Silicon nitride ceramics enhanced by boron nitride nanotube and preparation method thereof
A technology of boron nitride nanotubes and silicon nitride ceramics, applied in the field of silicon nitride ceramics and its preparation, can solve the problems of reducing the toughening effect and the like, and achieve the effects of low cost, simple operation and processing, and stable preparation process
- Summary
- Abstract
- Description
- Claims
- Application Information
AI Technical Summary
Problems solved by technology
Method used
Image
Examples
Embodiment 1
[0024] Example 1: Boron nitride nanotubes are used as reinforcing phase, silicon nitride is used as matrix, and aluminum oxide and yttrium oxide are used as sintering aids to prepare silicon nitride ceramics by hot pressing and sintering. Weigh 0.0875g of boron nitride nanotubes, 31.4125g of silicon nitride and 3.5g of sintering aids (including 2.1g of alumina and 1.4g of yttrium oxide) with a balance, and put 245g of agate balls into a planetary ball mill jar. At room temperature, the rotation speed of the planetary ball mill jar was 300r / min, and the ball mill was performed for 10 hours. Put the ball-milled mixed powder into a graphite mold with a diameter of 42mm, heat up to 1750°C at a rate of 20°C / min in a multifunctional sintering furnace, pressurize at 25Mpa for sintering, and stop heating after 45 minutes of heat preservation to make it sinter in the furnace Cool naturally to room temperature. The sintered ceramic block is finished by grinding, cutting and other proce...
Embodiment 2
[0025] Example 2: Boron nitride nanotubes are used as reinforcing phase, silicon nitride is used as matrix, and aluminum oxide and yttrium oxide are used as sintering aids to prepare silicon nitride ceramics by hot pressing and sintering. Weigh 0.7g of boron nitride nanotubes, 30.8g of silicon nitride and 3.5g of sintering aids (including 2.1g of alumina and 1.4g of yttrium oxide) with a balance, and put 245g of agate balls into a planetary ball mill jar. At room temperature, the rotational speed of the planetary ball mill jar was 290r / min, and the ball milled for 9 hours. Put the ball-milled mixed powder into a graphite mold with a diameter of 42mm, heat up to 1740°C at a rate of 19°C / min in a multifunctional sintering furnace, pressurize at 24Mpa for sintering, and stop heating after holding for 40 minutes to make it in the furnace Cool naturally to room temperature. The sintered ceramic block is finished by grinding, cutting and other processes.
Embodiment 3
[0026] Example 3: Boron nitride nanotubes are used as reinforcing phase, silicon nitride is used as matrix, and aluminum oxide and yttrium oxide are used as sintering aids to prepare silicon nitride ceramics by hot pressing and sintering. Weigh 1.75g of boron nitride nanotubes, 29.75g of silicon nitride and 3.5g of sintering aids (including 2.1g of alumina and 1.4g of yttrium oxide) with a balance, and put 245g of agate balls into a planetary ball mill jar. At room temperature, the rotation speed of the planetary ball mill jar was 310r / min, and the ball mill was performed for 11 hours. Put the ball-milled mixed powder into a graphite mold with a diameter of 42mm, heat up to 1760°C at a rate of 21°C / min in a multifunctional sintering furnace, pressurize at 26Mpa for sintering, and stop heating after holding for 50 minutes. Cool naturally to room temperature. The sintered ceramic block is finished by grinding, cutting and other processes.
PUM
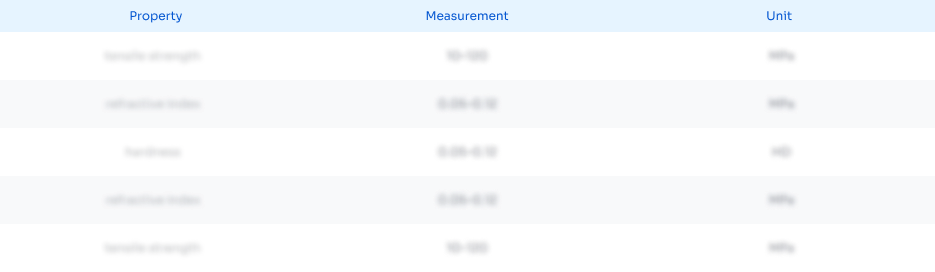
Abstract
Description
Claims
Application Information

- R&D
- Intellectual Property
- Life Sciences
- Materials
- Tech Scout
- Unparalleled Data Quality
- Higher Quality Content
- 60% Fewer Hallucinations
Browse by: Latest US Patents, China's latest patents, Technical Efficacy Thesaurus, Application Domain, Technology Topic, Popular Technical Reports.
© 2025 PatSnap. All rights reserved.Legal|Privacy policy|Modern Slavery Act Transparency Statement|Sitemap|About US| Contact US: help@patsnap.com