Method for preparing white anticorrosive pigment/filler by using bauxite tailings
A bauxite and anti-corrosion color technology, applied in fibrous fillers, inorganic pigment treatment, chemical instruments and methods, etc., to achieve the effects of low cost, increased application range and added value, and high anti-corrosion performance
- Summary
- Abstract
- Description
- Claims
- Application Information
AI Technical Summary
Problems solved by technology
Method used
Image
Examples
Embodiment 1
[0021] After wet ball milling the bauxite beneficiation tailings until the tailings have a particle size of 95% to -10um, calcinate at 550°C for 3 hours, mix the calcined tailings and water in a beaker at a weight ratio of 1:4, stir, and discard the beaker Larger particles at the bottom (4.6% of tailings in beaker). Add 85% phosphoric acid into a beaker and mix with the tailings according to the molar ratio of phosphorus to all metal elements in the tailings except potassium and sodium as 3, and react at 120°C for 10 hours under sealed conditions. The reactants were polycondensed at 380°C for 12 hours. The polycondensate and zinc oxide are mixed at a weight ratio of 10:1.5, wet ball milled for 3 hours, calcined at 280°C for 3 hours, washed with water, and ball milled. The white powder obtained is the white anti-corrosion pigment and filler.
Embodiment 2
[0023] Dry ball mill the bauxite dressing tailings until the tailings have a particle size of 95% to -10um, then calcinate at 600°C for 2 hours, mix the calcined tailings and water in a beaker at a weight ratio of 1:5, stir and discard Black larger particles at the bottom of the beaker (accounting for about 5% of the tailings in the beaker). Add polyphosphoric acid into a beaker with the molar ratio of phosphorus to all metal elements except potassium and sodium in the tailings at 2.5, mix with the tailings, and react at 100°C for 8 hours under sealed conditions. The reactants were polycondensed at 220°C for 18 hours. Mix the polycondensate and zinc oxide at a weight ratio of 5:1, wet ball mill for 5 hours, calcinate at 300°C for 2 hours, wash with water, and ball mill, and the white powder obtained is the white anti-corrosion pigment and filler.
Embodiment 3
[0025] After wet ball milling the bauxite beneficiation tailings until the tailings have a particle size of 95% to -10um, calcinate at 650°C for 2 hours, mix the calcined tailings and water in a beaker at a weight ratio of 1:4.5, stir and discard Larger particles at the bottom of the beaker (approximately 5% of the tailings in the beaker). Pyrophosphoric acid and all metal elements in the tailings except potassium and sodium in a molar ratio of 4 are added to a beaker and mixed with the tailings, and reacted at 150°C for 6 hours under sealed conditions. The reactants were polycondensed at 300°C for 9 hours. The polycondensate and zinc oxide were mixed in a weight ratio of 6:1, wet ball milled for 4 hours, calcined at 300°C for 2 hours, washed with water, and ball milled. The white powder obtained was the white anti-corrosion pigment and filler. tailings composition
[0026] The composition of the bauxite beneficiation tailings used in the embodiment is shown in Table 1
[0...
PUM
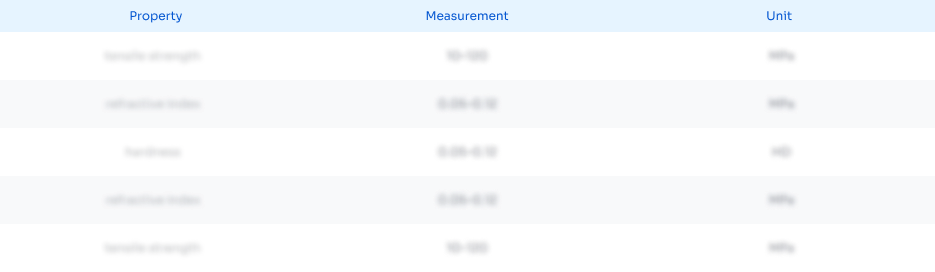
Abstract
Description
Claims
Application Information

- R&D
- Intellectual Property
- Life Sciences
- Materials
- Tech Scout
- Unparalleled Data Quality
- Higher Quality Content
- 60% Fewer Hallucinations
Browse by: Latest US Patents, China's latest patents, Technical Efficacy Thesaurus, Application Domain, Technology Topic, Popular Technical Reports.
© 2025 PatSnap. All rights reserved.Legal|Privacy policy|Modern Slavery Act Transparency Statement|Sitemap|About US| Contact US: help@patsnap.com