Stainless steel plate type heat exchanger and processing molding method thereof
A technology of plate heat exchanger and stainless steel plate, which is applied in forming tools, metal processing equipment, manufacturing tools, etc., can solve the problem that plate heat exchangers are prone to deformation and warpage, refrigerant and condensing oil are easy to accumulate, and stainless steel linear expansion coefficient Large and other problems, to achieve the effect of improving welding efficiency, improving work effect, and reducing refrigerant flow resistance
- Summary
- Abstract
- Description
- Claims
- Application Information
AI Technical Summary
Problems solved by technology
Method used
Image
Examples
Embodiment 1
[0066] see figure 1 and figure 2 , two 304L stainless steel plates with a length of 1.5m, a width of 0.8m, and a thickness of 1.2mm are processed and processed. To form surface micro-patterns, two stainless steel plates are welded at 880 equidistant points by means of current-carrying friction welding with a rotation speed of 2000r / min, a welding speed of 120mm / min, and a current-carrying current of 2KA. Honeycomb solder joints, 4 isolated welds with a length of 1300mm, and the plates are sealed and welded; the aluminum-copper composite inlet pipe and the aluminum-copper composite outlet pipe are sealed and connected to the stainless steel evaporation plate body by arc welding; the inflation positioning mold is adopted, The stainless steel evaporating plate is bulged by high-pressure gas to form a honeycomb-type evaporating plate with hollow channels and dimple-like corrugations on the surface; then other post-welding processes are performed, such as grinding, painting, etc....
Embodiment 2
[0068] see figure 1 and image 3 , Two pieces of 316 stainless steel with a length of 1.5m, a width of 0.8m, and a thickness of 1.3mm are processed and processed, the inner and outer surfaces of the stainless steel plate are subjected to surface shot peening and nano-treatment, and the superimposed inner surface is formed by mechanical micro-rolling The surface is micro-patterned, and laser welding is adopted. The power is 1200W, the welding speed is 1.8m / min, and the attenuation speed is 30%. and sealing and welding the surroundings; the aluminum-copper composite inlet pipe and the aluminum-copper composite outlet pipe are sealed and connected with the stainless steel condensing plate body by arc welding; the inflation positioning mold is used to bulge the stainless steel evaporating plate through high-pressure gas, Make it into a serpentine flow channel type evaporating plate with concave and convex surfaces with semi-cylindrical curved and serpentine hollow flow channels; ...
Embodiment 3
[0070] see figure 1 and image 3 , Two pieces of 18-8 stainless steel with a length of 1.5m, a width of 0.8m, and a thickness of 1.1mm are processed and processed, and the inner and outer surfaces of the stainless steel plate are subjected to surface shot peening and nano-treatment, and the superimposed inner surface is subjected to mechanical micro-rolling Press to form micro-patterns on the surface, adopt water-cooled resistance welding method, weld two stainless steel plates with fourteen equal-spaced welds into the middle weld with welding current of 8KA, welding speed of 45cm / min, and electrode pressure of 5KN. Seal and weld the surroundings; connect the aluminum-copper composite inlet pipe and the aluminum-copper composite outlet pipe with the stainless steel condensing plate body by arc welding; use the inflation positioning mold to bulge the stainless steel evaporating plate with high-pressure gas to make it It is formed into a serpentine flow channel evaporator plate...
PUM
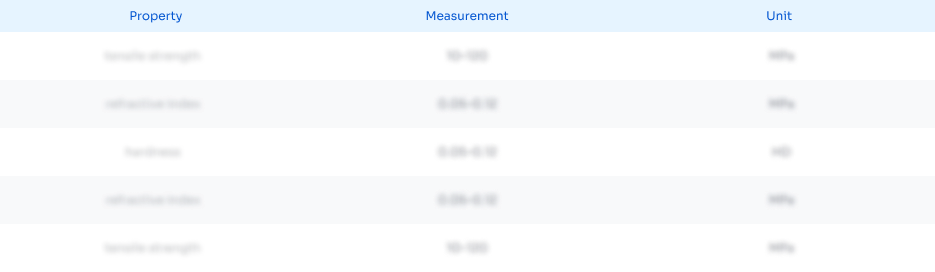
Abstract
Description
Claims
Application Information

- R&D
- Intellectual Property
- Life Sciences
- Materials
- Tech Scout
- Unparalleled Data Quality
- Higher Quality Content
- 60% Fewer Hallucinations
Browse by: Latest US Patents, China's latest patents, Technical Efficacy Thesaurus, Application Domain, Technology Topic, Popular Technical Reports.
© 2025 PatSnap. All rights reserved.Legal|Privacy policy|Modern Slavery Act Transparency Statement|Sitemap|About US| Contact US: help@patsnap.com