Method for preparing hollow silicon carbide nano material
A technology of structural silicon carbide and nanomaterials, applied in the field of synthesizing silicon carbide hollow particles and silicon carbide nanotubes, which can solve the problems of high cost of raw material templates, difficult control of the reaction process, and difficulty in large-scale production
- Summary
- Abstract
- Description
- Claims
- Application Information
AI Technical Summary
Problems solved by technology
Method used
Image
Examples
Embodiment 1
[0016] 1. Weigh 6 grams of phenolic resin, dissolve it in 12 milliliters of absolute ethanol, then add 0.25 grams of ferric nitrate, stir to dissolve it, and dry it at 70°C for 36 hours after the ethanol volatilizes.
[0017] 2. Grind the dried product to obtain a 20-mesh powder, then add it to 13 grams of industrial water glass, form a gel under constant stirring, and dry the obtained gel at 60° C. for 30 hours.
[0018] 3. Put the xerogel into a tube-type high-temperature furnace, raise the temperature to 1200°C under an argon atmosphere, react at a constant temperature for 10 hours, and then cool it down to room temperature naturally.
[0019] 4. The obtained reaction product was oxidized in air at 800°C for 2 hours, then soaked in a mixed acid of hydrochloric acid and hydrofluoric acid with a volume ratio of 1:1.5 for 12 hours, and finally washed, filtered, and dried to obtain silicon carbide hollow nano particles and nanotubes.
Embodiment 2
[0021] 1. Weigh 10 grams of phenolic resin, dissolve it in 25 milliliters of absolute ethanol, then add 2 grams of nickel nitrate, stir to dissolve it, and dry it at 80°C for 24 hours after the ethanol volatilizes.
[0022] 2. Grind the dried product to obtain a 50-mesh powder, then add it into 35 grams of industrial water glass, form a gel under constant stirring, and dry the obtained gel at 70° C. for 24 hours.
[0023] 3. Put the xerogel into a tubular high-temperature furnace, raise the temperature to 1250°C under an argon atmosphere, react at a constant temperature for 8 hours, and then cool it down to room temperature naturally.
[0024] 4. The obtained reaction product was oxidized in air at 600°C for 5 hours, then soaked in a mixed acid of nitric acid and hydrofluoric acid with a volume ratio of 1:2 for 15 hours, and finally washed, filtered and dried to obtain silicon carbide hollow nanometer particles and nanotubes.
Embodiment 3
[0026] 1. Weigh 15 grams of phenolic resin, dissolve it in 55 milliliters of absolute ethanol, then add 9 grams of cobalt nitrate, stir to dissolve it, and dry it at 90°C for 10 hours after the ethanol volatilizes.
[0027] 2. Grind the dried product to obtain 80-mesh powder, then add it into 90 grams of industrial water glass, form a gel under constant stirring, and dry the obtained gel at 80° C. for 24 hours.
[0028] 3. Put the xerogel into a tube-type high-temperature furnace, raise the temperature to 1300°C under an argon atmosphere, react at a constant temperature for 7 hours, and then cool it down to room temperature naturally.
[0029] 4. The obtained reaction product was oxidized in air at 700°C for 3 hours, then soaked in a mixed acid of hydrochloric acid and hydrofluoric acid with a volume ratio of 1:3 for 20 hours, and finally washed, filtered, and dried to obtain silicon carbide hollow nano particles and nanotubes.
PUM
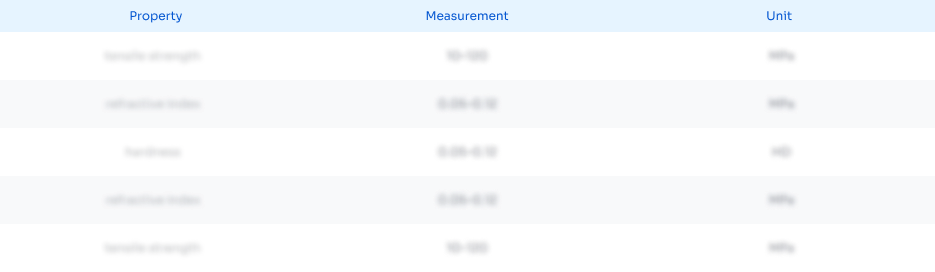
Abstract
Description
Claims
Application Information

- R&D
- Intellectual Property
- Life Sciences
- Materials
- Tech Scout
- Unparalleled Data Quality
- Higher Quality Content
- 60% Fewer Hallucinations
Browse by: Latest US Patents, China's latest patents, Technical Efficacy Thesaurus, Application Domain, Technology Topic, Popular Technical Reports.
© 2025 PatSnap. All rights reserved.Legal|Privacy policy|Modern Slavery Act Transparency Statement|Sitemap|About US| Contact US: help@patsnap.com