Preparation method of alkyl blocked allyl polyether
A technology of allyl-terminated polyether and alkyl polyether, which is applied in the field of preparation of alkyl-terminated allyl polyether, can solve the problems of troublesome post-processing, many side reactions, and increased side reactions, and achieve post-processing Convenient and simple, simplified reaction conditions, mild reaction conditions
- Summary
- Abstract
- Description
- Claims
- Application Information
AI Technical Summary
Problems solved by technology
Method used
Image
Examples
Embodiment 1
[0037] In a four-necked flask equipped with a stirring device, a reflux condenser, a thermometer and a dropping funnel, add R to C 12 Fatty alcohol polyoxyethylene ether (I) (number of oxyethylene n=7) 247g, NaOH 21g, stirred and heated to 40°C, within 1.5 hours, 57g of allyl chloride was added dropwise, and then reacted at 100°C for 5 hours, After the reaction is completed, use 2g of glacial acetic acid to neutralize to neutral, distill under reduced pressure at 100-110°C for 1.5 hours, remove low boilers until the allyl chloride is basically removed, filter and separate the organic matter and the generated salt to obtain the target compound 240g, the yield is 90%, light yellow transparent liquid.
[0038] Spectral analysis of target compounds:
[0039] IR (KBr cm -1 ): 2917(C-H), 1645(C=C), through the division of characteristic absorption peaks, it is proved that the product structure contains carbon-carbon unsaturated double bond C=C, which shows that the main product ob...
Embodiment 2
[0042] In a four-necked flask equipped with a stirring device, a reflux condenser, a thermometer and a dropping funnel, add R to C 12 Isomerized alkyl alcohol polyoxyethylene ether (I) (oxyethylene number n=9) 188g, KOH 18g, stirred and heated to about 30°C, within 0.5 hours, 25g of allyl chloride was added dropwise, and then at 70°C React under low temperature for 6 hours. After the reaction is completed, use 10g of 35% hydrochloric acid solution to neutralize to neutrality. Distill under reduced pressure at 100-110°C for 1 hour, remove low boiling matter until allyl chloride is basically removed, and filter to separate organic matter. and the generated salt to obtain 165 g of the target compound, with a yield of 83%, and a yellow transparent liquid.
[0043] Spectral analysis of target compounds:
[0044] IR (KBr cm -1 ): 2924(C-H), 1647(C=C), through the division of characteristic absorption peaks, it is proved that the product structure contains carbon-carbon unsaturated...
Embodiment 3
[0047] In a three-neck flask equipped with a stirring device, a reflux condenser, a thermometer and a dropping funnel, add R to C 18Fatty alcohol polyoxyethylene ether (I) (oxyethylene number n=3) 502g, NaOH 60g, stirred and heated up to 50°C, within 3.0 hours, 143g of allyl chloride was added dropwise, and then reacted at 90°C for 3.5 hours, After the reaction is completed, use 7.5g of glacial acetic acid to neutralize to neutral, distill under reduced pressure at 100-110°C for 1.5 hours, remove low boilers until allyl chloride is basically removed, filter and separate organic matter and generated salts to obtain the target Compound 463g, yield 93%, light yellow transparent liquid.
[0048] Spectral analysis of target compounds:
[0049] IR (KBr cm -1 ): 2923(C-H), 1647(C=C), through the division of characteristic absorption peaks, it is proved that the product structure contains carbon-carbon unsaturated double bond C=C, which shows that the main product obtained is exactl...
PUM
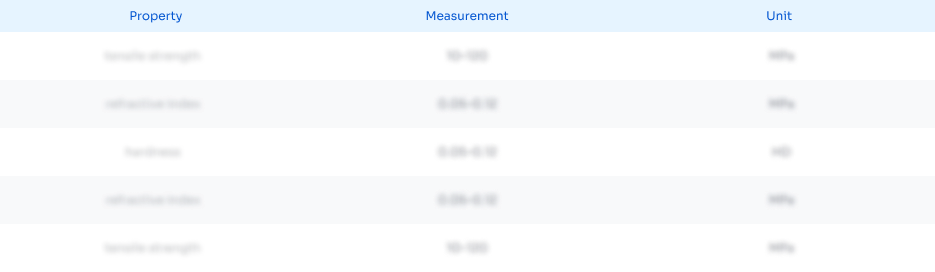
Abstract
Description
Claims
Application Information

- Generate Ideas
- Intellectual Property
- Life Sciences
- Materials
- Tech Scout
- Unparalleled Data Quality
- Higher Quality Content
- 60% Fewer Hallucinations
Browse by: Latest US Patents, China's latest patents, Technical Efficacy Thesaurus, Application Domain, Technology Topic, Popular Technical Reports.
© 2025 PatSnap. All rights reserved.Legal|Privacy policy|Modern Slavery Act Transparency Statement|Sitemap|About US| Contact US: help@patsnap.com