Glass fiber reinforced cement (GRC) insulation decorative wallboard and production method thereof
A technology of glass fiber and reinforced cement, which is applied to building components, ceramic molding machines, buildings, etc., can solve the problems of being unable to meet the needs of diversified architectural decoration, increasing the load of the frame structure due to its own weight, and affecting the safety of use due to low strength, and achieves the goal of decoration. Various effects, reduced on-site operation time, and outstanding thermal insulation performance
- Summary
- Abstract
- Description
- Claims
- Application Information
AI Technical Summary
Problems solved by technology
Method used
Image
Examples
Embodiment 1
[0056](1) Mix 50kg (50%) of cement, 15kg (15%) of sand, 3kg (3%) of glass shavings, 2kg (2%) of metal shavings, and 5kg (5%) of polyacrylate emulsion according to the distribution ratio by weight. Stir with water 25kg (25%) and make a slurry for subsequent use;
[0057] (2) The above-mentioned configured decorative layer slurry is sprayed to make a decorative layer in a mold and cured naturally for 20 minutes;
[0058] (3) Mix 25kg (25%) of cement, 60kg (60%) of sand, 7kg (7%) of alkali-resistant glass fiber, 1kg (1%) of polyacrylate emulsion, and 0.3 kg (0.3%), early strength agent triethanolamine 0.1kg (0.1%), antifreeze agent sodium nitrite 0.1kg (0.1%) and water 6.5kg (6.5%) stir and make glass fiber reinforced cement slurry for subsequent use;
[0059] (4) Spray the above-mentioned configured glass fiber reinforced cement slurry into the mold for making the decorative layer, and then use a pressure roller to carry out rolling compaction;
[0060] (5) Put the prepared in...
Embodiment 2
[0068] (1) 25kg (25%) of cement, 30kg (30%) of sand, 25kg (25%) of fine stones, 5kg (5%) of mica fragments, 4.1kg (4.1%) of polyacrylate emulsion, 1kg (1%) of polypropylene fiber, 1kg (1%) of liquid pigment, 0.4kg (0.4%) of water reducing agent naphthalene sulfonate formaldehyde condensate, 2kg (2%) of antifreeze calcium chloride and 6.5kg (6.5%) of water %), stir evenly to make slurry for subsequent use;
[0069] (2) The above-mentioned configured decorative layer slurry is used to lay and vibrate to make a decorative layer in a mold, and it is cured naturally for 30 minutes;
[0070] (3) According to the percentage distribution ratio by weight, cement 50kg (50%), sand 20kg (20%), alkali-resistant glass fiber 4kg (4%), early strength agent nitrite 0.4kg (0.4%), antifreeze agent potassium carbonate 0.6kg (0.6%), and water 25kg (20%) are stirred to make glass fiber reinforced cement slurry for subsequent use;
[0071] (4) pour the above-mentioned configured glass fiber reinfo...
Embodiment 3
[0080] (1) According to the percentage distribution ratio by weight, 37kg (37%) of cement, 33kg (33%) of sand, 2kg (2%) of shell debris, 10kg (10%) of polyacrylate emulsion, and 1kg (1kg) of early strength agent sulfate %), antifreeze agent calcium chloride 2kg (2%) and water 15kg (15%), stir and make slurry for subsequent use;
[0081] (2) Make the decorative layer slurry in the mould, by brushing the prepared decorative layer slurry, and let it solidify naturally for 60 minutes;
[0082] (3) Mix 41kg (41%) of cement, 41kg (41%) of sand, 3kg (3%) of alkali-resistant glass fiber (3%) and 15kg (15%) of water according to the distribution ratio by weight to make glass fiber reinforced cement slurry spare;
[0083] (4) pour the above-mentioned configured glass fiber reinforced cement slurry into the mold for making the decorative layer, and then use a pressure roller to carry out rolling compaction;
[0084] (5) Put the prepared installation connectors, suspension rings and ste...
PUM
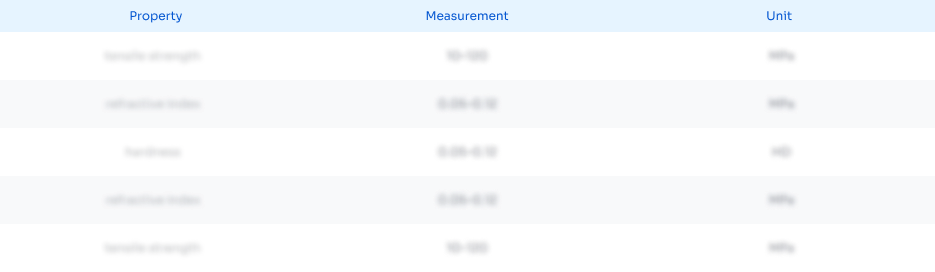
Abstract
Description
Claims
Application Information

- R&D
- Intellectual Property
- Life Sciences
- Materials
- Tech Scout
- Unparalleled Data Quality
- Higher Quality Content
- 60% Fewer Hallucinations
Browse by: Latest US Patents, China's latest patents, Technical Efficacy Thesaurus, Application Domain, Technology Topic, Popular Technical Reports.
© 2025 PatSnap. All rights reserved.Legal|Privacy policy|Modern Slavery Act Transparency Statement|Sitemap|About US| Contact US: help@patsnap.com