Method for preparing ruthenium-containing corrosion resistant titanium alloy
A titanium alloy and corrosion-resistant technology, which is applied in the field of preparation of ruthenium-containing corrosion-resistant titanium alloy, can solve the problems of high cost, long cycle, and many processes, and achieve the effects of simple operation, low cost, and stable chemical properties
- Summary
- Abstract
- Description
- Claims
- Application Information
AI Technical Summary
Problems solved by technology
Method used
Examples
Embodiment 1
[0022] Accurately weigh 100kg of titanium sponge and 0.11kg of ruthenium powder (particle size: -70 mesh), fully mix the ruthenium powder and titanium sponge and press it into an electrode block, and use plasma arc welding to weld the electrode block into titanium of the required specification The electrodes are then smelted into ingots by vacuum electric arc furnace at least twice. After strict process control of batching, electrode pressing, electrode welding, and smelting, the ruthenium content of the head and bottom of the titanium ingot is 0.10% and 0.105%, and the ingot is inspected by chemical composition analysis and surface quality. After passing the forging, rolling, etc. The TA27 (Ti-0.10Ru) titanium material with good quality is produced to meet the needs of industrial use.
Embodiment 2
[0024] Accurately take required sponge titanium, aluminum-vanadium master alloy and pure aluminum 1000kg altogether, mix into ruthenium powder 1.1kg (particle size:-100 order), its nominal chemical composition Ti-6Al-4V-0.11Ru (wt%), The TC23 alloy ingot containing ruthenium can be obtained according to the steps in Example 1, and the chemical analysis results of the ruthenium content at the head and bottom of the titanium ingot are: 0.10%, 0.11%.
PUM
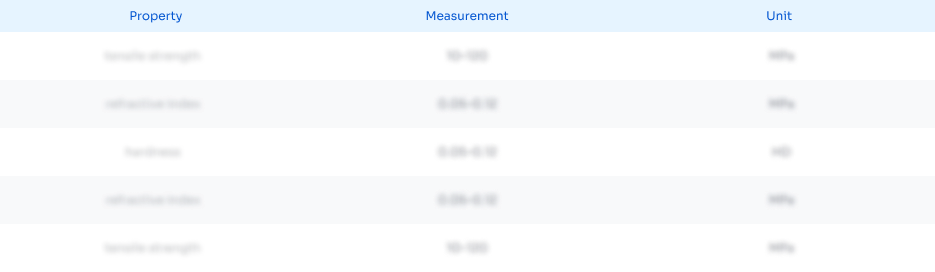
Abstract
Description
Claims
Application Information

- Generate Ideas
- Intellectual Property
- Life Sciences
- Materials
- Tech Scout
- Unparalleled Data Quality
- Higher Quality Content
- 60% Fewer Hallucinations
Browse by: Latest US Patents, China's latest patents, Technical Efficacy Thesaurus, Application Domain, Technology Topic, Popular Technical Reports.
© 2025 PatSnap. All rights reserved.Legal|Privacy policy|Modern Slavery Act Transparency Statement|Sitemap|About US| Contact US: help@patsnap.com