Method for extracting vanadium pentoxide from vanadium slag
The technology of vanadium pentoxide and vanadium slag is applied in the field of vanadium metallurgy, which can solve the problems of equipment investment and operation difficulties, high energy consumption and high equipment requirements, and achieve the effects of high leaching rate, low environmental pollution and low equipment requirements.
- Summary
- Abstract
- Description
- Claims
- Application Information
AI Technical Summary
Problems solved by technology
Method used
Image
Examples
Embodiment 1
[0028] Embodiment 1 adopts the inventive method to extract vanadium pentoxide from vanadium slag
[0029] The vanadium slag is crushed and ball milled, and the passing rate of passing through 200 mesh reaches 82%, and 100g of refined vanadium slag is weighed and roasted under aerobic conditions. The roasting temperature is 850°C, and the time is controlled at 3.0h;
[0030] Grind the clinker in a ball mill, then add 20% potassium hydroxide solution and 15% sodium carbonate solution for leaching, the liquid-solid ratio is 4:1, the leaching reaction temperature is 120°C, and the leaching reaction time is 1.0h. The clinker was washed 5 times; the feed liquid was subjected to solid-liquid separation at 90°C, and filtered to obtain 14g / L vanadium-containing solution and tailings;
[0031] Add 0.3 parts by mass of CaCl to the vanadium-containing solution 2 and 0.2 parts by mass of Al 2 (SO 4 ) 3 Carry out impurity removal, the time for impurity removal is 0.5h, and remove slag a...
Embodiment 2
[0034] Embodiment 2 adopts the inventive method to extract vanadium pentoxide from vanadium slag
[0035] The vanadium slag is crushed and ball milled, and the passing rate of passing through 200 meshes reaches 90%. Weigh 100g of refined vanadium slag and roast it under aerobic conditions. The roasting temperature is 1000°C, and the time is controlled at 1.0h;
[0036] Grind the clinker in a ball mill, then add 20% potassium carbonate solution and 30% sodium sulfate solution for leaching, the liquid-solid ratio is 2:1, the leaching reaction temperature is 150°C, and the leaching reaction time is 2.0h. The clinker was washed 4 times; the feed liquid was subjected to solid-liquid separation at 120°C, and filtered to obtain 27g / L vanadium-containing solution and tailings;
[0037] Add 0.1 mass parts of CaO and 0.4 mass parts of MgCl to the vanadium-containing solution 2 Carry out impurity removal, the impurity removal time is 1.0h, and remove slag after the reaction is completed...
Embodiment 3
[0040] Embodiment 3 adopts the inventive method to extract vanadium pentoxide from vanadium slag
[0041] The vanadium slag is crushed and ball milled, and the passing rate of passing through 200 meshes reaches 86%. Weigh 100g of refined vanadium slag and roast it under aerobic conditions. The roasting temperature is 900°C, and the time is controlled at 1.0h;
[0042] Grind the clinker in a ball mill, then add 30% sodium hydroxide solution and 15% sodium carbonate solution for leaching, the liquid-solid ratio is 3:1, the leaching reaction temperature is 130°C, and the leaching reaction time is 1.5h. The clinker was washed 3 times; the feed liquid was subjected to solid-liquid separation at 95°C, and filtered to obtain 21g / L vanadium-containing solution and tailings;
[0043] Add 0.5 parts by mass of CaCl to the vanadium-containing solution 2 Carry out impurity removal, the impurity removal time is 1.0h, and remove slag after the reaction is completed; the liquid phase is cool...
PUM
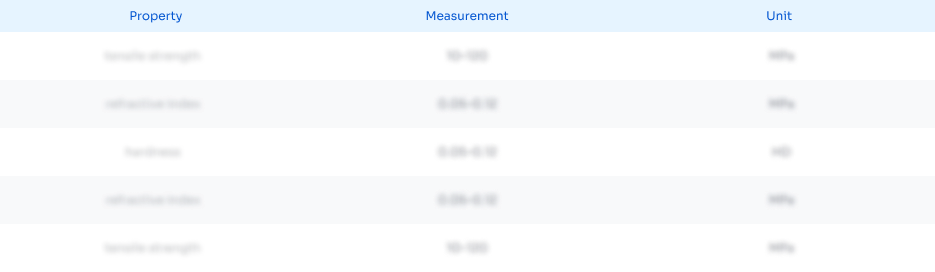
Abstract
Description
Claims
Application Information

- R&D Engineer
- R&D Manager
- IP Professional
- Industry Leading Data Capabilities
- Powerful AI technology
- Patent DNA Extraction
Browse by: Latest US Patents, China's latest patents, Technical Efficacy Thesaurus, Application Domain, Technology Topic, Popular Technical Reports.
© 2024 PatSnap. All rights reserved.Legal|Privacy policy|Modern Slavery Act Transparency Statement|Sitemap|About US| Contact US: help@patsnap.com