CO hydrogenation synthesizing reaction metallic carbide catalyst and preparation and application
A metal carbide and bimetallic carbide technology, applied in the field of metal carbide catalysts, can solve the problems of low activity and poor selectivity of higher alcohols, and achieve high C2+OH selectivity, lower production costs, and excellent sulfur resistance. Effect
- Summary
- Abstract
- Description
- Claims
- Application Information
AI Technical Summary
Problems solved by technology
Method used
Image
Examples
Embodiment 1
[0031] Ammonium molybdate ((NH 4 ) 6 Mo 7 o 24 .24H 2 O) 10.0g was calcined at 450°C in air for 4 hours, and the obtained MoO 3 Grind it into a powder smaller than 0.3 mm, put it into a quartz reactor, use methane:hydrogen gas with a volume ratio of 1:4 as the carbonization medium, and feed 1.0 g of precursor into the reactor at a flow rate of 30 mL / min. Two-stage temperature program control is adopted, the temperature rise rate is 5°C / min from room temperature to 400°C, and the temperature rise rate is 1°C / min from 400°C to the final temperature of 650°C. Concentration of 0.5% O 2 / N 2 Mixed gas passivation for 3 hours to get molybdenum carbide. Alkali metal modification using K 2 CO 3 is the K source, K 2 CO 3 The molar ratio of molybdenum carbide to molybdenum carbide is 0.2, the K source is introduced by equal volume impregnation method, and then roasted in an inert atmosphere Ar at 600 ° C for 2 hours and then lowered to room temperature, using O with an oxygen...
Embodiment 2
[0033] Ammonium tungstate ((NH 4 ) 6 W 7 o 24 .24H 2 O) 17.9g was roasted at 550°C in air for 3 hours, and the resulting WO 3 Grind it into a powder less than 0.3 mm, put it into a quartz reactor, use a mixed gas with a volume ratio of ethylene:hydrogen of 1:6 as the carbonization medium, and feed 1.0 g of precursor into the reactor at a flow rate of 50 mL / min. Two-stage temperature program control is adopted, the temperature rise rate is 10°C / min from room temperature to 400°C, and the temperature rise rate is 1.5°C / min from 400°C to the final temperature of 750°C. 2 rapidly cooled to room temperature, and then the oxygen concentration was 1.0% O 2 / N 2 Mixed gas passivation for 5 hours to obtain tungsten carbide. Alkali metal modification uses NaOH as the Na source, the molar ratio of NaOH to tungsten carbide is 0.5, the Na source is introduced by the equal volume impregnation method, and then in an inert atmosphere N 2 After roasting at 500 ° C for 3 hours, it was l...
Embodiment 3
[0035] Ammonium chromate ((NH 4 ) 2 CrO 4 )8.5g was roasted in the air at 600°C for 2.5 hours, and the obtained CrO 3 Grind it into a powder less than 0.3 mm, put it into a quartz reactor, use a CO: hydrogen gas mixture with a volume ratio of 1:8 as the carbonization medium, and feed 1.0 g of precursor into the reactor at a flow rate of 80 mL / min. Two-stage temperature program control is adopted, the temperature rise rate is 15°C / min from room temperature to 400°C, and the temperature rise rate is 0.5°C / min from 400°C to the final temperature of 800°C. Concentration of 1.5% O 2 / He mixed gas passivation for 8 hours to get chromium carbide. Alkaline earth metal modification with Ca(CH 3 COO) 2 is the source of Ca, Ca(CH 3 COO) 2 The molar ratio to chromium carbide was 0.1, the Ca source was introduced by physical mixing method, and then calcined at 450 °C for 4 hours in an inert He atmosphere, and then lowered to room temperature, using O with an oxygen volume concentra...
PUM
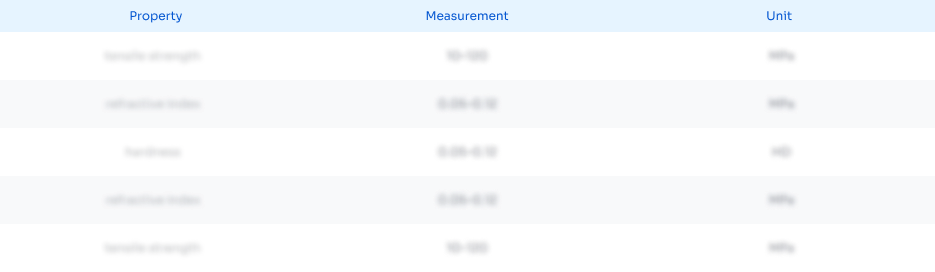
Abstract
Description
Claims
Application Information

- R&D
- Intellectual Property
- Life Sciences
- Materials
- Tech Scout
- Unparalleled Data Quality
- Higher Quality Content
- 60% Fewer Hallucinations
Browse by: Latest US Patents, China's latest patents, Technical Efficacy Thesaurus, Application Domain, Technology Topic, Popular Technical Reports.
© 2025 PatSnap. All rights reserved.Legal|Privacy policy|Modern Slavery Act Transparency Statement|Sitemap|About US| Contact US: help@patsnap.com