Preparation method of negative-ion master batch
A technology of negative ions and master batches, applied in the field of preparation of polymer additives, can solve the problems of reduced negative ion generation speed, increased processing difficulty, limited negative ion generation amount, etc., and achieves increased negative ion generation, good compatibility, and improved mechanical properties. Effect
- Summary
- Abstract
- Description
- Claims
- Application Information
AI Technical Summary
Problems solved by technology
Method used
Image
Examples
preparation example Construction
[0026] A preparation method of negative ion masterbatch, comprising:
[0027] 1) Put the negative ion additive and surface treatment agent into a high-speed mixer at a mass ratio of 100:3 to 10, stir or heat during stirring until the surface treatment agent melts;
[0028] 2) Put the stirred raw materials into a low-speed mixer, and stir while cooling until the raw materials are cooled to room temperature to obtain a cooling material;
[0029] 3) The cooling material is ball milled to obtain a modified negative ion additive (FL additive);
[0030] 4) Mixing 20-80 parts by mass of modified anion additive, 20-80 parts by mass of organic carrier, antioxidant and lubricant;
[0031] 5) extruding the raw material, cooling, cutting into pellets, and drying to obtain the negative ion masterbatch.
[0032] The schematic diagram of its preparation process is shown in figure 1 shown.
[0033] Surface treatment agents include stearic acid, stearates, polyethylene wax, and oxidized po...
Embodiment 1
[0044] 1) Take 100 parts of negative ion additives and 5 parts of stearic acid, put them into a high-speed mixer for stirring, and heat up to 75°C to melt the surface treatment agent;
[0045] 2) Blowing the material in the high-speed mixer into a low-speed mixer with a cooling device, and cooling to room temperature while stirring;
[0046] 3) The cooling material is ball milled to 400 mesh without sieve residue to obtain a modified negative ion additive;
[0047] 4) Take 80 parts of modified anion additives, 20 parts of organic carrier EVA, antioxidant 1010: 1 part, antioxidant 168: 1 part, lubricant PE wax: 2 parts and put them into the mixer, mix well;
[0048] 5) The uniformly mixed raw materials are kneaded and extruded through a high-shear twin-screw extruder with an aspect ratio of 40, air-cooled, and cut to obtain an anion masterbatch.
Embodiment 2
[0050] 1) Take 100 parts of negative ion additives and 6 parts of oxidized polyethylene wax, put them into a high-speed mixer for stirring, and heat up to 105°C to melt the surface treatment agent;
[0051] 2) Blowing the material in the high-speed mixer into a low-speed mixer with a cooling device, and cooling to room temperature while stirring;
[0052] 3) The cooling material is ball milled to 400 mesh without sieve residue to obtain a modified negative ion additive;
[0053] 4) Take 40 parts of modified anion additives, 50 parts of organic carrier polypropylene, antioxidant 1010: 1 part, lubricant PE wax: 3 parts and put them into the mixer, and mix well;
[0054] 5) The uniformly mixed raw materials are kneaded and extruded through a high-shear twin-screw extruder with an aspect ratio of 45, air-cooled, and cut to obtain an anion masterbatch.
PUM
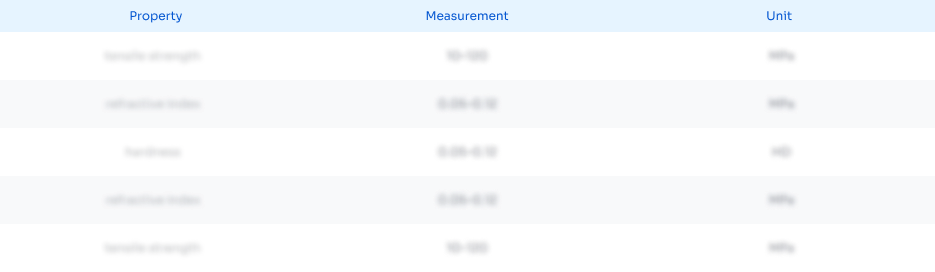
Abstract
Description
Claims
Application Information

- Generate Ideas
- Intellectual Property
- Life Sciences
- Materials
- Tech Scout
- Unparalleled Data Quality
- Higher Quality Content
- 60% Fewer Hallucinations
Browse by: Latest US Patents, China's latest patents, Technical Efficacy Thesaurus, Application Domain, Technology Topic, Popular Technical Reports.
© 2025 PatSnap. All rights reserved.Legal|Privacy policy|Modern Slavery Act Transparency Statement|Sitemap|About US| Contact US: help@patsnap.com