Method for preparing poly(arylene ether nitrile) resin powder
A polyarylether nitrile and resin powder technology, which is applied in the field of polyarylether nitrile resin powder and its preparation, can solve the problems of complex preparation process, insufficient purity, and reduced resin performance, and achieve excellent electrical properties, uniform particle size, and high performance stable effect
- Summary
- Abstract
- Description
- Claims
- Application Information
AI Technical Summary
Problems solved by technology
Method used
Image
Examples
Embodiment 1
[0025] Molar ratio: 2,6-dichlorobenzonitrile: hydroquinone: resorcinol: anhydrous potassium carbonate: N-methylpyrrolidone: toluene = 1:0.9:0.1:1.2:6:1.3 preparation Raw materials are put into a reaction kettle with water separator, agitator and heater, and the temperature is raised to 140°C for dehydration reaction for 2 hours under stirring. Toluene is evaporated through the water separator, and the temperature is raised to 200°C. When rod phenomenon occurs, a certain amount of N-methylpyrrolidone solvent is injected into the reactor to terminate the reaction, and at the same time, the reaction solution is diluted so that the mass concentration of the reaction product is 2-10%. Cool down the temperature in the reactor to 120-140°C and add ethanol to the reactor. The amount of ethanol added is 70-110% of the volume of N-methylpyrrolidone. The temperature in the reactor is controlled at 20-70°C. After continuous stirring for 1 hour, Centrifuge for solid-liquid separation, put ...
Embodiment 2
[0029] Molar ratio: 2,6-dichlorobenzonitrile: biphenol: anhydrous potassium carbonate: N-methylpyrrolidone: toluene = 1: 1: 1.3: 7: 1.4 Prepare the raw materials and put them into the belt In the reaction kettle with water tank, agitator and heater, heat and stir to 150°C for dehydration reaction for 2 hours, steam the toluene through the water separator, raise the temperature to 200°C, and inject it into the reaction kettle when the rod climbing phenomenon occurs. A certain amount of N-methylpyrrolidone solvent terminates the reaction, so that the mass concentration of the reaction product is 8-15%. Lower the temperature in the reactor to 120-140°C and add methanol to the reactor. The amount of methanol added is 50-80% of the volume of N-methylpyrrolidone. The temperature in the reactor is controlled at 20-100°C. After continuous stirring for 1 hour, the Centrifuge for solid-liquid separation, put the solid into oxalic acid or hydrochloric acid boiling aqueous solution with a...
Embodiment 3
[0033]Molar ratio: 2,6-dichlorobenzonitrile: bisphenol A: anhydrous potassium carbonate: N-methylpyrrolidone: toluene = 1: 1: 1.2: 6: 1.3 Prepare raw materials, and put into Heating and stirring to 140°C for dehydration reaction for 3 hours, steaming toluene through the water separator, raising the temperature to 200°C, and injecting a certain amount of A certain amount of N-methylpyrrolidone solvent terminates the reaction, so that the mass concentration of the reaction product is 10-15%. Cool down the temperature in the reaction kettle to 120-140°C and add water to the reaction kettle. The amount of water added is 130-200% of the volume of N-methylpyrrolidone. The temperature in the reaction kettle is controlled at 20-70°C. After continuous stirring for 1 hour, Centrifuge for solid-liquid separation, put the solid into oxalic acid or hydrochloric acid boiling aqueous solution with a pH value between (5,7), wash three times, filter, and then dry at 150°C for 8 hours to obtain...
PUM
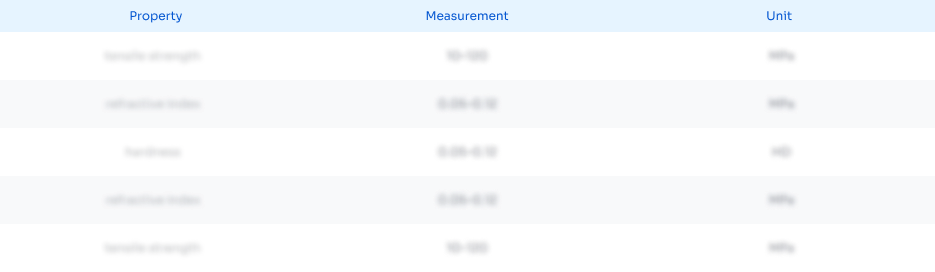
Abstract
Description
Claims
Application Information

- R&D Engineer
- R&D Manager
- IP Professional
- Industry Leading Data Capabilities
- Powerful AI technology
- Patent DNA Extraction
Browse by: Latest US Patents, China's latest patents, Technical Efficacy Thesaurus, Application Domain, Technology Topic, Popular Technical Reports.
© 2024 PatSnap. All rights reserved.Legal|Privacy policy|Modern Slavery Act Transparency Statement|Sitemap|About US| Contact US: help@patsnap.com