Method for preparing metal polysilicate flocculant
A polysilicate metal salt and flocculant technology, applied in the field of water treatment, can solve the problems of high cost, achieve good stability, good flocculation effect, and wide application range
- Summary
- Abstract
- Description
- Claims
- Application Information
AI Technical Summary
Problems solved by technology
Method used
Examples
Embodiment 1
[0013] Prepare polysilicate metal salt flocculant, concrete steps are:
[0014] 1) 20 grams of vitriol (FeSO 4 ·7H 2 (2), 40 grams of titanium dioxide waste acid, and 40 grams of industrial potassium chlorate join in the reaction vessel, stirred and reacted at 35 DEG C for 3 hours to obtain viscous polyferric sulfate;
[0015] 2) take by weighing 203 grams of sodium silicate (Na 2 SiO 3 , containing 100 g SiO 2 ) is diluted with water to form SiO 2 An aqueous solution of sodium silicate with a weight content of 2%, the pH value of the solution is adjusted to 3.5 with waste acid, stirring and polymerizing at room temperature for 10 minutes to obtain a polysilicate solution;
[0016] 3) Take 100 grams of the above-mentioned polyferric sulfate and add it to the polysilicate solution, stir evenly, and then activate it for 10 hours to obtain the polysilicate metal salt flocculant.
Embodiment 2
[0018] Prepare polysilicate metal salt flocculant, concrete steps are:
[0019] 1) 50 grams of vitriol (FeSO 4 ·7H 2 (2), 100 grams of titanium dioxide waste acid, and 50 grams of industrial potassium chlorate join in the reaction vessel, stirred and reacted at 50 DEG C for 2 hours to obtain viscous polyferric sulfate;
[0020] 2) take by weighing 203 grams of sodium silicate (Na 2 SiO 3 , containing 100 g SiO 2 ) is diluted with water to form SiO 2 A sodium silicate aqueous solution with a weight content of 3%, the pH value of the solution is adjusted to 4.5 with waste acid, stirring and polymerizing at room temperature for 30 minutes to obtain a polysilicate solution;
[0021] 3) Take 200 grams of the above-mentioned polyferric sulfate and add it into the polysilicate solution, stir evenly, and then activate it for 24 hours to obtain the polysilicate metal salt flocculant.
Embodiment 3
[0023] Prepare polysilicate metal salt flocculant, concrete steps are:
[0024] 1) 45 grams of vitriol (FeSO 4 ·7H 2 (2), 90 grams of titanium dioxide waste acid, and 60 grams of industrial potassium chlorate join in the reaction vessel, stirred and reacted at 45 DEG C for 2.5 hours to obtain viscous polyferric sulfate;
[0025] 2) take by weighing 473 grams of sodium silicate (Na 2 SiO 3 9H 2 O, containing 100 grams of SiO 2 ) is diluted with water to form SiO 2 A sodium silicate aqueous solution with a weight content of 2.5%, the pH value of the solution is adjusted to 4 with waste acid, stirring and polymerizing at room temperature for 20 minutes to obtain a polysilicate solution;
[0026] 3) Weigh 150 grams of the above-mentioned polyferric sulfate and add it into the polysilicate solution, stir evenly and then activate it at rest for 18 hours to obtain the polysilicate metal salt flocculant.
PUM
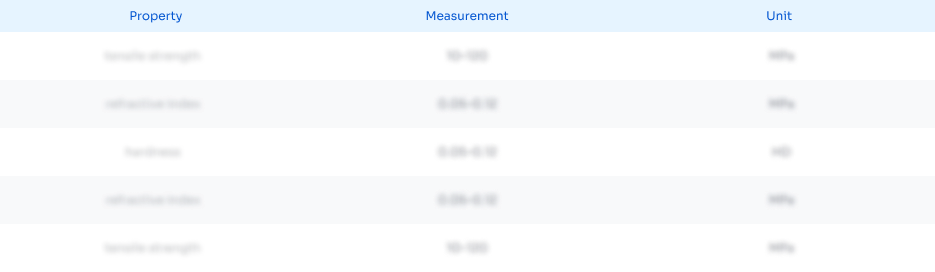
Abstract
Description
Claims
Application Information

- R&D Engineer
- R&D Manager
- IP Professional
- Industry Leading Data Capabilities
- Powerful AI technology
- Patent DNA Extraction
Browse by: Latest US Patents, China's latest patents, Technical Efficacy Thesaurus, Application Domain, Technology Topic, Popular Technical Reports.
© 2024 PatSnap. All rights reserved.Legal|Privacy policy|Modern Slavery Act Transparency Statement|Sitemap|About US| Contact US: help@patsnap.com