Method for reducing phosphorus in high phosphorus haematite or hematite and limonite ore by magnetization roasting-leaching method
A magnetized roasting and red limonite technology, applied in iron ore phosphorus reduction, high phosphorus hematite red limonite magnetization roasting-leaching phosphorus reduction field, can solve the fine particle size of phosphorus mineral embedding, which affects iron Concentrate quality and marketability, complexity and other issues
- Summary
- Abstract
- Description
- Claims
- Application Information
AI Technical Summary
Problems solved by technology
Method used
Image
Examples
Embodiment 1
[0016] Example 1: The raw material comes from a certain area in Sichuan. The ore is crushed to below -3mm, and 5% coke (particle size -1mm) by weight of the raw material is added and mixed, and the mixed material is magnetized and roasted in a roasting furnace. The roasting temperature is 900℃, and the roasting time is 15min. The roasted materials are water-quenched and then classified by grinding (-0.074mm accounts for 70%). The overflow of the classifier enters the permanent magnetic separator with a magnetic field strength of 1200 Oe to obtain magnetism. Iron ore concentrate, the magnetic iron ore concentrate is filtered, dehydrated and dried with a concentration of 10wt% hydrochloric acid with twice the weight of the dry ore, then stirred and leached for 15 minutes, the leaching solution is taken out for centralized treatment, the leaching residue is rinsed three times and then filtered and dehydrated After drying, iron concentrate is obtained. The beneficiation index of iron ...
Embodiment 2
[0024] Example 2: The test ore sample comes from a certain area in Yunnan. The sample is mainly hematite ore. The sample is powdery, with a relatively fine particle size and easy to silt. The ore is crushed to less than -5mm, and 8% is added at the same time After the coke (particle size -1mm) is mixed, the mixed materials are magnetized and roasted in a roasting furnace at a roasting temperature of 950°C and a roasting time of 20 minutes. The roasted materials are water-quenched and then graded by grinding (-0.074mm accounts for 70.12%), the overflow of the classifier into the magnetic field intensity is 1000O e The magnetic separation iron ore is obtained after magnetic separation by the permanent magnetic separator. The magnetic separation iron ore is filtered, dehydrated and dried with 12wt% hydrochloric acid, mixed with water of twice the dry weight of the ore, and then stirred and leached for 15 minutes, and the leachate is taken out After intensive processing, the leaching ...
Embodiment 3
[0031] Example 3: The test ore sample comes from a high-phosphorus hematite from a certain place in Shaanxi Province. The sample is in block shape and has a relatively large hardness. The original ore has a finer grain size and a compact shape. It is a difficult to crush and easy to grind ore, but the ore is ground. In the process, sludge is easy to occur. The ore is crushed to below -3mm, and 6% coke (particle size -1mm) is added at the same time. After mixing, the mixed material is magnetized and roasted in a roasting furnace at a roasting temperature of 1000°C. , The roasting time is 10min, the roasted material is water-quenched and then classified by grinding (-0.074mm accounts for 75.12%), the overflow of the classifier enters the magnetic field with a strength of 1200O e The magnetic separation iron ore is obtained after magnetic separation by the permanent magnetic separator. The magnetic separation iron ore is filtered, dehydrated and dried with 20wt% sulfuric acid, mixed ...
PUM
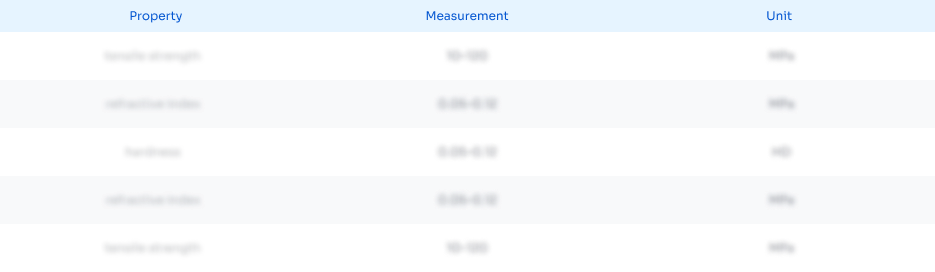
Abstract
Description
Claims
Application Information

- R&D Engineer
- R&D Manager
- IP Professional
- Industry Leading Data Capabilities
- Powerful AI technology
- Patent DNA Extraction
Browse by: Latest US Patents, China's latest patents, Technical Efficacy Thesaurus, Application Domain, Technology Topic, Popular Technical Reports.
© 2024 PatSnap. All rights reserved.Legal|Privacy policy|Modern Slavery Act Transparency Statement|Sitemap|About US| Contact US: help@patsnap.com