High-silicon extra-low-carbon stainless steel soldering wire and horizontal continuous-casting tandem-rolling continuous-drawing manufacturing method thereof
A horizontal continuous casting, ultra-low carbon technology, applied in the direction of manufacturing tools, welding equipment, welding media, etc.
- Summary
- Abstract
- Description
- Claims
- Application Information
AI Technical Summary
Problems solved by technology
Method used
Image
Examples
Embodiment 1
[0049] Embodiment 1 In conjunction with accompanying drawing, the manufacturing method of high-silicon ultra-low carbon stainless steel welding wire of the present invention, the steps are as follows:
[0050] (1) According to the designed welding wire composition and batching, the molten steel is smelted in a vacuum electric furnace to desulfurize, dephosphorize and remove harmful impurities, so that C<0.3%, and the tapping temperature T≥1680°C.
[0051] The chemical composition of the designed welding wire is shown in Table 3.
[0052] table 3
[0053]
[0054] (2) Use AOD at 1680°C for out-of-furnace refining, purify molten steel, use vacuum oxygen blowing technology to decarburize, reach C<0.01%, and perform tundish casting at 1590°C.
[0055] (3) The horizontal continuous casting technology is adopted to further refine the molten steel in the tundish, and the electromagnetically driven centrifugal flow tundish is used to purify the molten steel, eliminate pores, and ...
Embodiment 2
[0061] Embodiment 2 In conjunction with accompanying drawing, the manufacturing method of high-silicon ultra-low carbon stainless steel welding wire of the present invention, the steps are as follows:
[0062] (1) According to the designed welding wire composition and batching, the molten steel is smelted in a vacuum electric furnace to desulfurize, dephosphorize and remove harmful impurities, so that C<0.3%, and the tapping temperature T≥1680°C.
[0063] The chemical composition of the designed welding wire is shown in Table 5.
[0064] table 5
[0065]
[0066] (2) Use AOD at 1700°C for out-of-furnace refining, purify molten steel, use vacuum oxygen blowing technology to decarburize, reach C<0.01%, and perform tundish casting at 1600°C.
[0067] (3) The horizontal continuous casting technology is adopted to further refine the molten steel in the tundish, and the electromagnetically driven centrifugal flow tundish is used to purify the molten steel, eliminate pores, and ...
Embodiment 3
[0073] Embodiment 3 In conjunction with accompanying drawing, the manufacturing method of high-silicon ultra-low carbon stainless steel welding wire of the present invention, the steps are as follows:
[0074] (1) According to the designed welding wire composition and batching, the molten steel is smelted in a vacuum electric furnace to desulfurize, dephosphorize and remove harmful impurities, so that C<0.3%, and the tapping temperature T≥1680°C.
[0075] The chemical composition of the designed welding wire is shown in Table 7.
[0076] Table 7
[0077]
[0078] (2) Use AOD at 1690°C for out-of-furnace refining, purify molten steel, use vacuum oxygen blowing technology to decarburize, achieve C<0.01%, and perform tundish casting at 1595°C.
[0079] (3) The horizontal continuous casting technology is adopted to further refine the molten steel in the tundish, and the electromagnetically driven centrifugal flow tundish is used to purify the molten steel, eliminate pores, and...
PUM
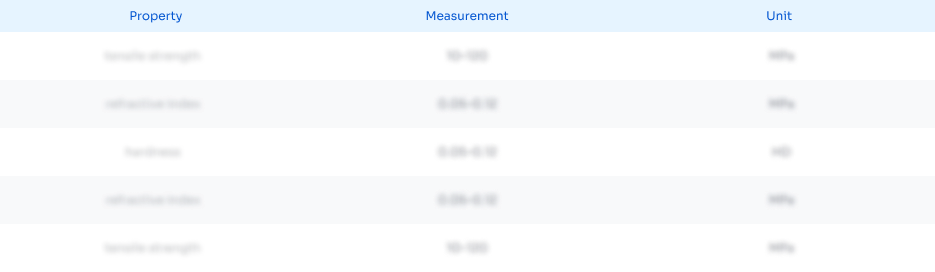
Abstract
Description
Claims
Application Information

- R&D Engineer
- R&D Manager
- IP Professional
- Industry Leading Data Capabilities
- Powerful AI technology
- Patent DNA Extraction
Browse by: Latest US Patents, China's latest patents, Technical Efficacy Thesaurus, Application Domain, Technology Topic, Popular Technical Reports.
© 2024 PatSnap. All rights reserved.Legal|Privacy policy|Modern Slavery Act Transparency Statement|Sitemap|About US| Contact US: help@patsnap.com