Hydrogenation catalyst of distillate oil and preparation method thereof
A hydrogenation catalyst, distillate oil technology, applied in molecular sieve catalysts, chemical instruments and methods, physical/chemical process catalysts, etc., can solve the problems of difficult pore structure, poor hydrothermal stability of carriers, affecting catalyst activity, etc. High degree of dispersion, good hydrothermal stability, and the effect of reducing diffusion limitation
- Summary
- Abstract
- Description
- Claims
- Application Information
AI Technical Summary
Problems solved by technology
Method used
Examples
Embodiment 1
[0028] Preparation of Catalyst Support Z1
[0029] (i) 35g of pseudo-boehmite, 65ml of tetramethoxysilane and 70ml of deionized water were mixed and stirred to obtain paste A;
[0030] (ii) get 40g template agent (polyethylene glycol-polyglycerol-polyethylene glycol EO 20 PO 70 EO 20 , referred to as P 123 ) into 1.3L hydrochloric acid solution (pH value 1.5), stirring constantly to form jelly, adding paste A gradually, and stirring constantly, and continuing to stir for 10 hours after adding completely, the whole process is at 40°C Complete in a constant temperature water bath, then put the obtained mixture B into a high-pressure reactor, and crystallize at 100°C for 24 hours;
[0031] (iii) Take out the crystallized material in the reaction kettle, filter, wash with deionized water, then dry the solid composite at 120°C for 12 hours, and roast at 450°C for 24 hours, and the heating rate before each constant temperature is 3°C / Minutes to get SBA-15 / γ-Al 2 o 3 Composit...
Embodiment 2
[0033] Preparation of Catalyst C1 Using Z1 as Carrier
[0034] Weigh 25.1g of ammonium tetramolybdate (containing molybdenum oxide 85.0%) and add it to 100ml deionized water. After dissolving, add 13.9g ammonium metatungstate (containing tungsten oxide 80.6%) and stir to dissolve; add 5.5g nitric acid to 20ml deionized water Nickel, after stirring to dissolve, mix the two solutions, filter, and add appropriate amount of deionized water to obtain 100ml of stable co-immersion solution. 100 g of the carrier Z1 described in Example 1 was saturated and impregnated with the above co-impregnation solution at room temperature, allowed to stand overnight, then dried at 130°C for 10 hours and at 450°C for 6 hours to obtain catalyst C1. The composition of the catalyst is shown in Table 2.
Embodiment 3
[0036] Preparation of Catalyst Support Z2
[0037] (i) 21g of pseudo-boehmite, 95ml of tetraethoxysilane and 70ml of deionized water were mixed and stirred to obtain paste A;
[0038] (ii) get 40g template agent (polyethylene glycol-polyglycerol-polyethylene glycol EO 20 PO 70 EO 20 , referred to as P 123 ) into 1.3L hydrochloric acid solution (pH value 1.0), stirring continuously to form a jelly, adding the paste A gradually, and stirring continuously, and continuing to stir for 10 hours after adding completely, the whole process is at 40°C Finish in a constant temperature water bath, and then put the obtained mixture B into an autoclave for crystallization at 100° C. for 24 hours.
[0039] (iii) Take out the crystallized material in the reaction kettle, filter, wash with deionized water, then dry the solid composite at 100°C for 48 hours, and roast at 550°C for 6 hours, and the heating rate before each constant temperature is 3°C / minute. Get SBA-15 / γ-Al 2 o 3 Compos...
PUM
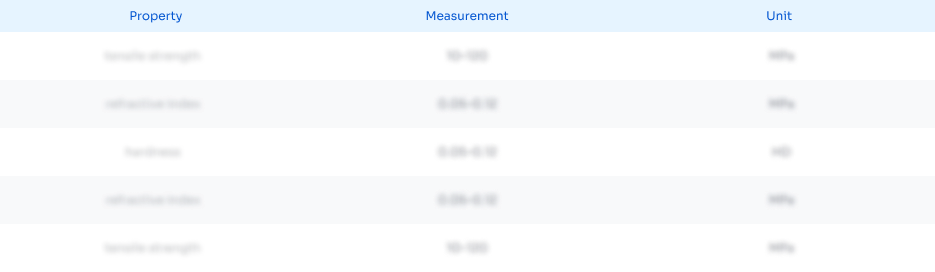
Abstract
Description
Claims
Application Information

- R&D
- Intellectual Property
- Life Sciences
- Materials
- Tech Scout
- Unparalleled Data Quality
- Higher Quality Content
- 60% Fewer Hallucinations
Browse by: Latest US Patents, China's latest patents, Technical Efficacy Thesaurus, Application Domain, Technology Topic, Popular Technical Reports.
© 2025 PatSnap. All rights reserved.Legal|Privacy policy|Modern Slavery Act Transparency Statement|Sitemap|About US| Contact US: help@patsnap.com