Process for comprehensively developing and utilizing nickel, cobalt, iron and magnesium from laterite-nickel ore
A technology of lateritic nickel ore and nickel-cobalt, which is applied in the direction of improving process efficiency, etc., can solve the problems of insufficient comprehensive utilization of resources and poor versatility, and achieve the effects of low cost, wide application range and complete scheme
- Summary
- Abstract
- Description
- Claims
- Application Information
AI Technical Summary
Problems solved by technology
Method used
Image
Examples
Embodiment 1
[0051]A. Add water according to the material-to-water ratio of 1:1 (wt) to ball-mill the laterite nickel ore and pass through a 100-mesh sieve. Take the -100 mesh slurry and pump it into the pressure reactor, pump water and hydrochloric acid (HCl content above 28%) respectively according to the liquid-solid ratio of 3.0:1 and the acid material (weight) ratio of 1.2:1, and stir for leaching.
[0052] B. Control of leaching conditions: stirring and leaching for 0.5 hours at 165°C (pressure not greater than 0.5MPa).
[0053] C. Filter while hot and wash the residue. The comprehensive leaching rates of valuable metals are: Ni+Co 92.1%; Mg 94.6%; Fe 3.1%.
Embodiment 2
[0055] A. Add water according to the material-to-water ratio of 1:2 (wt) to ball-mill the laterite nickel ore and pass through a 100-mesh sieve. Take -100 mesh slurry and pump it into the pressure reactor, pump water and hydrochloric acid (HCl content above 28%) respectively according to the liquid-solid ratio of 4.0:1 and the acid material (weight) ratio of 1.5:1, and stir for leaching.
[0056] B. Control of leaching conditions: stirring and leaching for 2 hours at 150°C (pressure greater than 0.35MPa).
[0057] C. Filter while hot and wash the residue. The comprehensive leaching rates of valuable metals are: Ni+Co 91.4%; Mg 95.2%; Fe 5.7%.
[0058] The laterite nickel ore is leached with hydrochloric acid under pressure. The contents of nickel and cobalt in the leaching solution (g / L) are: Ni+Co 2.27; Mg 33.5Fe2.16; the acidity of the leaching solution is: H + 0.82mol / L. The following examples are based on this leachate.
[0059] The valuable metal components (%) of th...
Embodiment 3
[0061] A. Pelletizing: Mix the water-containing leached slag, composite binder and reducing agent evenly, and granulate with a disc granulator. The composite binder is 80% sodium humate + 10% quicklime + 10% sodium carbonate, and the dosage is 3% of the dry weight of the leaching residue; the reducing agent is bituminous coal, and the dosage is 10% of the dry weight of the leaching residue.
[0062] B. Magnetization roasting: put the raw balls into the reduction roasting rotary kiln, the roasting temperature is 700°C, and the roasting time is 40 minutes.
[0063] C. Magnetic separation: the reduced cooked balls are crushed, ball milled, and passed through a 200-mesh sieve; the -200-mesh powder is magnetically separated with a weak magnetic separator, and the magnetic field strength of the magnetic separation is 100 Tesla; the iron content of the magnetic separation product is 58.4%; The iron yield was 76.3%.
PUM
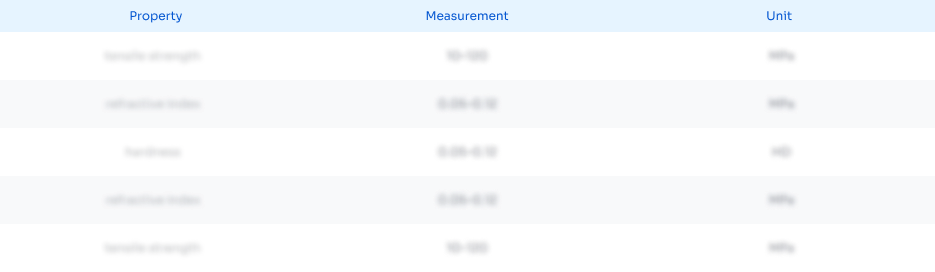
Abstract
Description
Claims
Application Information

- R&D
- Intellectual Property
- Life Sciences
- Materials
- Tech Scout
- Unparalleled Data Quality
- Higher Quality Content
- 60% Fewer Hallucinations
Browse by: Latest US Patents, China's latest patents, Technical Efficacy Thesaurus, Application Domain, Technology Topic, Popular Technical Reports.
© 2025 PatSnap. All rights reserved.Legal|Privacy policy|Modern Slavery Act Transparency Statement|Sitemap|About US| Contact US: help@patsnap.com