Method for preparing molybdenum-silicium-boron alloy
A boron alloy and alloy powder technology, applied in the field of preparation of molybdenum-silicon-boron alloy, can solve the problems of high oxygen content and other impurities, high cost, complicated operation and the like
- Summary
- Abstract
- Description
- Claims
- Application Information
AI Technical Summary
Problems solved by technology
Method used
Examples
Embodiment 1
[0013] Example 1: Weigh 85.2g molybdenum powder, 12.6g silicon powder and 2.2g boron powder respectively, and use a blender for uniform mixing treatment, and smelt in an arc melting furnace with a smelting working current of 700A. The smelted block The body is crushed and annealed. The annealing temperature is: 1200℃, and the time is: 1.0 hour. Then the annealed alloy powder is put into a graphite mold, and the mold is sintered in a spark plasma sintering furnace. Argon is used for sintering. Protected by gas atmosphere, the heating rate is 300℃ / min, the sintering temperature is: 1450℃, the sintering axial pressure is: 25MPa, the sintering holding time: 3min, after sintering, the mold is taken out after the furnace is cooled to 450℃, and cooled to At room temperature, after demolding, the obtained sintered body is processed to remove the surface layer by 0.3 mm, and the molybdenum-silicon-boron alloy material is obtained.
Embodiment 2
[0014] Example 2: Weigh 86.1g of molybdenum powder, 11.5g of silicon powder and 2.4g of boron powder, and use a blender for uniform mixing, and then smelt in an electric arc smelting furnace. The smelting current is 750A. The smelted block The body is crushed and annealed, the annealing temperature is: 1250℃, the time is: 1.0 hour, and then the annealed alloy powder is put into a graphite mold, and the mold is sintered in a spark plasma sintering furnace. Argon is used for sintering. Protected by gas atmosphere, the heating rate is 400℃ / min, the sintering temperature is: 1400℃, the sintering axial pressure is: 28MPa, the sintering holding time: 5min, after sintering, the mold is taken out after the furnace is cooled to 400℃, and cooled to At room temperature, after demolding, the obtained sintered body is processed to remove the surface layer by 0.3 mm, to obtain a molybdenum-silicon-boron alloy material.
Embodiment 3
[0015] Example 3: Weigh 87.5g molybdenum powder, 11.2g silicon powder and 1.3g boron powder respectively, use a blender for uniform mixing treatment, and smelt in an arc melting furnace with a smelting working current of 800A. The smelted block The body is crushed and annealed, the annealing temperature is: 1300℃, the time is: 1.0 hour, and then the annealed alloy powder is put into a graphite mold, and the mold is sintered in a spark plasma sintering furnace. Argon is used for sintering. Protected by gas atmosphere, the heating rate is 350℃ / min, the sintering temperature is: 1550℃, the sintering axial pressure is: 28MPa, and the sintering holding time: 3min. After sintering, the mold is taken out after the furnace is cooled to 400℃ and cooled to At room temperature, after demolding, the obtained sintered body is processed to remove the surface layer of 0.4 mm to obtain a molybdenum-silicon-boron alloy material.
PUM
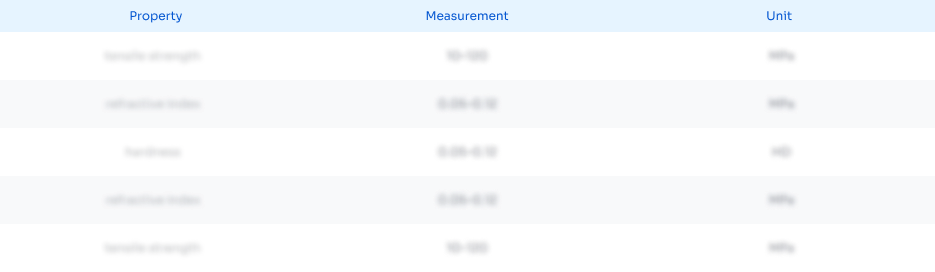
Abstract
Description
Claims
Application Information

- R&D
- Intellectual Property
- Life Sciences
- Materials
- Tech Scout
- Unparalleled Data Quality
- Higher Quality Content
- 60% Fewer Hallucinations
Browse by: Latest US Patents, China's latest patents, Technical Efficacy Thesaurus, Application Domain, Technology Topic, Popular Technical Reports.
© 2025 PatSnap. All rights reserved.Legal|Privacy policy|Modern Slavery Act Transparency Statement|Sitemap|About US| Contact US: help@patsnap.com