Fabrication method of Ti movable device
A manufacturing method and device technology, applied in the manufacture of microstructure devices, processes for producing decorative surface effects, coatings, etc., can solve problems such as poor fracture toughness, complex processes, large aspect ratio, etc., and achieve self-stress Small, uniform etching, bright surface effect
- Summary
- Abstract
- Description
- Claims
- Application Information
AI Technical Summary
Problems solved by technology
Method used
Image
Examples
Embodiment 1
[0037] Example 1 Using SU8 as the middle layer for bonding
[0038] 1. Titanium Substrate Preparation and Mask Generation
[0039] Such as figure 1 As shown, the device material is titanium, and after annealing and chemical mechanical polishing, the surface of the titanium substrate is flat and bright. The mask is made of SU8 photoresist. SU8 is a kind of thick glue, different thickness can be obtained under different speed. The mask thickness is determined according to the required thickness of the device. In this embodiment, the device height is expected to be 40 microns, and it is recommended to use undiluted SU8-3010 at a rotation speed of 1000 to obtain a thickness of about 15 microns.
[0040] 2. Define the mask pattern
[0041] The pattern is defined by photolithography and development, and after pre-baking, exposure, development, and post-exposure baking (Post Exposure Bake), a mask pattern with flat and steep side walls can be obtained, such as figure 2 shown. ...
Embodiment 2
[0053] Example 2 Using BCB as the middle layer for bonding
[0054] Steps 1 to 6 are the same as in Example 1. When bonding in step 7, benzocyclobutene polymer (BCB, Benzocyclobutene) is used as the intermediate layer, and the pattern is defined before bonding. First coat the BCB on the bonded glass sheet, then use the photoresist as a mask to define the BCB pattern, and use the plasma dry etching method to etch and pattern the BCB, and then perform the same step 6 to obtain Patterned bonding of titanium substrates, such as Figure 10 shown. Subsequent steps are similar to those in Embodiment 1. In the final process of structure release, it is only necessary to remove the filled Parylene material with oxygen plasma.
PUM
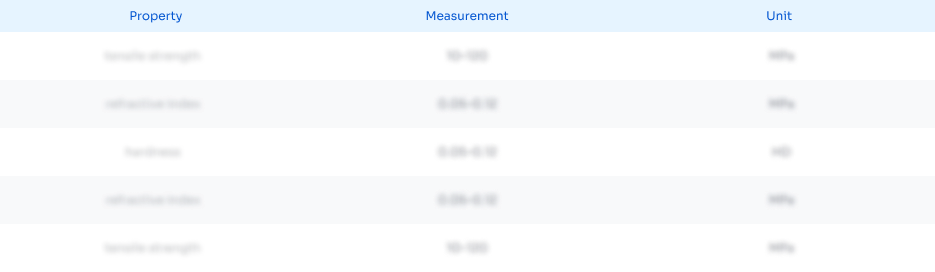
Abstract
Description
Claims
Application Information

- R&D
- Intellectual Property
- Life Sciences
- Materials
- Tech Scout
- Unparalleled Data Quality
- Higher Quality Content
- 60% Fewer Hallucinations
Browse by: Latest US Patents, China's latest patents, Technical Efficacy Thesaurus, Application Domain, Technology Topic, Popular Technical Reports.
© 2025 PatSnap. All rights reserved.Legal|Privacy policy|Modern Slavery Act Transparency Statement|Sitemap|About US| Contact US: help@patsnap.com