
Problems solved by technology
Method used
Image
Examples
preparation example Construction
[0034] A method for preparing a glass sealing material, comprising uniformly mixing raw materials; melting at 1300-1500°C for 1-4 hours; rapidly cooling the melted glass to obtain a glass frit; and then The glass frit is crushed, ground or ball milled, and the glass sealing material is obtained after sieving.
[0035] A method for using a glass sealing material comprises the following steps:
[0036] 1) Mix the glass sealing material with binder, dispersant and solvent to form a slurry, and disperse it evenly by ball milling in a ball mill; cast it, dry it naturally, and then cut it into the embryo body of the desired shape;
[0037] 2) Place the embryo body at the part to be sealed, raise the temperature in an electric furnace at a rate of 1-5°C / min, keep it at 400-500°C for 0.5-2 hours, and then raise the temperature at a rate of 1-5°C / min to 750 Crystallize at -850°C for 0.5-2 hours, then cool down to the working temperature of the solid oxide fuel cell at a rate of 1-3°C / ...
Embodiment 1
[0041] Embodiment 1: Preparation and sealing of materials
[0042] according to Figure 8 The ratio of each component, weigh a certain amount of analytically pure raw materials (CaO, SrO, SiO 2 、Al 2 o 3 、B 2 o 3 , Ga 2 o 3 ), and mixed evenly with a planetary ball mill for 24 hours; then put the powder into a platinum crucible, place it in the air atmosphere of a box-type resistance furnace, heat it to 1300°C at 3°C / min, and keep it warm for 1 hour; then, take out the crucible, Pour the melt into deionized water for rapid cooling, and dry to obtain fragments of glass melt; grind and pass through a 100-mesh sieve to obtain glass powder. Mix glass powder with polyvinyl alcohol, fish oil, ethanol and toluene (80%, 2%, 1%, 10%, 7% by weight) to form a slurry, and disperse evenly in a ball mill; tape casting, natural Dry, then cut into the embryo body of the desired shape; place the embryo body on the part to be sealed, heat up in an electric furnace at a rate of 2°C / min, ...
Embodiment 2
[0043] Embodiment 2: Preparation and sealing of materials
[0044] according to Figure 8 The ratio of each component, weigh a certain amount of analytically pure raw materials (CaO, SrO, SiO 2 、Al 2 o 3 、B 2 o 3 , Ga 2 o 3 ), and mixed evenly with a planetary ball mill for 24 hours; then put the powder into a platinum crucible, place it in the air atmosphere of a box-type resistance furnace, heat it at 3°C / min to 1450°C, and keep it warm for 1 hour; then, take out the crucible, Pour the melt into deionized water for rapid cooling, and dry to obtain fragments of glass melt; grind and pass through a 100-mesh sieve to obtain glass powder. Mix glass powder with methylcellulose, polyvinyl alcohol, n-butanol and acetone (82%, 2%, 2%, 8%, 6% by weight) to form a slurry, and disperse evenly in a ball mill; Stretching, drying naturally, and then cutting the embryo body into the desired shape; placing the embryo body on the part to be sealed, raising the temperature in an elect...
PUM
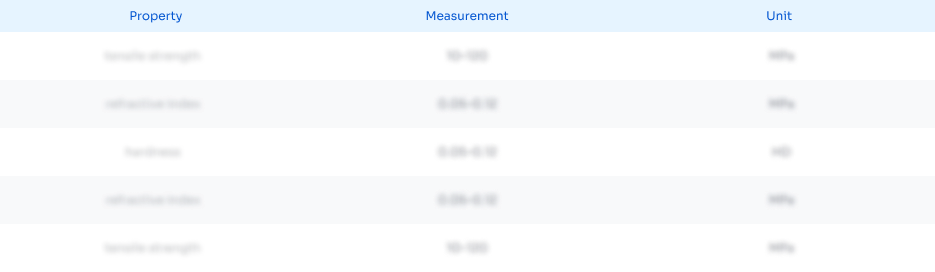
Abstract
Description
Claims
Application Information

- R&D
- Intellectual Property
- Life Sciences
- Materials
- Tech Scout
- Unparalleled Data Quality
- Higher Quality Content
- 60% Fewer Hallucinations
Browse by: Latest US Patents, China's latest patents, Technical Efficacy Thesaurus, Application Domain, Technology Topic, Popular Technical Reports.
© 2025 PatSnap. All rights reserved.Legal|Privacy policy|Modern Slavery Act Transparency Statement|Sitemap|About US| Contact US: help@patsnap.com