Method for preparing short-chain branch water and oil repellent finishing agent containing modified nano-oxide and fluorine
A nano-oxide and finishing agent technology, applied in fiber treatment, textiles and papermaking, etc., can solve the problems of high bioaccumulation and toxicity, low surface energy, unfavorable environment, etc., and achieve excellent water and oil repellency, enhanced repellency Water and oil repellency, high safety effect
- Summary
- Abstract
- Description
- Claims
- Application Information
AI Technical Summary
Problems solved by technology
Method used
Image
Examples
example 1
[0019] Take 13.20g of hexafluorobutyl methacrylate, 2.68g of methyl methacrylate, 3.36g of n-butyl acrylate, 1.08g of ureidomethacrylate, 1.28g of hexadecyltrimethylammonium bromide, and 1.28g of perfluorinated Put 0.64g of alkyl alcohol polyoxyethylene ether and 50g of deionized water in a beaker, emulsify with a high-speed emulsifier, and set aside; weigh 0.192g of ammonium persulfate and dissolve it in 10g of deionized water, set aside; 3.30g of fluorobutyl ester, 0.67g of methyl methacrylate, 0.84g of n-butyl acrylate, 0.27g of ureidomethacrylate, 0.048g of ammonium persulfate, 0.32g of cetyltrimethylammonium bromide, Put 0.16g of fluoroalkyl alcohol polyoxyethylene ether, 1.2g of modified titanium dioxide and 60g of deionized water in a beaker, use an ultrasonic pulverizer to ultrasonically disperse for 10 minutes, and then emulsify with a high-speed emulsifier and add a mixer, thermometer, In the reaction vessel of the condenser, after feeding nitrogen and raising the te...
example 2
[0024] Take 20.8 g of trifluoroethyl methacrylate, 4.6 g of styrene, 5.32 g of butyl methacrylate, 2.04 g of methylol acrylamide, 1.04 g of hydroxyethyl methacrylate, and 3.2 g of sodium dodecylbenzenesulfonate g, 3.08g of perfluoroalkyl ethoxy ether alcohol and 72.8g of deionized water are placed in a beaker, emulsified using a high-speed emulsifier, and set aside; weigh 0.212g of azobisisobutylamidine hydrochloride and dissolve it in 10g of deionized water In deionized water, set aside; Separately weigh 5.20 g of trifluoroethyl methacrylate, 1.15 g of styrene, 1.33 g of butyl methacrylate, 0.51 g of methylol acrylamide, 0.26 g of hydroxyethyl methacrylate, azo Diisobutylamidine hydrochloride 0.053g, sodium dodecylbenzene sulfonate 0.8g, perfluoroalkyl ethoxy ether alcohol 0.77g, modified silicon dioxide 1.5g and 67.2g deionized water in a beaker ,Use an ultrasonic pulverizer to ultrasonically disperse for 20 minutes, then emulsify with a high-speed emulsifier and add it to a...
example 3
[0027] Take 13.64g of hexafluorobutyl acrylate, 4.8g of lauryl acrylate, 1.6g of acrylic acid, 1.28g of hydroxypropyl methacrylate, 0.72g of glycidyl acrylate, 0.76g of octadecyltrimethylammonium bromide, fat Alcohol polyoxyethylene ether OS-150.44g and deionized water 55g were placed in a beaker, emulsified with a high-speed emulsifier, and set aside; weighed 0.128g of azodiisopropylimidazoline hydrochloride and dissolved in 10g of deionized water, set aside In addition, 3.41g of hexafluorobutyl acrylate, 1.2g of lauryl acrylate, 0.4g of acrylic acid, 0.32g of hydroxypropyl methacrylate, 0.18g of glycidyl acrylate, and azodiisopropylimidazoline hydrochloride Put 0.032g, 0.19g of octadecyltrimethylammonium bromide, fatty alcohol polyoxyethylene ether OS-150.11g, 1.5g of modified magnesium oxide and 55g of deionized water in a beaker, and use an ultrasonic pulverizer to ultrasonically disperse for 15 minutes , and then emulsified with a high-speed emulsifier and added to a reac...
PUM
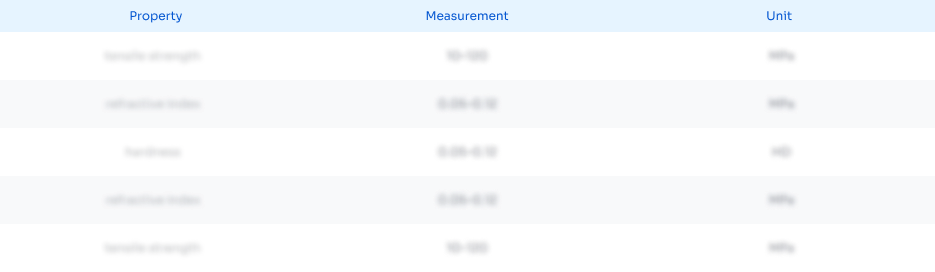
Abstract
Description
Claims
Application Information

- R&D
- Intellectual Property
- Life Sciences
- Materials
- Tech Scout
- Unparalleled Data Quality
- Higher Quality Content
- 60% Fewer Hallucinations
Browse by: Latest US Patents, China's latest patents, Technical Efficacy Thesaurus, Application Domain, Technology Topic, Popular Technical Reports.
© 2025 PatSnap. All rights reserved.Legal|Privacy policy|Modern Slavery Act Transparency Statement|Sitemap|About US| Contact US: help@patsnap.com