Preparing technology of polyurethane modified ethoxyline resin adapted for composite wear-resistant coating material
A polyurethane modification and epoxy resin technology, applied in the direction of polyurea/polyurethane coatings, coatings, etc., can solve problems such as poor flexibility, achieve high bonding strength, save production costs, flexibility and impact resistance Good results
- Summary
- Abstract
- Description
- Claims
- Application Information
AI Technical Summary
Problems solved by technology
Method used
Examples
Embodiment 1
[0017] The invention discloses a preparation process of polyurethane modified epoxy resin suitable for composite wear-resistant coating materials, which uses polyether diol with a functionality of 2 and an average relative molecular weight of 1200-2200 and preheated toluene Diisocyanate or diphenylmethane-4,4'-diisocyanate reacts to synthesize polyether diol polyurethane prepolymer, standby; select bisphenol A type E-44 or E-51 epoxy resin that has been pre-dehydrated One of them is ready for use; according to the mass ratio of polyether diol polyurethane prepolymer and epoxy resin at 15-70:100, it undergoes polyaddition reaction to form polyurethane-modified epoxy resin.
Embodiment 2
[0019] As a preferred embodiment of the present invention, on the basis of Example 1, the polyether glycol described in the present invention is selected from polypropylene glycol, polytetrahydrofuran, tetrahydrofuran-propylene oxide copolyether or polyε-caprolactone wherein A sort of.
Embodiment 3
[0021] Bisphenol A type E-44 and E-51 type epoxy resins are modified with polyether glycol polyurethane prepolymer to obtain polyurethane modified epoxy resins. The specific operation steps are as follows:
[0022] a. Add the calculated amount of bisphenol A type E-44 or E-51 epoxy resin into the stainless steel vacuum dehydration kettle, heat to 100-120°C, vacuumize, keep the vacuum degree of 10-80mmHg, and remove moisture for 1-2 hours. spare. According to the mass ratio epoxy resin: polyether glycol polyurethane = 100: 15-70 to prepare materials.
[0023] b. Add the calculated amount of toluene diisocyanate (TDI) or diphenylmethane-4,4'-diisocyanate (MDI) into the stainless steel preheating kettle, preheat to 50-60°C, and set aside. According to the molar ratio of isocyanate NCO:hydroxyl OH=2:1, and the excess of isocyanate NCO is 3-5%, the proportioning reaction is carried out to prepare materials.
[0024] C. Add one of polypropylene glycol, polytetrahydrofuran, tetrahy...
PUM
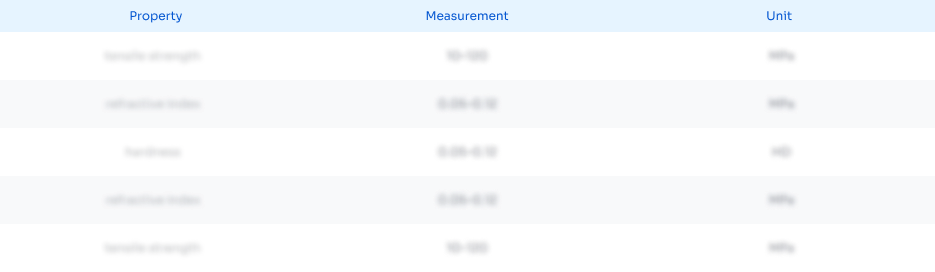
Abstract
Description
Claims
Application Information

- Generate Ideas
- Intellectual Property
- Life Sciences
- Materials
- Tech Scout
- Unparalleled Data Quality
- Higher Quality Content
- 60% Fewer Hallucinations
Browse by: Latest US Patents, China's latest patents, Technical Efficacy Thesaurus, Application Domain, Technology Topic, Popular Technical Reports.
© 2025 PatSnap. All rights reserved.Legal|Privacy policy|Modern Slavery Act Transparency Statement|Sitemap|About US| Contact US: help@patsnap.com