Manufacturing method of laminated type ceramic electronic element
A technology of electronic components and manufacturing methods, applied in the direction of inductor/transformer/magnet manufacturing, resistance manufacturing, electrical components, etc., can solve the problems of increasing stray capacitance, deteriorating product performance, short-circuiting through holes, etc. The effect of capacitors
- Summary
- Abstract
- Description
- Claims
- Application Information
AI Technical Summary
Problems solved by technology
Method used
Image
Examples
Embodiment Construction
[0037] The present invention will be described below in combination with specific embodiments and with reference to the accompanying drawings.
[0038] a kind of like Figure 4~7 In the manufacturing method of the laminated chip ceramic electronic component shown, the laminated chip ceramic electronic component is a high-frequency magnetic bead with a length of 1.0mm and a width of 0.5mm imitating a bluetooth antenna structure. The overall molding stage has the following steps:
[0039] 1) Tape casting to form ceramic green sheets
[0040] 1.1) Surface coating
[0041] The ceramic slurry is coated on the surface of the PET film carrier sheet 10 to form a ceramic green sheet 11. The components of the coated ceramic slurry and their weight percentages are as follows:
[0042] Ferrite NiCuZn powder 80%;
[0043] Binder: polyvinyl butyral (PVB) resin 15%;
[0044] Dispersant: BYK110 3%;
[0045] Plasticizer: Dibutyl Phthalate (DBP) 2%.
[0047] ...
PUM
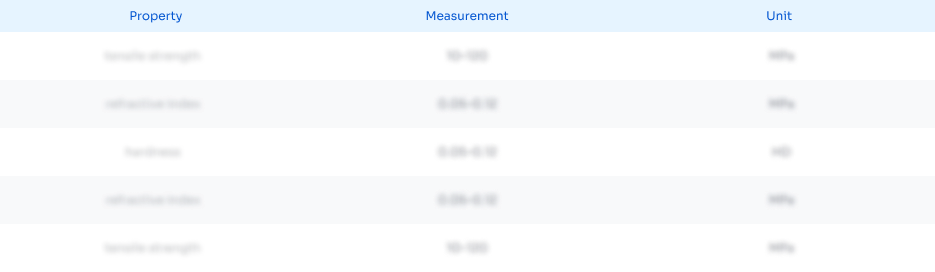
Abstract
Description
Claims
Application Information

- R&D
- Intellectual Property
- Life Sciences
- Materials
- Tech Scout
- Unparalleled Data Quality
- Higher Quality Content
- 60% Fewer Hallucinations
Browse by: Latest US Patents, China's latest patents, Technical Efficacy Thesaurus, Application Domain, Technology Topic, Popular Technical Reports.
© 2025 PatSnap. All rights reserved.Legal|Privacy policy|Modern Slavery Act Transparency Statement|Sitemap|About US| Contact US: help@patsnap.com