Method for recycling ruthenium from ruthenium-containing waste
A waste, ruthenium tetroxide technology, applied in the direction of improving process efficiency, can solve problems such as insufficient separation, low ruthenium recovery rate, and inability to efficiently purify
- Summary
- Abstract
- Description
- Claims
- Application Information
AI Technical Summary
Problems solved by technology
Method used
Image
Examples
Embodiment 1
[0047] Examples of the present invention are described below. 5.2 kg of sodium chloride and 240 g of carbon powder were mixed with 1.0 kg of grinding dust and mixed waste of grinding dust generated when the ruthenium target was machined. The composition and content of the mixed waste are shown in Table 1. Here, the amount of sodium chloride added was 5.8 times the equivalent, and the amount of carbon was 1.9 times the equivalent of the amount of ruthenium contained in the scrap.
[0048] Table 1 Composition and content of waste materials containing ruthenium
[0049] Ru Al Ag Cu Ni Grade (mass%) 51.9 21.8 0.39 1.43 0.38 Content (g) 519 218 4 14 4
[0050] This mixture was put into a quartz boat, and heated to 780° C. in a tubular furnace whose core tube was made of quartz while circulating chlorine gas, and subjected to a chlorination roasting treatment for 3 hours.
[0051] The processed product was leached in warm water kept at 8...
Embodiment 2
[0062] In Example 2, the block-shaped end material scrap of the shaped ruthenium target is used as the raw material. The bulky end material waste was crushed with a crusher, and then pulverized with a hammer mill to obtain a powder sample that passed through a sieve with a mesh size of 500 μm. Table 5 shows the composition and content of the powder samples that passed through the sieve. 4.8 kg of sodium chloride and 220 g of carbon powder were mixed in 1.0 kg of the powder material. Here, the amount of sodium chloride added was 3.0 times the equivalent, and the amount of carbon was 1.0 times the equivalent of the amount of ruthenium contained in the waste.
[0063] Table 5 Composition and content of pulverized scrap containing ruthenium
[0064] Ru Fe Al Cr Ni Grade (mass%) 91.2 6.5 0.84 0.33 0.20 Content (g) 912 65 8 3 2
[0065] Put...
PUM
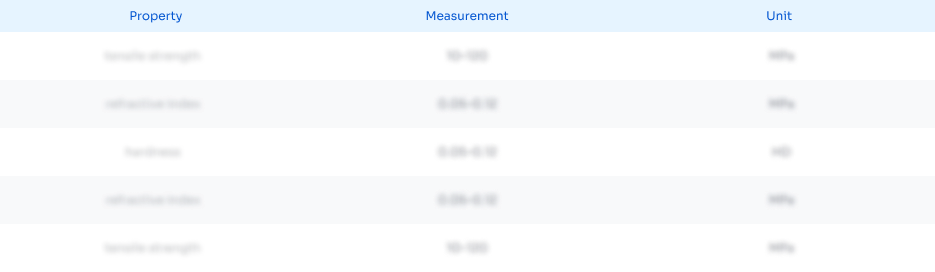
Abstract
Description
Claims
Application Information

- Generate Ideas
- Intellectual Property
- Life Sciences
- Materials
- Tech Scout
- Unparalleled Data Quality
- Higher Quality Content
- 60% Fewer Hallucinations
Browse by: Latest US Patents, China's latest patents, Technical Efficacy Thesaurus, Application Domain, Technology Topic, Popular Technical Reports.
© 2025 PatSnap. All rights reserved.Legal|Privacy policy|Modern Slavery Act Transparency Statement|Sitemap|About US| Contact US: help@patsnap.com