Method for processing coloured foreign fiber burnt-out fabric
A processing method and burnt-out technology, applied in the field of knitted fabric processing, can solve the problems of impossibility and single layered feeling, and achieve the effect of ideal warmth retention, clear pattern and good softness
- Summary
- Abstract
- Description
- Claims
- Application Information
AI Technical Summary
Problems solved by technology
Method used
Image
Examples
Embodiment 1
[0031] according to figure 1 Process flow shown:
[0032] A) raw material selection, choose 100D / 48F FDY colored polyester filament and 100D / 48F DTY colored polyester network filament as the bottom texture raw material, i.e. bottom yarn, choose 21S ring spinning pure cotton yarn as surface texture raw material, i.e. surface yarn, wherein : The mass percentage that colored polyester filament accounts for is 23%, and the mass percentage that 21S ring-spun pure cotton yarn accounts for is 77%. The pile yarn is located on the two bars of GB1 and GB4, while the GB2 bar uses 100D / 48F
[0033] DTY colored polyester network filaments, 100D / 48F FDY colored polyester filaments for GB3 bar, colored polyester filaments are made of light green, yellow, blue, dark green four colors, the warping machine is warped in strips according to the color needs On the pan head ;
[0034] B) Weaving, put the 100D / 48F FDY colored polyester filament warped by step A), the 100D / 48F DTY colored polyeste...
Embodiment 2
[0044] according to figure 1 Process flow shown.
[0045] A) Raw material selection, choose 100D / 72F FDY colored polyester filament and 150D / 72F DTY colored polyester network filament as the bottom texture raw material, that is, bottom yarn, choose GB1 to use 32S, GB4 to use 16S ring spinning pure cotton yarn as surface texture The raw material is face silk, wherein: the mass percentage that colored polyester filament accounts for is 29%, and the mass percentage that 21S and 16S ring spinning pure cotton yarn accounts for is 71%. 21S ring spun pure cotton yarn is placed on GB1 as raised loop yarn, 16S ring spun pure cotton yarn is placed on GB4 as raised loop yarn, while GB2 uses 150D / 72F DTY colored polyester network filament, and GB3 uses 100D / 72F FDY Colored polyester filaments, colored polyester filaments are made of light green, yellow, blue, orange, and dark green, and are warped on the pan head in strips according to the color requirements of the warping machine;
[0...
Embodiment 3
[0056] according to figure 1 Process flow shown.
[0057] A) Raw material selection, choose 100D / 72F FDY colored polyester filament and 100D / 72F DTY colored polyester network filament as the base material, that is, bottom yarn, choose GB1 to use 16S ring spinning pure cotton yarn, GB4 use 32S ring spinning The pure cotton yarn is used as the raw material of the surface texture, namely the face silk, wherein the mass percentage of colored polyester filament is 24%, and the mass percentage of 21S and 16S ring-spun pure cotton yarn is 76%. Warping machine warping, 16S ring-spun pure cotton yarn is placed on GB1 as a loop yarn, 32S ring-spun pure cotton yarn is placed on GB4 as a loop yarn, and GB2 uses 100D / 72F DTY colored polyester network filament, 100D / 72F FDY colored polyester filaments are used for GB3. The colored polyester filaments are made of dark purple, light purple and pink, and are warped on the pan head in strips according to the color requirements of the warping m...
PUM
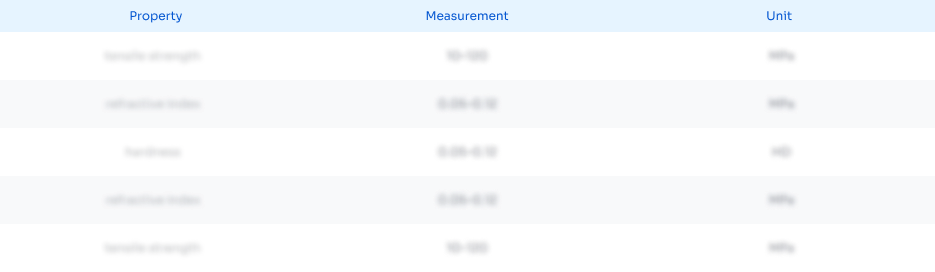
Abstract
Description
Claims
Application Information

- R&D
- Intellectual Property
- Life Sciences
- Materials
- Tech Scout
- Unparalleled Data Quality
- Higher Quality Content
- 60% Fewer Hallucinations
Browse by: Latest US Patents, China's latest patents, Technical Efficacy Thesaurus, Application Domain, Technology Topic, Popular Technical Reports.
© 2025 PatSnap. All rights reserved.Legal|Privacy policy|Modern Slavery Act Transparency Statement|Sitemap|About US| Contact US: help@patsnap.com