Heat sink material for power device and preparation method thereof
A technology for heat sink materials and power devices, applied in the field of components of power devices, to achieve the effects of small thermal expansion rate, good thermal conductivity, and directional thermal conductivity
- Summary
- Abstract
- Description
- Claims
- Application Information
AI Technical Summary
Problems solved by technology
Method used
Image
Examples
Embodiment 1
[0032] As shown in Figure 1, it is the internal structure diagram of the tungsten-copper alloy after sintering and infiltration provided by the present invention, including a skeleton 1 made of metal tungsten wrapped by a metal nickel plating layer 3 and infiltrated in the skeleton. Metal copper 2. The tungsten-copper alloy of this structure is prepared through the following procedures.
[0033] The first step of mixing
[0034] Take 20 kg and 60 kg of tungsten powder with a particle size of 4-6 microns, and 1.2 kg of stearic acid, and put them into a ball mill and mix them for 1 hour.
[0035] The second step of compression molding
[0036] Take 1.26 kg of mixed tungsten powder and divide it into seven parts and 0.20 kg of copper fiber with a diameter between 50-200 microns and divide it into six layers and place them in a mold of 50 mm × 100 mm for pressing; Press for 2 to 4 minutes.
[0037] The third step sintering infiltration
[0038] Wrap the pressed tungsten blank...
Embodiment 2
[0042] Example 2
[0043] The first step of mixing
[0044] Take 20 kg and 60 kg of tungsten powder with a particle size of 3-4 microns and 6-8 microns, 2 kg of copper powder with a particle size of 10-20 microns, and 1.5 kg of stearic acid into a ball mill and mix them for 1 Hour.
[0045] The second step of compression molding
[0046] Take 1.26Kg of uniformly mixed tungsten-copper powder and divide it into seven parts, take 0.0378 kg of metallic copper, and make six layers of copper skin with a specification of 50 mm × 100 mm × 200 microns. Press and form in a mold of ×100 mm; the pressing pressure is controlled by pressing the thickness of the billet to 20 mm, and the pressure is maintained for 2 to 4 minutes.
[0047] The third step sintering infiltration
[0048] Put the pressed tungsten-copper billet into the sintering furnace and pre-fire at 150°C for 5 minutes, then sinter and infiltrate at 1400°C for 50 minutes under the protection of hydrogen;
[0049] The four...
Embodiment 3
[0053] In order to further improve the thermal conductivity of the heat sink material for power devices, as shown in Figure 3, a unidirectional fiber structure layer 5 consisting of six layers of copper is sandwiched between seven layers of tungsten-copper alloy layers 4. When in use, its heat can not only be exported through the copper that forms the conjoined structure 2 by infiltration, but also be exported along the direction of the unidirectional fiber, so it has directional heat conduction characteristics, and its preparation process is:
[0054] The first step of mixing
[0055] Take 20 kg and 60 kg of tungsten powder with a particle size of 1-2 microns and 6-8 microns, 15 kg of copper powder with a particle size of 10-20 microns, and 2.0 kg of stearic acid into a ball mill for stirring and mixing. 70 minutes.
[0056] The second step of compression molding
[0057] Take 1.4Kg of uniformly mixed tungsten-copper powder and add it to a 50mm×100mm mold in 7 times. Lay a...
PUM
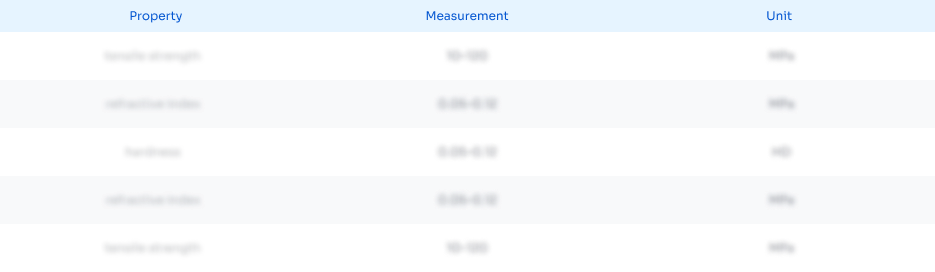
Abstract
Description
Claims
Application Information

- R&D
- Intellectual Property
- Life Sciences
- Materials
- Tech Scout
- Unparalleled Data Quality
- Higher Quality Content
- 60% Fewer Hallucinations
Browse by: Latest US Patents, China's latest patents, Technical Efficacy Thesaurus, Application Domain, Technology Topic, Popular Technical Reports.
© 2025 PatSnap. All rights reserved.Legal|Privacy policy|Modern Slavery Act Transparency Statement|Sitemap|About US| Contact US: help@patsnap.com