Method for preparing metallic matrix composite coating reinforced by alumina ceramics particles
A technology of alumina ceramics and composite materials, applied in metal material coating process, coating, heating inorganic powder coating and other directions, can solve the problems affecting the operation efficiency of thermal power plants, safe operation and power generation costs, and parts wear and ash removal. Technology, difficult to promote and use, etc., to achieve the effect of reducing the cost of coating preparation, high hardness and low price
- Summary
- Abstract
- Description
- Claims
- Application Information
AI Technical Summary
Problems solved by technology
Method used
Image
Examples
Embodiment 1
[0020] Embodiment 1, adopt 22%Al 2 o 3 +78% NiCrBSi mixed spray powder, plasma spray parameters are: current 440A; voltage 47V; primary gas (Ar) 47L / min; secondary gas (H 2 )3L / min; powder feeding speed 30g / min; spraying distance 80mm; spraying speed 90mm / s, to prepare Al 2 o 3P / NiCrBSi composite coating. Al 2 o 3P The erosion wear resistance rate of / NiCrBSi coating is 6.9×10 -3 mm 3 / g-7.2×10 -3 mm 3 / g; coating / substrate interface bonding strength is 30MPa-34MPa.
Embodiment 2
[0021] Embodiment 2, adopt 20% Al 2 o 3 +80% NiCrBSi mixed spray powder, plasma spray parameters are: current 440A; voltage 47V; primary gas (Ar) 47L / min; secondary gas (H 2 )3L / min; powder feeding speed 30g / min; spraying distance 80mm; spraying speed 90mm / s, to prepare Al 2 o 3P / NiCrBSi composite coating. Al 2 o 3P The erosion wear resistance rate of / NiCrBSi coating is 7.2×10 -3 mm 3 / g-7.5×10 -3 mm 3 / g; coating / substrate interface bonding strength is 31MPa-35MPa.
Embodiment 3
[0022] Embodiment 3, adopt 24% Al 2 o 3 +76% NiCrBSi mixed spray powder, plasma spray parameters are: current 440A; voltage 47V; primary gas (Ar) 47L / min; secondary gas (H 2 )3L / min; powder feeding speed 30g / min; spraying distance 80mm; spraying speed 90mm / s, to prepare Al 2 o 3P / NiCrBSi composite coating. Al 2 o 3P The erosion wear resistance rate of / NiCrBSi coating is 7.0×10 -3 mm 3 / g-7.4×10 -3 mm 3 / g; coating / substrate interface bonding strength is 25MPa-30MPa.
PUM
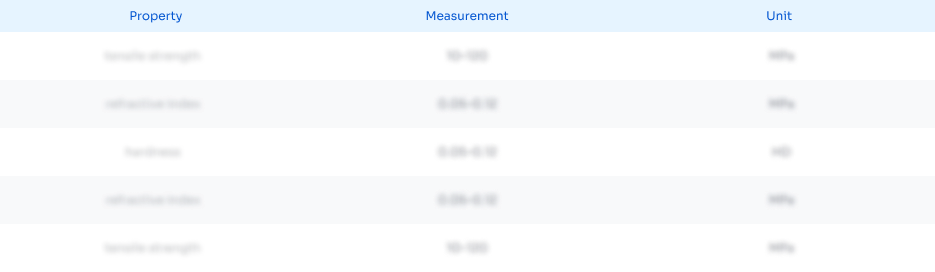
Abstract
Description
Claims
Application Information

- R&D
- Intellectual Property
- Life Sciences
- Materials
- Tech Scout
- Unparalleled Data Quality
- Higher Quality Content
- 60% Fewer Hallucinations
Browse by: Latest US Patents, China's latest patents, Technical Efficacy Thesaurus, Application Domain, Technology Topic, Popular Technical Reports.
© 2025 PatSnap. All rights reserved.Legal|Privacy policy|Modern Slavery Act Transparency Statement|Sitemap|About US| Contact US: help@patsnap.com