Plastic repair material for ladle working lining
A repairing material and working lining technology, applied in the field of refractory materials, can solve the problems of high rebound loss of materials, not resistant to erosion, and the thickness of the repairing material should not be too thick, so as to achieve the effect of no environmental pollution, guaranteeing the repairing quality and shortening the maintenance time.
- Summary
- Abstract
- Description
- Claims
- Application Information
AI Technical Summary
Problems solved by technology
Method used
Image
Examples
Embodiment Construction
[0021] First, add the weighed high-alumina bauxite and corundum granules into the mixer for pre-mixing for 1-2 minutes, then add part of the silica sol solution and mix for 3-4 minutes, then add corundum powder and magnesia powder for 3- After 5 minutes, add the rest of the silica sol and mix thoroughly until the material is discharged; depending on the condition of the mixed material, add some water to adjust it to be suitable for construction.
[0022] The comparison between the embodiments of the present invention and the prior art is shown in Table 1. Wherein 1, 2, 3, 4 are the embodiments of this patent, 5 is the smear repair material generally used at present, 6 is the embodiment among the patent 200510026322.4.
[0023] Table 1 The proportioning and performance of the embodiment of the present invention and the comparative example of the prior art
[0024]
[0025] As can be seen from Table 1, the obvious advantage of this embodiment of the invention is that the har...
PUM
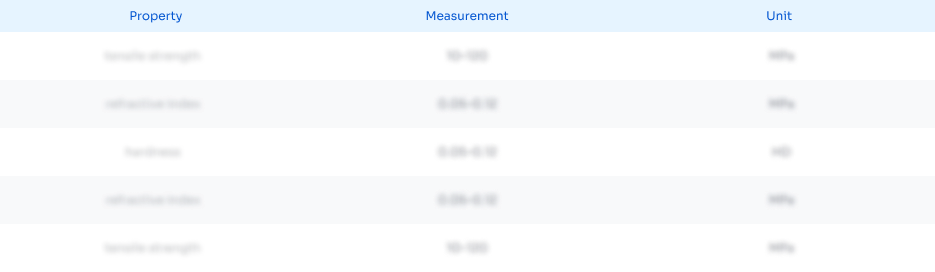
Abstract
Description
Claims
Application Information

- R&D Engineer
- R&D Manager
- IP Professional
- Industry Leading Data Capabilities
- Powerful AI technology
- Patent DNA Extraction
Browse by: Latest US Patents, China's latest patents, Technical Efficacy Thesaurus, Application Domain, Technology Topic, Popular Technical Reports.
© 2024 PatSnap. All rights reserved.Legal|Privacy policy|Modern Slavery Act Transparency Statement|Sitemap|About US| Contact US: help@patsnap.com