Method for preparing protecting residue from recovery refining slag
A technology of refining slag and mold slag, which is applied in the field of recovering refining slag to prepare mold slag, which can solve the problems that the chemical composition cannot be fully utilized, the thermal conductivity of the mixture is large, and the production cannot be carried out, so as to reduce the energy consumption of the preparation and reduce the dust. Pollution, cost-saving effect
- Summary
- Abstract
- Description
- Claims
- Application Information
AI Technical Summary
Problems solved by technology
Method used
Image
Examples
Embodiment 1
[0029] Example 1: Preparation of tundish mold flux, the ingredients are shown in Table 3-1. The reclaimed refined slag recovered from the steel mill after natural cooling is magnetically separated to remove iron, and the sieved material is sieved with a 100-mesh sieve. The analysis components are shown in Table 3-2, which are basically the same as those required for the tundish mold slag. Need to add suspending agent, binding agent, spray granulation. Get under the sieve and reclaim refined slag powder 94.3wt%, sodium butyl xanthate (C 4 h 9 OCSSNa) 1.5wt%, cornstarch 4.2wt%, mix the above raw materials, add water to make a slurry with a solid content of 55.56wt%, adopt automatic frequency conversion temperature control hot air stove, control the temperature of the hot air at the top of the tower at about 570 ° C, and spray Granulate.
[0030] Table 3-1 Tundish Mold Flux Composition (wt%)
[0031] CaO SiO2 MgO Al2O3 FeO CaF2 P S 45.83 6.32 8.11 ...
Embodiment 2
[0034] Example 2: Preparation of continuous casting mold flux, the composition is shown in Table 4-1. The reclaimed refined slag recovered from the steel mill after natural cooling, iron-removed by magnetic separation, sieved with a 100-mesh sieve to get the undersize, the analysis components are shown in Table 4-2. Add suspending agent, binder, deflocculating agent, water reducing agent according to the principle of making up the gap, and make slurry and spray granulate. Get under the sieve and reclaim refining slag powder 74.8wt%, sodium butyl xanthate (C 4 h 9 OCSSNa) 2.0wt%, calcium lignosulfonate 0.5wt%, boric acid 1.2wt%, cornstarch 3.3wt%, wollastonite 5wt%, waste glass 12wt%, soda ash 1.2wt% (additional raw material also all gets 100 mesh sieves Bottom), the above raw materials are mixed, and water is added to make a slurry with a solid content of 52.63wt%, and an automatic frequency conversion temperature-controlled hot blast furnace is used to control the temperatu...
Embodiment 3
[0039] Example 3: Preparation of heat preservation agent for ladle, the ingredients are shown in Table 5-1. The reclaimed refined slag recovered from the steel mill after natural cooling is magnetically separated to remove iron, sieved with a 100-mesh sieve to get the sieve, and the analysis components are shown in Table 5-2), according to the principle of filling up the gap, adding a suspending agent, combining agent, anti-flocculant, slurry spray granulation. Get under the sieve and reclaim refined slag powder 71.9wt%, sodium butyl xanthate (C 4 h 9 OCSSNa) 1.3wt%, cornstarch 3.8wt%, vermiculite 8%, coke powder 15wt% (additional raw materials also all get 100 mesh sieves), above-mentioned raw materials are mixed, add water and make the slurry of solid content 68.08wt% The material is sprayed and granulated by using an automatic frequency conversion temperature-controlled hot air stove to control the temperature of the hot air at the top of the tower at about 550 °C. C+R2O...
PUM
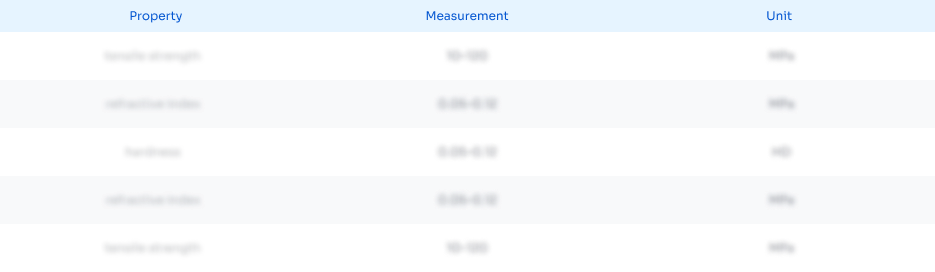
Abstract
Description
Claims
Application Information

- R&D
- Intellectual Property
- Life Sciences
- Materials
- Tech Scout
- Unparalleled Data Quality
- Higher Quality Content
- 60% Fewer Hallucinations
Browse by: Latest US Patents, China's latest patents, Technical Efficacy Thesaurus, Application Domain, Technology Topic, Popular Technical Reports.
© 2025 PatSnap. All rights reserved.Legal|Privacy policy|Modern Slavery Act Transparency Statement|Sitemap|About US| Contact US: help@patsnap.com