Aluminum melting furnace capable of improving service life and thermal efficiency
An aluminum smelting furnace and thermal efficiency technology, applied in the field of aluminum smelting furnaces, can solve the problems of falling bricks on the top of the furnace, aluminizing, and large heat loss of the furnace body.
- Summary
- Abstract
- Description
- Claims
- Application Information
AI Technical Summary
Problems solved by technology
Method used
Image
Examples
Embodiment 1
[0027] Embodiment 1 (15t aluminum smelting furnace)
[0028] a, choose to use the high-alumina refractory castable with SiC added as the working layer of the furnace lining (also known as the castable working layer); the addition of SiC is 10% of the weight of the refractory castable;
[0029] b. The surface temperature of the furnace shell is less than 30°C. The size of the furnace wall composite lining is determined to be refractory ceramic fiber + clay light-weight heat-insulating refractory brick + refractory castable = 20mm+114mm+230mm, and the thickness of the furnace wall lining is thicker than the original refractory brick The lining is thinned by 115mm;
[0030] c. The roof of the furnace adopts flat-top hanging type integral casting, and a layer of 20mm thick refractory fiber is laid on the pouring material, and the heating element is changed from the expensive nickel-chromium strip to the silicon carbon rod;
[0031] d. Carry out construction, maintenance and bakin...
Embodiment 2
[0036] Embodiment 2 (25t aluminum smelting furnace)
[0037] a. Choose to add Si 3 N 4 +β-Sialon's corundum refractory castable is used as the working layer of the furnace lining (also known as the castable working layer); Si 3 N 4 , β-Sialon are added in an amount of 5% of the weight of the refractory castable (Si 3 N 4 )3% (β-Sialon);
[0038] b. The surface temperature of the furnace shell is less than 30°C. The size of the furnace wall composite lining is determined to be refractory ceramic fiber + clay light-weight heat-insulating refractory brick + refractory castable = 40mm+180mm+230mm, and the thickness of the furnace wall lining is thicker than the original refractory brick The lining is thinned by 65mm;
[0039] c. The top of the furnace adopts flat-top hanging type integral casting, and a layer of 40mm thick refractory fiber is laid on the castable material, and the heating element is changed to use silicon carbon rods;
[0040] d. Carry out construction, mai...
Embodiment 3
[0045] Embodiment 3 (45t aluminum smelting furnace)
[0046] a. Choose to add Si 3 N 4 The mullite refractory castable is used as the working layer of the furnace lining (also known as the castable working layer); Si 3 N 4 The amount added is 6% of the weight of the refractory castable;
[0047] b. The surface temperature of the furnace shell is less than 30°C. The size of the furnace wall composite lining is determined to be refractory ceramic fiber + clay light-weight heat-insulating refractory brick + refractory castable = 40mm+180mm+230mm, and the thickness of the furnace wall lining is thicker than the original refractory brick The lining is thinned by 65mm;
[0048] c. The top of the furnace adopts flat-top hanging type integral casting, and a layer of 40mm thick refractory fiber is laid on the castable material, and the heating element is changed to use silicon carbon rods;
[0049] d. Carry out construction, maintenance and baking in strict accordance with the con...
PUM
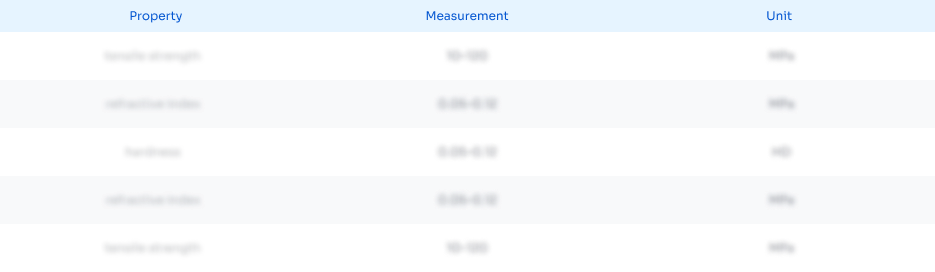
Abstract
Description
Claims
Application Information

- R&D Engineer
- R&D Manager
- IP Professional
- Industry Leading Data Capabilities
- Powerful AI technology
- Patent DNA Extraction
Browse by: Latest US Patents, China's latest patents, Technical Efficacy Thesaurus, Application Domain, Technology Topic, Popular Technical Reports.
© 2024 PatSnap. All rights reserved.Legal|Privacy policy|Modern Slavery Act Transparency Statement|Sitemap|About US| Contact US: help@patsnap.com