Pretreatment method for recovering valuable metal from anode material of waste lithium ion battery
A technology for lithium-ion batteries and positive electrode materials, which is applied in the field of efficient recovery and pretreatment of valuable metals in waste lithium-ion battery positive electrode materials, can solve the problems of complicated separation and recovery, difficult separation, high price, etc. Effects of cost reduction and temperature reduction
- Summary
- Abstract
- Description
- Claims
- Application Information
AI Technical Summary
Problems solved by technology
Method used
Image
Examples
Embodiment 1
[0031] Take a piece of used Nokia BL-5B lithium battery manufactured by Sanyo Energy Beijing Co., Ltd., soak it in saturated salt water for 6 hours, until it is fully discharged, disassemble it in a ventilated environment, decompose to obtain 5.32g of positive electrode material, and place it in a vacuum furnace . Heating at a heating rate of 10°C / min to 540-550°C, with a vacuum degree of 80-100Pa, keeping it warm for 0.5h, taking it out after cooling, separating the obtained lithium cobaltate powder and aluminum foil, and grinding the lithium cobaltate powder, the obtained powder is Liquid-solid ratio of 40-50g / L placed at 70-80°C containing 3mol / LH 2 SO 4 With 15~20vol.% H 2 o 2 Leach for 1 hour. During the reaction, soak the separated aluminum foil in the mixed solution for 1 minute, remove it and rinse it with a small amount of water. After the reaction, measure the metal content of the leaching solution by ICP atomic emission spectrometry: cobalt 10.580g / L, lithium 1.1...
Embodiment 2
[0033] Take a piece of used SAMSUNG3.7V lithium battery manufactured by Tianji Samsung Communication Technology Co., Ltd., soak it in saturated salt water for 6 hours, until it is fully discharged, disassemble it in a ventilated environment, and decompose it to obtain 6.41g of positive electrode material, which is placed in a vacuum furnace. Heating at a heating rate of 10°C / min to 540-550°C, with a vacuum degree of 60-80Pa, keeping it warm for 0.5h, taking it out after cooling, separating the obtained lithium cobaltate powder and aluminum foil, grinding the lithium cobaltate powder, and the obtained powder is Liquid-solid ratio of 40-50g / L placed at 70-80°C containing 3mol / LH 2 SO 4 With 15~20vol.% H 2 o 2 Leach for 1 hour. During the reaction, soak the separated aluminum foil in the mixed solution for 1.5 minutes, remove it and rinse it with a small amount of water. After the reaction, measure the metal content of the leach solution by ICP atomic emission spectrometry: cob...
Embodiment 3
[0035]Take a used SAMSUNG 3.7V lithium-ion battery manufactured in Japan and assembled in South Korea, soak it in saturated salt water for 6 hours, until it is fully discharged, disassemble it in a ventilated environment, decompose to obtain 6.78g of positive electrode material, and place it in a vacuum furnace. Heat at a heating rate of 10°C / min to 540-550°C, vacuum degree 40-60Pa, keep warm for 0.5h, take it out after cooling, separate the obtained lithium cobalt oxide powder and aluminum foil, grind the lithium cobalt oxide powder, and obtain the powder With a liquid-solid ratio of 40-50g / L placed at 70-80°C containing 2.5-3mol / LH 2 SO 4 With 15~20vol.% H 2 o 2 Leach for 1 hour. During the reaction, soak the separated aluminum foil in the mixed solution for 2 minutes, remove it and rinse it with a small amount of water. After the reaction, measure the metal content of the leaching solution by ICP atomic emission spectrometry: cobalt 18.910g / L, lithium 2.021g / L, aluminum ...
PUM
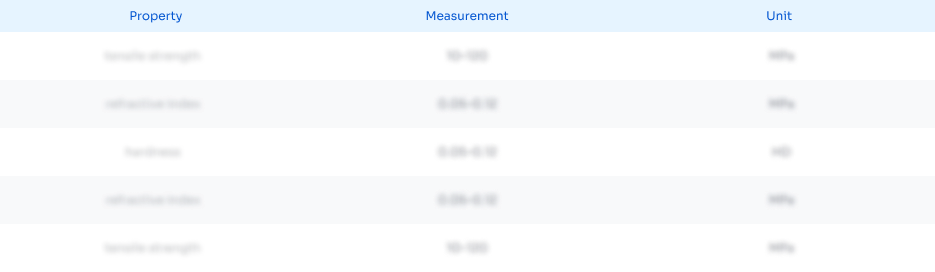
Abstract
Description
Claims
Application Information

- R&D Engineer
- R&D Manager
- IP Professional
- Industry Leading Data Capabilities
- Powerful AI technology
- Patent DNA Extraction
Browse by: Latest US Patents, China's latest patents, Technical Efficacy Thesaurus, Application Domain, Technology Topic, Popular Technical Reports.
© 2024 PatSnap. All rights reserved.Legal|Privacy policy|Modern Slavery Act Transparency Statement|Sitemap|About US| Contact US: help@patsnap.com