Repair method of bores of blast furnace tuyere small sleeve
A technology of a small tuyere cover and a repair method, which is applied in the direction of the tuyere, etc., can solve the problems of falling off of the welding layer, poor repair effect of the small tuyere cover, and weak fusion, etc., and achieves the effect of saving the use cost, solid welding, and reducing consumption.
- Summary
- Abstract
- Description
- Claims
- Application Information
AI Technical Summary
Problems solved by technology
Method used
Image
Examples
Embodiment Construction
[0014] The method for repairing the inner hole of the blast furnace tuyere small sleeve includes the following steps:
[0015] a. Carry out grease removal treatment on the small sleeve of blast furnace tuyere, and sandblasting and derusting treatment on the surface of the inner hole;
[0016] b. Put the small blast furnace tuyere cover into the heating furnace to preheat, raise the temperature to 450-500°C at a rate of 130°C-160°C per hour and keep it warm for 3 hours;
[0017] c. Preheat the beryllium-copper electrode, the preheating temperature is 300°C-350°C and keep it warm for 2 hours, and the blast furnace tuyere cover is surfacing layer by layer with the beryllium-copper electrode at a temperature of 450°C-480°C; the blast furnace tuyere The surfacing welding of the inner hole of the small sleeve is carried out in a closed room; the thickness of the surfacing welding of the front end of the inner hole of the blast furnace tuyere is smaller than that of the rear end;
...
PUM
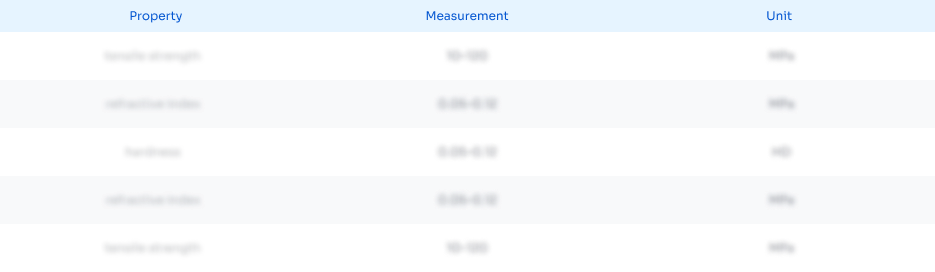
Abstract
Description
Claims
Application Information

- R&D
- Intellectual Property
- Life Sciences
- Materials
- Tech Scout
- Unparalleled Data Quality
- Higher Quality Content
- 60% Fewer Hallucinations
Browse by: Latest US Patents, China's latest patents, Technical Efficacy Thesaurus, Application Domain, Technology Topic, Popular Technical Reports.
© 2025 PatSnap. All rights reserved.Legal|Privacy policy|Modern Slavery Act Transparency Statement|Sitemap|About US| Contact US: help@patsnap.com