Method for synthesizing 2,6-dimethylnaphthalene with 2-methylnaphthalene and C10 aromatics by transferring alkyl group
A technology of carbon ten aromatic hydrocarbon alkyl and dimethyl naphthalene, which is applied in the field of synthesizing 2,6-dimethylnaphthalene by transalkylation of 2-methylnaphthalene and carbon ten aromatic hydrocarbon, and can solve the problems of reduced selectivity, large material consumption, and side effects. Serious reaction and other problems, to achieve the effects of slow deactivation, lower production costs, and long service life
- Summary
- Abstract
- Description
- Claims
- Application Information
AI Technical Summary
Problems solved by technology
Method used
Image
Examples
Embodiment 1
[0017] Embodiment 1: first put appropriate amount of glass beads at the bottom of the reaction tube bed layer of the miniature fixed-bed catalytic reactor with an internal diameter of 1.5 cm, spread a thin layer of quartz wool on the glass beads, and then put 3.0 to 5.0 g of cylindrical silica-alumina The MCM-22 molecular sieve catalyst with a ratio of 20 is loaded into the reaction tube, and the upper layer is filled with an appropriate amount of glass beads, and then the carrier gas hydrogen is introduced. The carrier gas / reactant ratio is 2:1 (mol / mol) to ensure that the gas flow flows through the catalyst evenly. Bed layer; reaction pressure is 3.0MPa, through 100 minutes program warming up to setting temperature, feeds with metering pump and is composed of a (carbon ten aromatics): b (2-methylnaphthalene)=4.5: 1 (kg / kg) Reaction raw material, mass space velocity WHSV=0.5h -1 , from low temperature to high temperature to investigate the effect of catalytic reaction at diff...
Embodiment 2
[0018] Embodiment 2: The difference between this embodiment and Example 1 is that the SAPO-11 molecular sieve with a Si: Al: P molar ratio of 0.03: 0.25: 0.22 is used as a catalyst, and the carrier gas hydrogen is introduced, and the carrier gas / reactant ratio is 7:1 (mol / mol); see Table 1 for other specific reaction conditions.
Embodiment 3
[0019] Example 3: The difference between this example and Example 1 is that the ZSM-5 molecular sieve with a silicon-aluminum ratio of 38 is used as a catalyst, and the carrier gas nitrogen is introduced, and the carrier gas / reactant ratio is 1.5:1 (mol / mol) ; See Table 1 for other specific reaction conditions.
PUM
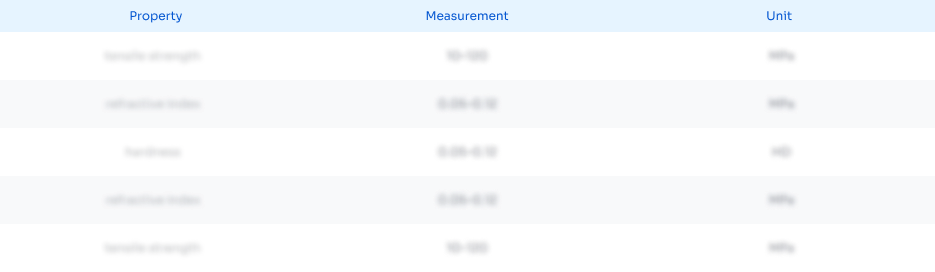
Abstract
Description
Claims
Application Information

- R&D
- Intellectual Property
- Life Sciences
- Materials
- Tech Scout
- Unparalleled Data Quality
- Higher Quality Content
- 60% Fewer Hallucinations
Browse by: Latest US Patents, China's latest patents, Technical Efficacy Thesaurus, Application Domain, Technology Topic, Popular Technical Reports.
© 2025 PatSnap. All rights reserved.Legal|Privacy policy|Modern Slavery Act Transparency Statement|Sitemap|About US| Contact US: help@patsnap.com