Polished sucker rod
A technology for sucking polished rods and nickel-based alloys, applied in drill rods, coatings, metal material coating processes, etc., can solve the problems of difficulty in ensuring the elongation after breaking, reducing the service life of spray welding polished rods, and high production costs. The effect of improving toughness and resistance to crack formation, improving resistance to crack formation and propagation, and improving the ability to resist surface cracks
- Summary
- Abstract
- Description
- Claims
- Application Information
AI Technical Summary
Problems solved by technology
Method used
Image
Examples
Embodiment 1
[0033] A polished oil pumping rod, comprising a base material 1 and a nickel-based alloy coating 2 spray-welded on the surface of the base material 1, the composition of the nickel-based alloy coating in mass percentage is: C: 0.30%, Si: 3.0%, B: 2.0%, Cr: 10.0%, Cu: 12.0%, Fe: 3.0%, and the balance is nickel. The composition of the substrate in terms of mass percentage is: C: 0.13%, Si: 1.30%, Mn: 0.95%, Cr: 1.60%, Nb: 0.04%, Ti: 0.02%, Mo: 0.2%, Ni: 0.2 %, S: 0.010%, P: 0.007%, and the balance is iron. The preparation process of the oil pumping polished rod of the present invention is: cold drawing-upsetting-whole rod normalizing-whole rod tempering-machining-heat treatment such as thermal spraying and remelting of nickel-based alloy coating-coating surface grinding and polishing.
Embodiment 2
[0035] A polished oil pumping rod, comprising a base material 1 and a nickel-based alloy coating 2 spray-welded on the surface of the base material 1, the composition of the nickel-based alloy coating in terms of mass percentage is: C: 0.40%, Si: 2.5%, B: 3.0%, Cr: 8.0%, Cu: 9.0%, Fe: 2.0%, and the balance is nickel. The composition of the substrate in terms of mass percentage is: C: 0.14%, Si: 1.00%, Mn: 1.25%, Cr: 1.40%, Nb: 0.03%, Ti: 0.04%, Mo: 0.1%, Ni: 0.15 %, S: 0.008%, P: 0.010%, and the balance is iron. The preparation process of the oil pumping polished rod of the present invention is: cold drawing-upsetting-whole rod normalizing-whole rod tempering-machining-heat treatment such as thermal spraying and remelting of nickel-based alloy coating-coating surface grinding and polishing.
Embodiment 3
[0037] A polished oil pumping rod, comprising a base material 1 and a nickel-based alloy coating 2 spray-welded on the surface of the base material 1, the composition of the nickel-based alloy coating in terms of mass percentage is: C: 0.10%, Si: 2.2%, B: 2.5%, Cr: 7.5%, Cu: 7.0%, Fe: 5.0%, and the balance is nickel. The composition of the substrate in terms of mass percentage is: C: 0.17%, Si: 0.60%, Mn: 0.80%, Cr: 1.70%, Nb: 0.06%, Ti: 0.03%, Mo: 0.15%, Ni: 0.2 %, S: 0.010%, P: 0.005%, and the balance is iron. The preparation process of the oil pumping polished rod of the present invention is: cold drawing-upsetting-whole rod normalizing-whole rod tempering-machining-heat treatment such as thermal spraying and remelting of nickel-based alloy coating-coating surface grinding and polishing.
PUM
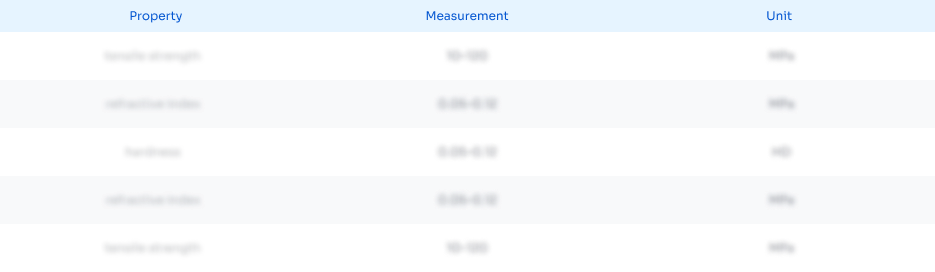
Abstract
Description
Claims
Application Information

- R&D Engineer
- R&D Manager
- IP Professional
- Industry Leading Data Capabilities
- Powerful AI technology
- Patent DNA Extraction
Browse by: Latest US Patents, China's latest patents, Technical Efficacy Thesaurus, Application Domain, Technology Topic, Popular Technical Reports.
© 2024 PatSnap. All rights reserved.Legal|Privacy policy|Modern Slavery Act Transparency Statement|Sitemap|About US| Contact US: help@patsnap.com