Silicon nitride composite ceramics heater
A technology of composite ceramics and silicon nitride, which is applied in the field of silicon nitride composite ceramic heating elements, can solve the problems that the point temperature difference range is not too wide, the thermal shock performance needs to be further improved, and the thermal conductivity of the heating element is not too high, so as to achieve the thermal conductivity Improvement, safe and reliable use, good thermal shock resistance
- Summary
- Abstract
- Description
- Claims
- Application Information
AI Technical Summary
Problems solved by technology
Method used
Examples
Embodiment 1-4
[0007] (1) Preparation of raw materials: weigh the ingredients according to the ratio in Table 1, vibrate and ball mill for 8 hours, unload, sieve, bake at a constant temperature, and make wax cakes with wax, and seal them for preservation.
[0008] (2) Biscuit preparation: Process the metal mold according to the shape requirements of the heating element, and prepare the biscuit by hot die casting.
[0009] (2) Sintering: The prepared biscuit is loaded into a mold, loaded into a furnace, dewaxed, hot-pressed under the protection of flowing nitrogen, and heated at a constant speed. 250kg / cm 2 . After reaching the firing temperature, keep the temperature and pressure constant for 1 hour, then lower the temperature and keep the pressure down to 1550°C, then cut off the power and shut down the furnace. 2.5 hours to 3 hours after power failure and furnace shutdown, it will be released from the furnace for demoulding, and the initial inspection and inspection will be carried out t...
PUM
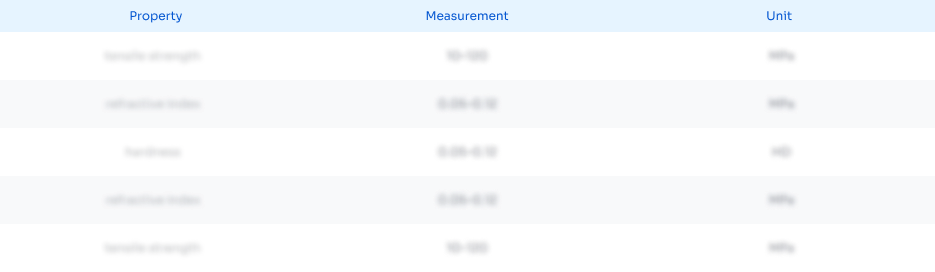
Abstract
Description
Claims
Application Information

- R&D
- Intellectual Property
- Life Sciences
- Materials
- Tech Scout
- Unparalleled Data Quality
- Higher Quality Content
- 60% Fewer Hallucinations
Browse by: Latest US Patents, China's latest patents, Technical Efficacy Thesaurus, Application Domain, Technology Topic, Popular Technical Reports.
© 2025 PatSnap. All rights reserved.Legal|Privacy policy|Modern Slavery Act Transparency Statement|Sitemap|About US| Contact US: help@patsnap.com