Stir friction composite welding stainless steel device with resistor heat and method thereof
A technology of friction stir and composite welding, which is applied in the field of friction stir welding stainless steel equipment, resistance heat-friction stir composite welding stainless steel equipment, which can solve the problems of embrittlement of joints, high heat loss, long heating time, etc., and achieve increased Welding length, extended service life, easy-to-achieve effects
- Summary
- Abstract
- Description
- Claims
- Application Information
AI Technical Summary
Problems solved by technology
Method used
Image
Examples
specific Embodiment 1
[0021] Weld 3mm thick 316 stainless steel, the stirring head is tungsten alloy steel, the shaft shoulder diameter is 16mm, the stirring pin diameter is 5mm, and the length is 2.9mm. Using the resistance heating-friction stir composite welding process of the present invention, the rotation speed of the stirring head is 950r / min, the welding speed is 60mm / min, and the auxiliary current is 1000A. The welding length is 150mm, the tensile strength of the welded stainless steel welded joint reaches 86% of the base metal, and the wear of the stirring head is relatively light.
[0022] In the absence of an auxiliary heat source, friction stir welding cannot form an effective connection, and the stirring head is severely worn.
specific Embodiment 2
[0023]Weld 3mm thick 304 stainless steel, the stirring head is tungsten alloy steel, the shaft shoulder diameter is 16mm, the stirring pin diameter is 5mm, and the length is 2.9mm. The resistance heat-friction stir composite welding stainless steel device of the present invention is used for welding, the rotation speed of the stirring head is 950r / min, the welding speed is 60mm / min, the auxiliary current is 1000A, and the welding length is 142mm. The tensile strength of the stainless steel welded joint after welding reaches 85% of the base metal, and the wear of the stirring head is relatively light.
[0024] In the absence of an auxiliary heat source, friction stir welding cannot form an effective connection, and the stirring head is severely worn.
[0025] It can be seen from the above examples that using the device of the present invention to weld stainless steel can effectively reduce the difficulty of friction stir welding of stainless steel. At the same time, it reduces...
PUM
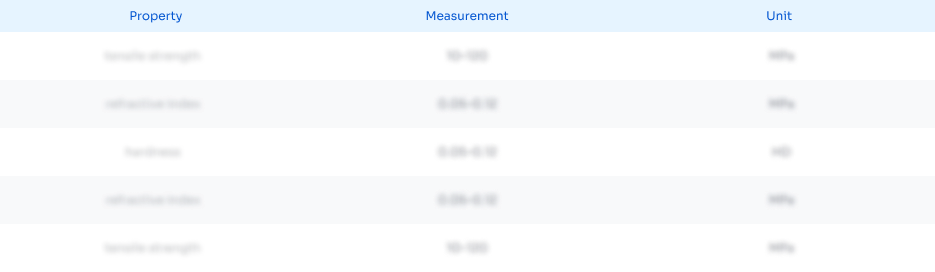
Abstract
Description
Claims
Application Information

- R&D
- Intellectual Property
- Life Sciences
- Materials
- Tech Scout
- Unparalleled Data Quality
- Higher Quality Content
- 60% Fewer Hallucinations
Browse by: Latest US Patents, China's latest patents, Technical Efficacy Thesaurus, Application Domain, Technology Topic, Popular Technical Reports.
© 2025 PatSnap. All rights reserved.Legal|Privacy policy|Modern Slavery Act Transparency Statement|Sitemap|About US| Contact US: help@patsnap.com