Method for manufacturing electric plating diamond burr
A technology for electroplating diamond and manufacturing method, which is applied to electrolytic coatings, dental tools, coatings, etc., can solve the problems of easy falling off of diamond particles, peeling off of the coating layer, and fracture of the needle base body, so as to reduce the probability of breakage and enhance the coating layer. Bonding force, the effect of preventing breakage accidents
- Summary
- Abstract
- Description
- Claims
- Application Information
AI Technical Summary
Problems solved by technology
Method used
Examples
preparation example Construction
[0038] The preparation process of the composite coating layer in the third step of the present invention is as follows: preparation of plating solution→priming plating→sand plating→thickening plating. The prepared electroplating solution is composed of NiSO 4 ·6H 2 O 250~350g·L -1 , NiCl 2 ·6H 2 O 35~50g·L -1 , H 3 BO 3 30-45g·L -1 , sodium lauryl sulfate 0.05~0.1g·L -1 .
[0039] The bottom plating in step 3 of the present invention includes impact plating and empty plating. The electroplating process parameters of impact nickel plating are: 2-4A / dm 2 , time 5-15min; electroplating process parameters for empty nickel plating: 0.5-3A / dm 2 , time 10-30min.
[0040] In the preparation of the diamond composite coating in step 3 of the present invention, an annular hollow electrolytic nickel column or four symmetrically distributed electrolytic nickel plates are used as anodes.
[0041] The upper sand plating in step 3 of the present invention is to add the upper san...
specific Embodiment approach 1
[0044] Specific implementation mode 1: Research on the heat treatment process after electroplating nickel on the surface of nickel-titanium alloy
[0045] The nickel-titanium alloy bur matrix is used as the research object, and the composition is Ti-50.8 at.% Ni. Before electroplating, the Nitinol sheet is pretreated.
[0046] (1) Pretreatment process
[0047] a. Insulate the non-plated part of the nickel-titanium alloy bur base with a thermoplastic tube.
[0048] b. Put the nickel-titanium alloy bur base into acetone solution, ultrasonically clean it for 15 minutes, and then rinse it with distilled water.
[0049] c. Containing NaOH 50g / l, Na 2 CO 3 40g / l, Na 3 PO 4 30g / l and Na 2 SiO 3 Carry out alkaline washing and degreasing in 5g / l lye, keep it warm for 20min at a temperature of 80°C, then wash under ultrasonic conditions for 10min, and rinse with distilled water.
[0050] d. In HF and HNO 3 The mixed solution (volume ratio HF (40wt.%): HNO 3 (65wt.%)=1:3)...
specific Embodiment approach 2
[0059] Specific implementation mode two: vacuum-encapsulate the electroplated nickel-titanium alloy bur base and then conduct heat treatment at a treatment temperature of 850° C., keep it warm for 60 minutes, and then cool in the furnace. Others are the same as the first embodiment.
[0060] The cross-section of the nickel-titanium alloy bur substrate after heat treatment was ground and polished with No. 1000 sandpaper, and the X-ray energy spectrum analyzer was used to detect the line of Ti and Ni elements on the interface between the nickel-plated layer on the cross-section and the nickel-titanium alloy substrate. Scan component analysis. The results show that when the nickel-titanium alloy substrate is used, a diffusion layer can be formed between the nickel plating layer and the substrate during heat treatment, and the interface bonding strength is greatly improved.
PUM
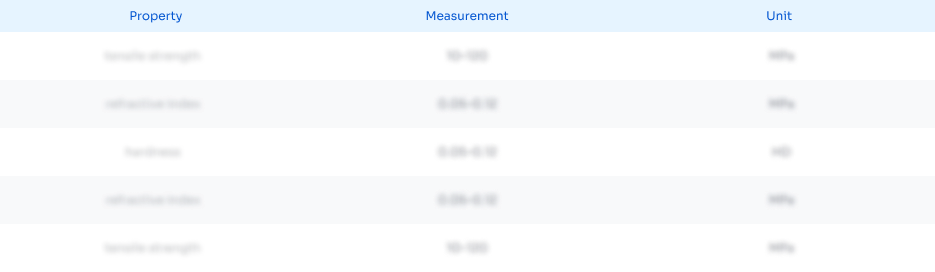
Abstract
Description
Claims
Application Information

- R&D
- Intellectual Property
- Life Sciences
- Materials
- Tech Scout
- Unparalleled Data Quality
- Higher Quality Content
- 60% Fewer Hallucinations
Browse by: Latest US Patents, China's latest patents, Technical Efficacy Thesaurus, Application Domain, Technology Topic, Popular Technical Reports.
© 2025 PatSnap. All rights reserved.Legal|Privacy policy|Modern Slavery Act Transparency Statement|Sitemap|About US| Contact US: help@patsnap.com