Iron alloy-based composite hard alloy roller and production method thereof
A technology of hard alloy and production method, which is applied in the field of rolls, can solve the problems of complex casting process of composite hard alloy roll rings, low metallurgical interface bonding strength, long production cycle, etc., achieve good toughness performance, and improve fracture resistance ability, the effect of increasing production
- Summary
- Abstract
- Description
- Claims
- Application Information
AI Technical Summary
Problems solved by technology
Method used
Examples
Embodiment 1
[0025] Example 1, a ferroalloy-based composite cemented carbide roll is formed by pressing the metal powder constituting the cemented carbide outer ring and the metal powder constituting the ferroalloy inner ring through vacuum pressure sintering, and the cemented carbide outer ring is made of 69%-71% WC, 16%-18% Co, 12%-14% Ni, 0.3% mixed rare earth powder, wherein the mixed rare earth is composed of 50% Ce, 45% La, 3% Z r o 2 , 2%y 2 o 3 Composition; the iron alloy inner ring is made of 20% to 25% of TiC, 0.3% of Ni, 2.5% to 3.5% of Cr, 8.1% to 9.1% of W, 0.4% of C, 2% to 3% of Mo, and The amount is composed of Fe.
[0026]A kind of production method of ferroalloy-based composite cemented carbide roll is that according to the formula of cemented carbide outer ring, the ratio of raw material and alcohol is 5:1 by weight to volume. The present embodiment is WC140kg, Co35.4kg, Ni24kg, mixed rare earth 0.6 kg and 40 liters of alcohol, put them into a stirring ball mill and s...
Embodiment 2
[0027] Embodiment 2, a kind of ferroalloy-based composite cemented carbide roll and production method thereof, is on the basis of embodiment 1, and present embodiment is WC 140kg, Co32.4kg, Ni27kg, mixed rare earth 0.6kg and 40 liters of alcohol, dress Put it into the stirring ball mill and stir the ball mill for 3 hours, pass through a 300-mesh sieve, put it into a Z-type vacuum dryer to heat and vacuum dry, the drying temperature is 100°C, add the dried material to a gasoline rubber solution with a concentration of 12%, and the addition ratio It is 12% gasoline-rubber solution that adding 6-7 kilogram concentration is 12% gasoline-rubber solution for every hundred kilograms of materials, and the present embodiment is that 14kg of 12% gasoline-rubber solution is added to the dried material, stir evenly, vacuum in Z-type vacuum drier. Evaporate to dryness at a temperature of 100°C. Unload the evaporated material and pass it through a 60-mesh sieve, and put it in a bucket for la...
Embodiment 3
[0028] Embodiment 3, a kind of ferroalloy-based composite cemented carbide roll and production method thereof, is on the basis of embodiment 1, and present embodiment is WC 138kg, Co36kg, Ni 25.4kg, mixed rare earth 0.6kg and 40 liters of alcohol, dress Put it into the stirring ball mill and stir the ball mill for 3 hours, pass through a 300-mesh sieve, put it into a Z-type vacuum dryer to heat and vacuum dry, the drying temperature is 100°C, add the dried material to a gasoline rubber solution with a concentration of 12%, and the addition ratio It is 12% gasoline rubber solution that adding 6-7 kilogram concentration is 12% gasoline rubber solution for every hundred kilograms of materials, and the present embodiment is that 12kg gasoline rubber solution 12% is added to the dried material, stir evenly, vacuum in Z-type vacuum drier. Evaporate to dryness at a temperature of 100°C, unload the evaporated material and pass through a 60-mesh sieve, and put it in a barrel for later u...
PUM
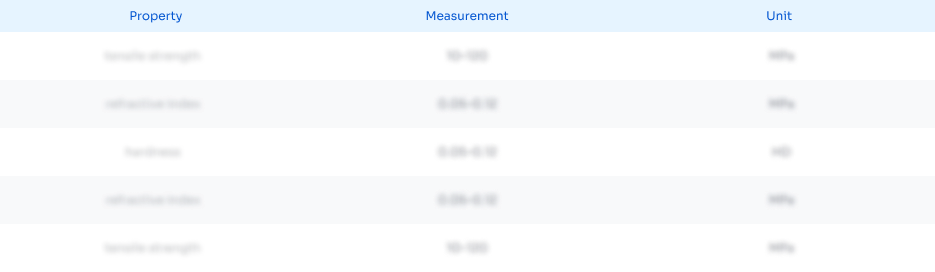
Abstract
Description
Claims
Application Information

- R&D
- Intellectual Property
- Life Sciences
- Materials
- Tech Scout
- Unparalleled Data Quality
- Higher Quality Content
- 60% Fewer Hallucinations
Browse by: Latest US Patents, China's latest patents, Technical Efficacy Thesaurus, Application Domain, Technology Topic, Popular Technical Reports.
© 2025 PatSnap. All rights reserved.Legal|Privacy policy|Modern Slavery Act Transparency Statement|Sitemap|About US| Contact US: help@patsnap.com