LF (Ladle Furnace) hot steel slag recycling process
A hot-state steel slag and process technology, which is applied in the field of steel-making and refining in the metallurgical industry, can solve the problems of environmental pollution, waste of heat and waste of hot-state refining slag, save the amount of deoxidizer added, improve the yield of molten steel, reduce The effect of production costs
- Summary
- Abstract
- Description
- Claims
- Application Information
AI Technical Summary
Problems solved by technology
Method used
Image
Examples
Embodiment 1
[0022] In this embodiment, in the tundish casting furnace, after the first ladle of molten steel is cast, its sulfur content is detected to be 0.020, and the ladle is hoisted from the rotary table of the continuous casting machine with the workshop crane, and the small hook on the crane Hang the connecting piece at the bottom of the ladle, lift the small hook of the crane to overturn the ladle, and pour all the remaining steel slag and poured molten steel into another ladle after the steel is tapped from the converter. The ladle slag stays for 8 minutes after being suspended from the continuous casting, which avoids sticking to the bottom of the ladle. The smelting cycle is controlled at 24 minutes.
[0023] Refining is carried out after adding refining raw materials into the ladle. During the refining process, it is necessary to ensure that argon is blown throughout. In the stage of power supply, the pressure of argon is 0.4 MPa, and the flow rate of argon is 30 liters / min; (...
Embodiment 2
[0026] In this embodiment, in the tundish casting furnace, after the first ladle of molten steel is cast, its sulfur content is detected to be 0.025. The workshop crane is used to hang the ladle from the rotary table of the continuous casting machine. The small hook on the crane Hang the connecting piece at the bottom of the ladle, lift the small hook of the crane to overturn the ladle, and pour all the remaining steel slag and poured molten steel into another ladle after the steel is tapped from the converter. The ladle slag stays for 9 minutes after being suspended from the continuous casting, which avoids sticking to the bottom of the ladle. The smelting cycle is controlled at 25 minutes.
[0027] Refining is carried out after adding refining raw materials into the ladle. During the refining process, it is necessary to ensure that argon is blown throughout. In the stage of power supply, the pressure of argon gas is 0.4 MPa, and the flow rate of argon gas is 40 liters / min; ...
Embodiment 3
[0030] In this embodiment, in the tundish casting furnace, after the first ladle of molten steel is cast, its sulfur content is detected to be 0.045, and the ladle is hoisted from the rotary table of the continuous casting machine with the workshop crane, and the small hook on the crane Hang the connecting piece at the bottom of the ladle, lift the small hook of the crane to overturn the ladle, and pour all the remaining steel slag and poured molten steel into another ladle after the steel is tapped from the converter. The ladle slag stays for 9.5 minutes after being lifted from the continuous casting, which avoids sticking to the bottom of the ladle. The smelting cycle is controlled at 23 minutes.
[0031] Refining is carried out after adding refining raw materials into the ladle. During the refining process, it is necessary to ensure that argon gas is blown throughout. In the stage of power supply, the pressure of argon gas is 0.4 MPa, and the flow rate of argon gas is 47 li...
PUM
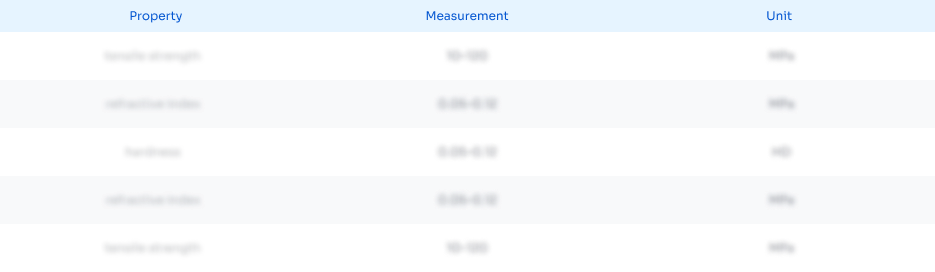
Abstract
Description
Claims
Application Information

- R&D
- Intellectual Property
- Life Sciences
- Materials
- Tech Scout
- Unparalleled Data Quality
- Higher Quality Content
- 60% Fewer Hallucinations
Browse by: Latest US Patents, China's latest patents, Technical Efficacy Thesaurus, Application Domain, Technology Topic, Popular Technical Reports.
© 2025 PatSnap. All rights reserved.Legal|Privacy policy|Modern Slavery Act Transparency Statement|Sitemap|About US| Contact US: help@patsnap.com