Preparation method of copper and indium alloy ink and application thereof
A copper indium alloy and ink technology, applied in the field of solar energy applications, can solve the problems of difficult nanoparticles and the like, and achieve the effects of easy dispersion, good sintering, and suitable particle size distribution
- Summary
- Abstract
- Description
- Claims
- Application Information
AI Technical Summary
Problems solved by technology
Method used
Image
Examples
Embodiment 1
[0026] (1) 1mmol CuCl 2 and 1mmol InCl 3 Dissolved in 20ml of ethylene glycol at 140°C, 0.1g of NaBH 4 The ethylene glycol solution of sodium borohydride obtained by dissolving in 4 ml of ethylene glycol was slowly dropped in and reacted for 30 minutes, and was washed and dried by centrifugation to obtain copper-indium alloy nanoparticles. Prepare the solvent according to ethylene glycol:methanol:ethylene glycol methyl ether=5:1:4 (volume ratio). The ink was prepared according to the amount of copper-indium alloy nanoparticles:solvent=1:4 (mass ratio) and ultrasonically dispersed for 30min. The prepared copper-indium alloy ink was coated on the substrate sheet by doctor-blade method, and dried at 80°C. The precursor film was vulcanized. The vulcanization process was as follows: firstly, the temperature was raised to 400 °C at a rate of 3 °C / min, and the organic solvent was removed by heating under the protection of an inert gas; then the temperature was raised to 550 °C at ...
Embodiment 2
[0029] (1) 2mmol CuCl 2 and 2mmol InCl 3 Dissolved in 40ml of ethylene glycol at 140°C, 0.2g of NaBH 4 The ethylene glycol solution of sodium borohydride obtained by dissolving in 8 ml of ethylene glycol was slowly dropped in and reacted for 30 minutes, and was washed and dried by centrifugation to obtain copper-indium alloy nanoparticles. Prepare the solvent according to ethylene glycol:methanol:ethylene glycol methyl ether=2:1:3 (volume ratio). The ink was prepared according to the amount of copper-indium alloy nanoparticles / solvent=1:2 (mass ratio) and ultrasonically dispersed for 30 minutes. The prepared ink was coated on the substrate sheet by doctor-blade method, and dried at 80°C. The precursor film was vulcanized. The vulcanization process was as follows: firstly, the temperature was raised to 400 °C at a rate of 3 °C / min, and the organic solvent was removed by heating under the protection of an inert gas; then the temperature was raised to 550 °C at a rate of 4 °C / ...
Embodiment 3
[0031] (1) 1mmol CuCl 2 and 1mmol InCl 3 Dissolved in 40ml of ethylene glycol at 100°C, dissolved 0.5g of disodium hypophosphite in 5ml of ethylene glycol to obtain the ethylene glycol solution of disodium hypophosphite slowly dripped and reacted for 40min, and obtained by centrifugal washing and drying Copper-indium alloy nanoparticles. Prepare the solvent according to ethylene glycol:methanol:ethylene glycol methyl ether=7:1:6 (volume ratio). The ink was prepared according to the amount of copper-indium alloy nanoparticles:solvent=1:5 (mass ratio) and ultrasonically dispersed for 30min. The prepared ink was coated on the substrate sheet by doctor-blade method, and dried at 100°C. The precursor film was vulcanized. The vulcanization process was as follows: firstly, the temperature was raised to 400°C at a heating rate of 3°C / min, and the organic solvent was removed by heating under the protection of an inert gas; Carry out vulcanization under sulfur atmosphere for 30min. ...
PUM
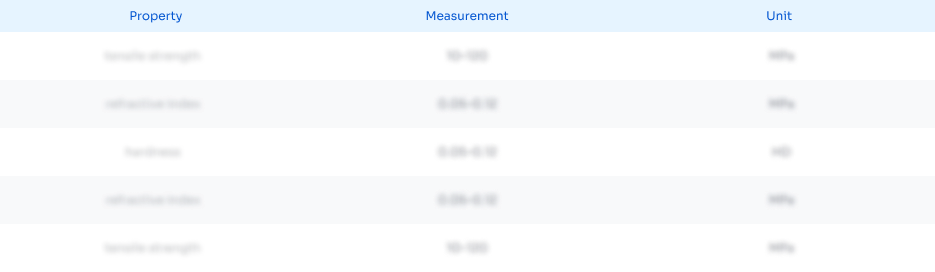
Abstract
Description
Claims
Application Information

- R&D
- Intellectual Property
- Life Sciences
- Materials
- Tech Scout
- Unparalleled Data Quality
- Higher Quality Content
- 60% Fewer Hallucinations
Browse by: Latest US Patents, China's latest patents, Technical Efficacy Thesaurus, Application Domain, Technology Topic, Popular Technical Reports.
© 2025 PatSnap. All rights reserved.Legal|Privacy policy|Modern Slavery Act Transparency Statement|Sitemap|About US| Contact US: help@patsnap.com