Negative temperature coefficient two-phase composite thermistor composition and preparation thereof
A technology of negative temperature coefficient and heat-sensitive material, applied in the field of negative temperature coefficient dual-phase composite heat-sensitive sensor material and its preparation, can solve the problems of difficult high resistivity, low resistivity, unfavorable material stability, low resistivity, etc. The effect of improved mechanical strength, good matching and good thermal stability
- Summary
- Abstract
- Description
- Claims
- Application Information
AI Technical Summary
Problems solved by technology
Method used
Image
Examples
Embodiment 1
[0013] Embodiment 1: (Fe 1.0 Cu 0.4 Ni 1.32 mn 3.28 o 8 )(YSZ) 1.5 preparation and testing of
[0014] Fe used in this example 1.0 Cu 0.4 Ni 1.32 mn 3.28 o 4 The powder is obtained by calcining the compound oxalate produced by solid-phase reaction at room temperature: the molar ratio of analytically pure copper acetate, iron oxalate, manganese acetate, nickel acetate, and oxalic acid is 0.4:1:3.28:1.32: 7.2. Use an analytical balance to weigh the above-mentioned substances of corresponding quality, mix the above-mentioned substances with zirconia balls in ethanol and ball mill for 1 day. The milling time should not be too short. Insufficient ball milling will lead to poor powder consistency. Lengthening can make the particle size of the powder smaller. In the present invention, powders with medium particle size are selected, and the ball milling time is generally selected to be 1 to 2 days. The ball milling time used in this example was 1 day; the obtained composit...
Embodiment 2
[0023] Embodiment 2: (Fe 1.0 Cu 0.4 Ni 1.32 mn 3.28 o 8 )(YSZ) 4 preparation and testing of
[0024] This example adopts the same preparation method as Example 1, the difference is that: the single-phase powder calcining condition is 850°C for 4h; the dual-phase powder ratio Fe 1.0 Cu 0.4 Ni 1.32 mn 3.28 o 8 :YSZ is 1:4, the ball milling time is 2 days, and the sintering temperature of the composite powder is increased to 1250°C, the particle size of the powder prepared under this condition is slightly smaller, 50-60 μm.
[0025] The same method as in Example 1 is used to carry out X-ray and scanning electron microscope tests on the sintered dual-phase composite material in this example. The results show that the single-phase powder obtained in this example is a spinel phase with a cubic structure; The phase composite material is composed of a cubic structure spinel phase and a cubic structure YSZ phase. The cubic spinel phase with a small mole fraction is evenly dis...
Embodiment 3
[0028] Embodiment 3: (Fe 1.0 Cu 0.3 Ni 1.32 mn 3.38 o 8 )(YSZ) 1.5 preparation and testing of
[0029] This example adopts the same preparation method as Example 1, the difference is that: the calcination condition of the single-phase powder is 800°C for 2h; the molar ratio of the two-phase powder is changed to Fe 1.0 Cu 0.3 Ni 1.32 mn 3.38 o 8 :YSZ is 1:1.5.
[0030] The same method as in Example 1 is used to carry out X-ray and scanning electron microscope tests on the sintered dual-phase composite material in this example. The results show that the single-phase powder in this example is a spinel phase with a cubic structure; the dual-phase composite The material is composed of a cubic structure spinel phase and a cubic structure YSZ phase. The cubic spinel phase with a small mole fraction is evenly distributed in the cubic phase YSZ with a large mole fraction, and forms a percolation network. The crystal of the spinel phase The particle size is 1-2 μm.
[0031] ...
PUM
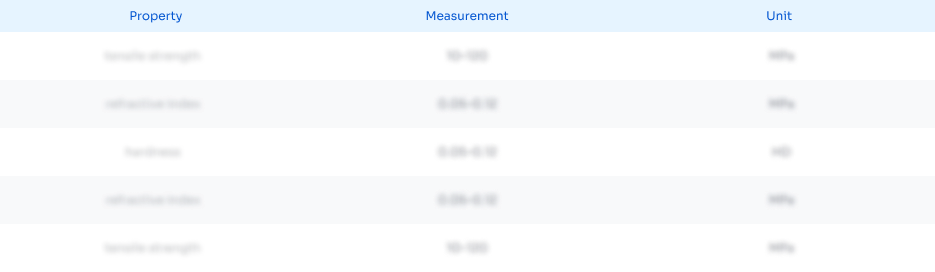
Abstract
Description
Claims
Application Information

- R&D Engineer
- R&D Manager
- IP Professional
- Industry Leading Data Capabilities
- Powerful AI technology
- Patent DNA Extraction
Browse by: Latest US Patents, China's latest patents, Technical Efficacy Thesaurus, Application Domain, Technology Topic, Popular Technical Reports.
© 2024 PatSnap. All rights reserved.Legal|Privacy policy|Modern Slavery Act Transparency Statement|Sitemap|About US| Contact US: help@patsnap.com